
Canada’s steel industry is witnessing significant changes as some of its steelmakers transition from blast furnace (BF) and basic oxygen furnace (BOF) methods of primary steelmaking to a more sustainable manufacturing process using electric arc furnaces (EAFs).
According to the Brussels-based World Steel Association, Canada’s annual steel production capacity was approximately 12.3 million metric tons in 2023, a 1.3 percent increase from 2022. Nearly 42 percent of this capacity was produced via EAF technology.
The bulk of Canada’s steel furnaces are in Ontario and Montreal, with a few others scattered across the rest of the country. Hamilton, Ontario— described as the “steel capital” of Canada—houses ArcelorMittal Dofasco and Stelco, two of the larger domestic steelmakers, while Algoma Steel is a six-hour drive north in Sault Ste. Marie, Quebec.
Luxembourg-based ArcelorMittal also has a presence in Quebec, and Brazil-based Gerdau operates an EAF in Whitby, Ontario, making that province an important North American steelmaking cluster.
While Gerdau currently maintains one of Ontario’s largest EAFs, Algoma and ArcelorMittal Dofasco are setting up similar furnaces that will change the country’s steelmaking landscape in terms of sustainability. The market dynamics for ferrous scrap, a major raw material used by EAFs, also will be affected.
Canada generates large volumes of ferrous scrap every year from end-of-life vehicles and demolition projects. The country exported 1.87 million metric tons from January to May of this year, 13 percent less than the 2.16 million metric tons it exported a year ago, of which 1.35 million metric tons went to the U.S.
The question is whether domestic scrap consumption and exports will change significantly after Canada increases its share of EAF production in steelmaking.
Steelmakers embrace EAFs
Algoma nearly has completed its EAF project, which is expected to be commissioned later this year, with its first steel output to be produced in the first quarter of 2025. Once commissioned, the plant is expected to produce some 3.7 million tons of steel, reducing Algoma’s carbon emissions by 70 percent annually.
The firm also has set up ATM Metals, a joint venture with Brampton, Ontario-based Triple M Metal, to source ferrous scrap. ATM plans to start procuring substantial volumes of scrap for the EAF in the second half of 2025.
Once Algoma begins buying for its new furnace, the increase in its ferrous scrap requirements might not be significant for the first couple years. Currently, it buys around 360,000 tons annually, according to one estimate.
With the new furnace, expected to produce up to 1.6 million tons annually, and running at 30 percent to 40 percent hot metal from the BF, which is set to close by decade’s end, Algoma’s scrap demand likely will increase to around 960,000 tons to 1.02 million tons per year, an industry source predicts.
Once the BF shuts down, Algoma will need significantly more ferrous scrap, potentially impacting the market, and concerns exist about the availability of material for its target production of up to 3.5 million tons.
Meanwhile, ArcelorMittal has started building a 2.5 million-ton-per-year direct-reduced iron (DRI) plant and an EAF with an annual capacity of 2.4 million tons at its Dofasco facilities in Ontario.
Construction is expected to be completed in 2026, and the production phase for DRI will start after a transition phase of 12 to 18 months. The EAF will produce high-quality steel using existing rolling and finishing equipment at the ArcelorMittal Dofasco plant along with the new DRI plant production.
“Economic development, sustainability and reduced emissions are the key factors driving the government’s promotion of EAFs,” says Paul Fogolin, president and CEO of the Canadian Association of Recycling Industries, or CARI, Oakville, Ontario.
Fogolin says ferrous scrap will be a significant part of the feedstock for EAFs, noting that a potential increase in demand in Canada could chip away at exports and potentially drive up the market.
He also points out that the shift to green steel will benefit the industry and could lead to more optimized feed mixes.
“Ferrous scrap is often more cost-effective than producing steel from pure iron ore,” Fogolin says. “With less raw material input required, EAFs lower the impact on the environment with less mining and energy consumption.”

Stronger demand for ferrous
The majority of buyers and sellers in the Canadian ferrous scrap market who have weighed in on demand trends for ferrous after the EAFs ramp up say competition for the material will increase in the coming years.
One buyer notes that as the market approaches equilibrium, mills in Ontario will run at a ferrous scrap deficit. At that point, mills would have to look east and into Quebec, the Maritimes and even upstate New York for supply. Traders also say it will become harder to source ferrous scrap, despite higher inflows to scrap yards. Moreover, if mills in Ontario offer higher prices, ferrous exports from Canada will shrink.
However, Fogolin strikes a more tempered approach on domestic ferrous scrap consumption.
