
The motto at Jamestown Plastics is if you can heat a type of plastic and make it pliable, the company can work with it.
In its 65th year, the Brocton, New York-based thermoformer has lived up to that ethos, supplying packaging and products made from a wide range of plastics for customers in numerous industries, such as automotive, medical, electronics and consumer goods.
“We don’t like to say no to a good opportunity,” says Jay Baker, CEO of family-owned and -operated Jamestown Plastics. “That’s how we view customer relations. First and foremost, we look at who the customer is. Then, we look at what the project is and how the customer is wired.”
Sustainability is also wired into the company’s thinking as it serves its customer base. Jamestown works with recycled resins such as postindustrial and postconsumer polyethylene terephthalate (PET), polyvinyl chloride (PVC), high-impact polystyrene (HIPS) and acrylonitrile butadiene styrene (ABS) when product specifications allow, and the company recycled more than 350,000 pounds of plastic scrap generated in its manufacturing processes in 2023 alone.
The company also holds more than 20 forming-related, solution-based patents granted in 44 countries, including its popular Clamtainer line of clamshell containers and its Click-It Closure technology for product labeling—both primarily made of PET.
“We do things in our operation that nobody else in the world does," Baker says.

Family atmosphere
The company was founded in 1958 in Jamestown, New York, and its initial customer base was focused on preservation packaging for military bearings, durable commercial products and retail consumer goods.
In 1972, Jamestown Plastics was sold to Erie, Pennsylvania-based Prescotech, and James Baker, Jay’s father, was named the company’s vice president and general manager. In 1976, James and his wife, Jacqueline, purchased Jamestown Plastics from Tannetics Corp., the company that previously acquired Prescotech. Jay joined the company out of college as its first full-time salesperson in 1984 and succeeded his father as president in 1999.
In 2021, Jay named his son, Jessup Baker, the company’s third-generation president and transitioned to his current role as CEO. Jessup oversees the day-to-day operations of the business.
In the years since the Baker family took over leadership of Jamestown Plastics, the company moved from its 10,000-square-foot facility in Jamestown to a 100,000-square-foot site in Brocton in 1986, then added a second, 35,000-square-foot processing facility in Brownsville, Texas, in 1996. There, the company performs the same tasks, using a number of in-line thermoforming lines.
In 2022, Jamestown purchased Meadville, Pennsylvania-based Tamarack Products Ltd. and its 20,000-square-foot plant. Jay says the Meadville location is used primarily for light-gauge thermoforming, vinyl applications and silk screening, among other processes.
“We stepped in, and [the Meadville operation] has grown and flourished, and we’ve expanded upon some of the things that [Tamarack] did, such as the flexible vinyl operations,” Baker says. “We’ve expanded on the technology there and added equipment to broaden the market.”
The company has around 200 employees, and Baker estimates that about 50 percent of that workforce has been employed for more than two decades, including multiple generations of families.
“We have extremely low turnover,” he says. “We have very long-tenured employees. We consider ourselves a family business, and that doesn’t mean your last name has to be Baker. I think the fact that we have the third generation [of some families] coming along in our operations indicates that our employees must have a reciprocal feeling because I don’t think you’re going to get your child and your grandchild to follow in your footsteps if you [don’t like the job].
“We hire on the basis of attitude. We’ve been doing this long enough that we have grandchildren of employees working for us and doing a great job. I will hire on attitude first and foremost, and if you’re willing to learn, then we’ll figure out a role for you.”

Finding solutions
Jamestown Plastics’ can-do mentality applies to the wide range of industries it works with as well as the many types of plastic it can develop.
At its three facilities, the company can make products from light- and heavy-gauge materials that include PET, PVC, HIPS, ABS and many other plastics, including polypropylene, high- and low-density polyethylene, thermoplastic polyolefin, polycarbonate, nylons, polyethylene terephthalate glycol and amorphous PET.
Baker says Jamestown Plastics sources material domestically in sheet or rolled sheet form, depending on that plastic’s thickness, from a variety of compounders and extruders, noting that a typical roll measures about 32 inches wide and 30 inches in diameter and weighs about 750 pounds. Jamestown Plastics also purchases custom-made rolls that can be as narrow as 16 inches with a diameter of 24 inches and a 100-pound weight.
“It depends on the application, and it depends on the volume,” Baker says. “Within that realm, 125 pounds would be a really small roll, and 750 pounds would be a really big roll in that range.”
Jamestown Plastics can perform a variety of manufacturing processes for customers across its facilities and has multiple ISO-certified clean rooms used for the manufacturing of medical device trays, sensitive electronic packaging, life science products and other products that require precise control of particulate and contamination.
