
Recently, U.S. Conveyor Technologies had the opportunity to work side-by-side with Steinert U.S. to deliver two Auto Shredder Residue (ASR) processing plants. With one in Georgia and the other in Texas, the plants were more than just geographically far away from one another.
One project was a retrofit to upgrade metals recovery. The other was a largely greenfield installation, although it required utilizing some existing infrastructure. Both projects entailed difficult integration elements.
Robert Broughton, Scrap Market Manager for Steinert, comments, “Anytime you work a retrofit project it’s more difficult. Each of these projects presented challenges. The team at U.S. Conveyor addressed the challenges to ensure the customers’ satisfaction. As a technology supplier, that’s the kind of partnership we need with a plant builder.”
Precision Integration
“Certainly, the bulk of the project in Texas was greenfield,” says Chris Melenick, Systems Project Manager with U.S. Conveyor. “However, we had to marry the front of the new system to the back of an existing metals sizing plant--no easy task. In Georgia we had to reconfigure the plant, adding equipment and changing material flow.”
In both instances, U.S. Conveyor brought a unique technological advantage to the project. “We were able to scan the existing plants using state-of-the-art digital scanning. Within our 3D engineering platform, we’re then able to marry that digital scan with new engineering work,” says Troy Graves, President of U.S. Conveyor.
“Through the scanning process we’re able to ensure seamless integration when it comes to joining new components to older ones,” says Melenick. “Another benefit is that once you scan the plant, you have all the data you need. There is no need to go on-site again to double-check dimensions. This makes everything easier for the customer, technology provider and plant builder.”
In Texas, the team found that the plant’s ground elevation varied. This, too, was discovered through the scanning process. “Allowing for elevation differences in the design was instrumental to ensuring a smooth installation. The laser scanning process removes guesswork, which eliminates the need for field modifications,” says Graves.
The Value Add

“In one of these plants much of Steinert’s newest technology was deployed. In the other we used some fine, if a bit older, technology and some of the newest technology,” says Broughton. “In both instances, maximizing the metallic recovery for the client was the objective. U.S. Conveyor helped us do that.”
“Analyzing plant performance, screen sizes, aspiration and material flow are all things we do on any project,” says Melenick. “We understand how material wants to flow; as plant integrators we’ve done this before. We consider the presentation of the material to each separation stage.”
”Customer requirements continue to evolve and change. In fact, in these two cases the customers were producing different products. One plant was more tuned to the export market while one was geared to feed other downstream operations,” says Broughton. Tuning to these differences is something U.S. Conveyor has done successfully.
Another technological advantage U.S. Conveyor brought to these projects was its unique Modular Hybrid Conveyor®. The modular design allows these conveyors to be added to or re-routed, and delivers flexibility should there be a future need to modify system flow or add new processing steps.
The conveyors also can be bent in an arc fashion. This allows the incorporation of vertical rise, but with a standard conveyor. The technology avoids special rollers and idlers as well as the expense and maintenance that goes along with them. The unique design eliminates material roll-back, which helps to maintain system production and even burden depth to ensure efficient separation with each processing stage.
“We enjoy working with U.S. Conveyor” states Broughton. “They do great work. On-site, their support and coordination is top-notch. They do a great job with drawings and overall plant layout, even considering things like containing spillage. We appreciate the added value they bring to any project.”
“Analyzing plant performance, screen sizes, aspiration and material flow are all things we do on any project.” — Chris Melenick
A Unique Partner
By working with U.S. Conveyor, Steinert got a strong partner for the project. The company was founded in 1988. Its staff is an experienced and growing team working together from two facilities with 70,000-square-feet of engineering and production capacity.
The team has more than 100 years of combined recycling industry experience and has worked on hundreds of projects, including the most complicated and advanced micro-fines plants.
U.S. Conveyor Technologies invests to provide its customers with a competitive advantage. That’s why it uses the latest in technology and design concepts to deliver cutting-edge material handling equipment. These include:
3D Laser Scanning –3D laser scanning gives U.S. Conveyor the ability to precisely scan a system and design new equipment to install seamlessly with the existing equipment. Less guesswork, less downtime, seamless installations.
Design Software –U.S. Conveyor designs in 2D and 3D CAD, at the customer’s preference, using the latest technologies in CAD software to make certain equipment is designed to install easily, operate safer and with maximized ergonomics.
Research and Development – U.S. Conveyor operates a dedicated research and development team that works with its customers to test and refine equipment designs. 3D printing also has become an important part of the prototyping phase to test fit and proper operation before production.
As a privately held, family-run company, U.S. Conveyor Technologies is not simply an equipment fabricator. It is a complete system design firm ready to help devise the right system to meet any customer’s individual needs.

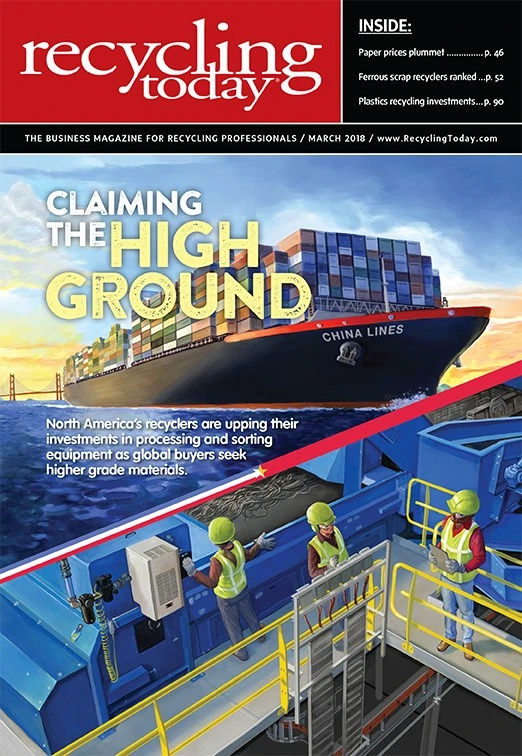
Explore the March 2018 Issue
Check out more from this issue and find your next story to read.
Latest from Recycling Today
- APR, RecyClass release partnership progress report
- Clearpoint Recycling, Enviroo sign PET supply contract
- Invista expanding ISCC Plus certification program
- Redwood partnership targets recycling of medium-format batteries
- Enfinite forms Hazardous & Specialty Waste Management Council
- Combined DRS, EPR legislation introduced in Rhode Island
- Eureka Recycling starts up newly upgraded MRF
- Reconomy Close the Gap campaign highlights need for circularity