“Although the assumption would be that mills would need more recycled material to feed their furnaces, the melt mix for these new EAFs is currently uncertain,” he says.
Fogolin also counters that as EAFs are more energy efficient, they could consume less scrap.
Additionally, integrated mills that transform raw iron ore into steel already procure 20 to 30 percent scrap, which they add to their feedstock. This share likely would remain unchanged, which could further understate an increase in scrap demand.
Prime grades could be winners
Sheet mills require higher-quality raw materials compared with bar mills, which usually have an ample supply of obsolete scrap. The EAF mix for sheet production typically includes 60 percent prime grades (such as No. 1 bundles and No. 1 busheling), 20 percent pig iron and 20 percent obsolete grades (such as No. 1 HMS, or heavy melt scrap, and 5-foot plate and structural, or P&S).
Global dynamics come into play here. Turkey relies heavily on the U.S. for ferrous scrap, prompting some Turkish steelmakers to set up sourcing units in North America. However, given the shortage of prime scrap for export in the U.S., Turkey increasingly supplements its supply from Canada.
Mills already are anticipating more demand for higher-quality ferrous grades, such as No. 1 busheling, which are preferred for the production of flat steel in Canada.
These sentiments are echoed by Boston Consulting Group, which has released a report indicating Canada’s exports of prime grades to the U.S. could decrease 50 percent by 2030 because of growing domestic demand.
Ontario, currently a surplus market for prime scrap, is expected to meet much of the increased demand for prime grades. As a result, prices for prime scrap likely will increase as mills compete for available supply, resulting in these mills facing higher costs to secure their share of the material.
Sponsored Content
Still relying on manual sorters?
Let AI do the heavy lifting. Waste Robotics delivers reliable, high-performance robots tailored for complex waste streams. They require minimal maintenance, are easy to operate, and are designed to boost your recovery rates. Smarter sorting starts with the right partner. Waste Expo Booth #1969 & REMA #2843
Click here to see our robots in action!Sponsored Content
Still relying on manual sorters?
Let AI do the heavy lifting. Waste Robotics delivers reliable, high-performance robots tailored for complex waste streams. They require minimal maintenance, are easy to operate, and are designed to boost your recovery rates. Smarter sorting starts with the right partner. Waste Expo Booth #1969 & REMA #2843
Click here to see our robots in action!Green steel legislation
The Canadian Net-Zero Emissions Accountability Act, which was enacted in June 2021, legally commits Canada to achieving net-zero emissions by 2050. The act mandates transparency and accountability as the government progresses toward its emissions targets.
Canada has invested approximately CA$1.3 billion ($946 million) for the BOF-to-EAF conversions at Algoma and Dofasco, which drastically will increase the country’s share of EAF steel production in the future.
Fogolin says that while the Canadian government has not yet enacted specific green steel legislation, the possibility still exists. His stance is that government support for EAF projects thus far has been not just about lowering emissions but also with an eye toward regional economic development by funding manufacturing, which brings jobs to smaller and midsize communities.
“The influence of carbon taxes in steering the industry toward green steel also cannot be understated,” Fogolin says. “While this is not specifically green steel legislation, the issue heavily influences political discourse and affects various manufacturing methods, including steel production.”
A major concern is that most of the pollution and emissions in steel production stems from the BF and coking processes. If mills converting to EAFs don’t completely phase out these processes, the benefits of their transition to greener practices could be minimal.
Impact on the U.S. market
U.S. Midwestern mills are large consumers of ferrous scrap from Ontario and purchase up to 2 million tons annually from Canada.
With new EAFs coming online, participants are confident this number could shrink as local Ontario-based yards find large purchasers in Algoma and Dofasco, apart from Gerdau, which already purchases ferrous scrap for its EAF. Many eagerly await this development as it would tighten availability within the Midwest market, thereby driving up prices.
Some market participants predict that in the event of a ferrous scrap shortfall in Ontario, mills in the U.S. could need to source material from other markets, causing potential disruptions for up to six months. They could turn to areas such as Cleveland and Chicago, which have excess busheling supply. Canadian mills like Algoma and others also could increasingly source from these regions, along with Ontario and Detroit, to meet their supply needs.
“At the end of the day, everyone in the industry is driven by maximizing outputs and reducing input costs,” Fogolin says. “Economics will drive the eventual melt mix.”
He notes it’s fair to say Canada likely will become less of an exporter of recycled steel after its new EAF steelmaking capacity comes online.Get curated news on YOUR industry.