Among the company’s capabilities are high-speed in-line thermoforming lines with robotic automation; high-speed computer numerical control machining capabilities for precise and efficient parts; high-precision robotic trimming that employs router, water jet and laser jet technologies; multiple component assembly technologies, including ultraviolet-activated adhesives, mechanical fastener systems, ultrasonic bonding, radio frequency bonding, welding, folding and bending, hook and loop fasteners, automotive foam tape and more; and decorating, including foil hot stamping, silk screening and pad printing.
“Our philosophy also is to control everything we can control,” Baker says. “We do soup to nuts, from design to tooling, everything’s in-house. We don’t buy outside tooling; we do all of our design in-house. We control the process and keep our promises.”
In the consumer goods space, the company has designed products that include clamshell and blister packaging, insert trays for cosmetics applications, signage and point-of-sale purchase displays and merchandisers. For industrial uses, the company has developed products such as dunnage trays and hazardous materials packaging. Its automotive products have included interior and exterior trim components, mud flaps, bumper guards and in-vehicle organizing and storage systems.
In 2012, for example, Jamestown Plastics designed a hood liner for the Tesla Model S introduction.
Sustainability-minded

for thermoforming
Baker says Jamestown Plastics increasingly has added postindustrial and postconsumer resin—primarily recycled PET, or rPET—to certain products.
Approximately 40 percent of the material the company purchased in 2023 included some amount of recycled content, and 32 percent of that was rPET. In 2023, Jamestown recycled 353,345 pounds of plastic scrap, recovering 81 percent of the total scrap produced from its manufacturing processes. In its 2023 sustainability report, Jamestown Plastics says its New York and Texas plants diverted more than 1.7 million pounds of plastic from landfills since 2021.
The company’s patented Clamtainer, a line of clamshell containers the Bakers first designed in 2016, can be made with up to 100 percent rPET and has been a popular product in a wide range of packaging applications. Baker says the Clamtainer is childproof, available in different sizes and primarily has been sold to customers in the hardware sector for items such as nuts and bolts and in the cannabis sector. The company is looking to enter the containers into the food product space, where they could store anything from berries to bakery items.
When used with the company’s Click-It Closure for product labeling, which is designed for easy removal from the container itself, Baker says Jamestown Plastics’ version of a clamshell offers a longer life than a traditional package.
“Every container is reusable,” he says. “That’s our first mantra. It’s not packaging, it’s a container that’s serving the role of packaging in its first iteration, and then the consumer is going to keep using it, especially if it’s a product you’re not going to use all at once.”
Because the Click-It is removable from the Clamtainer as opposed to traditional packaging that is “engulfed in plastic,” Baker says the company’s production results in 50 percent less plastic usage compared with traditional packaging. The labeling “card” housed in the Click-It can be recycled with paper products.
The company also has closed the loop in its operations by ensuring its manufacturing scrap finds a new life. It grinds its manufacturing scrap into flake, then tests it to make sure it is pure and free of contamination. It then sells that flake to processors, including compounders and extruders it works with, to be turned back into sheet for thermoforming.
“When it comes to recycling on the industrial side for us, we recycle virtually everything,” Baker says, “unless it’s a type of material [that can’t be recycled], such as a laminate material for some automotive applications.”
In order to create more sustainable operations, the company has invested in equipment upgrades, which have lowered Jamestown Plastics’ energy consumption, Baker says, and installed newer heating and air conditioning systems.
In its sustainability report, the company notes that it has decreased its Scopes 1 and 2 CO2 equivalent emissions by 23.9 percent and 38.2 percent, respectively, since 2021.
Foray into medical
Jamestown Plastics began manufacturing products for the medical packaging industry in 1997 and steadily has gained traction in a space that could be considered nontraditional in its approach to sourcing those products.
The thermoformer custom manufactures a variety of health care packaging for devices as well as unit dose, blister, clamshell and child-resistant packaging; light- and heavy-gauge device trays and tray systems; returnable totes; medical carts; lock boxes; and other components.
The medical product sector has a high barrier to entry, Baker says, because the industry can be viewed as risk-averse.
“For obvious reasons, one mistake can literally be life or death,” he says, adding that when it comes to using more proven products, it’s an industry that believes “if it ain’t broke, don’t fix it.”
Baker notes that even though medical packaging can be a difficult industry to break into, those vendors can be great additions once trust is gained.
“The medical device manufacturers looking for packaging aren’t surfing the internet day in and day out looking for new vendors that have some new idea that might save them some money,” he says. “That’s not that industry. So, if you get in, you need to do a great job and don’t screw up. … Reputation is huge.”
Adding to the company’s medical industry credentials, Jamestown Plastics gained membership into the global MedTech Network. That network was established in 2021 in Schaffhausen, Switzerland, and features member companies in Switzerland, Australia and the U.S. It provides customers in the medical products industry with access to global supply through using local small and midsized enterprises.