Enter your email to receive our newsletters.
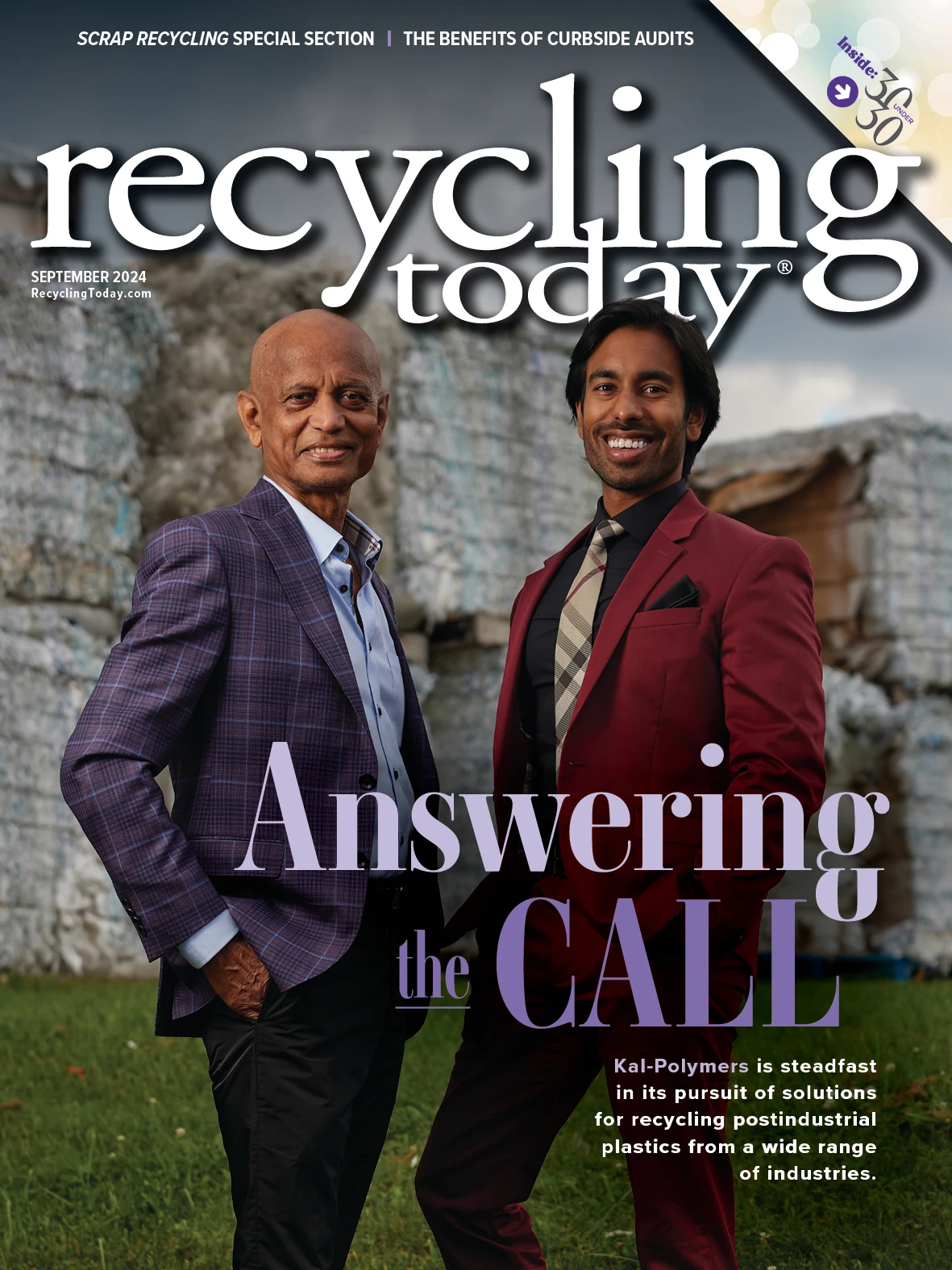
Explore the September 2024 Issue
Check out more from this issue and find your next story to read.
Latest from Recycling Today
- Circular by Shapiro releases "5 for Five" sustainability series
- Graphic Packaging set to close Ohio CRB facility
- Ameripen voices support for Maryland EPR bill
- Matalco to close Canton, Ohio, plant
- Maryland county expands curbside recycling to include electronics
- California EPS ban will be enforced
- YKK AP America introduces BetterBillet
- Fresh Perspective: Cameron Keefe