Thanks to its depth of thermoforming experience with a wide range of plastics, Jamestown Plastics never backs away from challenging applications.
“The tougher the challenge, the more we like to take it on,” Baker says. “Our business is strong; our order book is strong, and we hope it continues that way.”
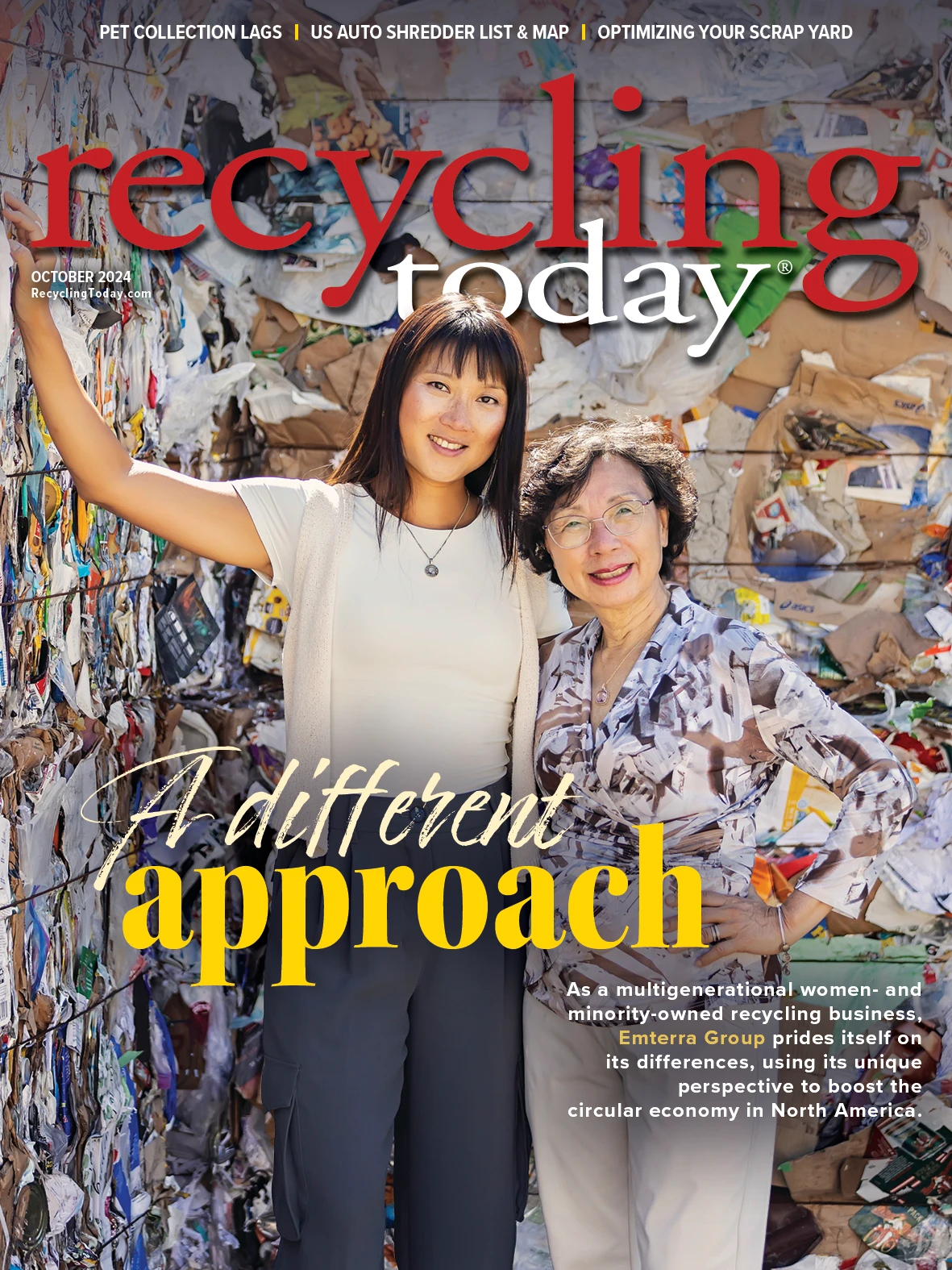
Explore the October 2024 Issue
Check out more from this issue and find your next story to read.
Latest from Recycling Today
- NWRA, SWANA issue joint response to Bureau of Labor Statistics fatality data
- Former WM executive joins Amp board
- PLASTICS announces formation of Polystyrene Recycling Alliance
- Energizer launches plastic-free battery packaging
- ReMA accepting applications for 2025 Design for Recycling Award
- Panasonic says collaboration yields recycling results
- Saarstahl inks recycled-content rail contract
- Liebherr machinery at work in expansion project