
America’s electrical grid is an underappreciated asset, taken for granted by many people who simply assume that when they flip a switch, power will flow into a light bulb, appliance or entertainment device.
The workers and managers at A-Line Environmental Decommission Service (A-Line EDS) are more aware than most people that beyond that electrical switch plate is a coast-to-coast network of (mostly metal) equipment that must be vigilantly maintained and upgraded and sometimes replaced and decommissioned.
The decommissioning of this equipment can be a specialized process, particularly when it involves transformers and other devices that contain potentially hazardous materials.
A-Line EDS, based in Waterloo, Iowa, is one of those specialist firms. Its work causes it to take possession of a wide variety of electrical equipment, including wire and cable with considerable amounts of copper and aluminum contained within.
Doing things right
A-Line’s history of handling transformers, of which older ones can contain highly regulated polychlorinated biphenyls (PCBs), means the company is highly attentive to its decommissioning and recycling processes, according to Jon Lapczenski, director of business development at A-Line’s facility in Tonkawa, Oklahoma.
“A-Line provides the environmentally sound decommissioning of transformers and associated electrical equipment, as well as the most comprehensive transformer recycling and removal services available,” he comments.
His colleague Lynn Fritz, a senior account executive with A-Line, adds, “Our process is regulated by the United States Environmental Protection Agency (EPA). We have special permits, including one to operate a reclamation furnace, which means we can burn [insulating paper] off before we chop cable and wire.”
“It’s going to be a much cleaner operating system that will be better for the workers, and in the end we’re going to make a better product to sell to the market.” – Lynn Fritz, A-Line EDS
The company, on its website, says its facilities have been constructed and permitted “for the express purpose of providing environmentally safe disposal of transformers and associated electrical equipment regardless of PCB concentration” using methods that are “meeting or exceeding all local, state and federal regulations.”
Lapczenski and Fritz have been working with equipment maker Eldan, headquartered in Denmark, to upgrade a wire and cable processing system at the Tonkawa plant. The facility was acquired by A-Line earlier in 2016 and operates under the name A-Line Transformer Disposal Specialists, or A-Line TDS.
Although the 80,000-square-foot plant focuses in part on transformer decommissioning and dismantling, it also processes and prepares for market wire and cable that A-Line takes possession of as it undertakes projects on behalf of utility firms and property owners.
“A-Line EDS has been processing wire and cable since its inception,” Lapczenski says. “Wire and cable are essential electrical components that we handle on almost all of our on-site jobs and we process in all of our facilities every day. We granulate copper and aluminum, which we sell 100 percent to mills and end users within the United States,” he adds.
The company’s equipment must be prepared for a wide variety of materials, Fritz says. Inbound material, he says, “is a blend of both aluminum cable and copper wire.” In terms of gauge or width, the material is “all over the place,” he says, ranging from “angel-hair-pasta-thin wire to transformer core wires that are ?-inch thick.”
On the spot
A-Line has confidence in the technical capabilities of the Eldan equipment, but according to Lapczenski, a vendor’s knowledge, commitment to service and to answering follow-up questions were among the highest priorities.
He says a number of positives emerged quickly after A-Line contacted Eldan Recycling A/S, which has a sales and service location in Sanborn, New York, near Buffalo.
Lapczenski says, “There was already a somewhat dated Eldan system in place at the time of the acquisition [of the Oklahoma plant].” That system features a rasper that “breaks the material down to the size of a quarter,” he says. After that, material “goes into the granulator, which reduces it to chops about the size of BBs.”

Although A-Line had not previously worked with Eldan at any of its other locations, it decided to contact the firm. Shortly thereafter, Carsten Nielsen and Ken Moulin of Eldan “traveled to our facility in Oklahoma to discuss upgrading the system to help meet our needs,” Lapczenski says.
He continues, “After identifying the proper setup and necessary equipment [to install], we were assigned a project manager who we have been in continuous contact with ever since.” The Eldan project manager, Lapczenski says, “gives us updates as the equipment is being built and has been very easy to contact regarding maintenance and parts for our equipment.
“After meeting with Carsten and Ken and having them explain what they had to offer compared to other systems at our other facilities, we felt very comfortable with their expertise,” he continues.
Lapczenski says A-Line CEO Ben Stroh previously had shopped for a system that was installed in Iowa earlier this decade. “Ben was very educated on the chopping process” by the time it came to buy another system in Oklahoma, he says. “The Eldan people had to explain or justify the differences in their system and what they were trying to sell.”
Sponsored Content
Redefining Wire Processing Standards
In nonferrous wire and cable processing, SWEED balances proven performance with ongoing innovation. From standard systems to tailored solutions, we focus on efficient recovery and practical design. By continually refining our equipment and introducing new technology, we quietly shape the industry—one advancement at a time.
Expertise is only helpful when it’s available, he comments, and fortunately that has been the case with Eldan. “As questions have come up, they have always been available to us for answers,” Lapczenski says.
“We granulate copper and aluminum, which we sell 100 percent to mills and end users within the United States.” – Jon Lapczenski, A-Line EDS
After the installation is complete in October 2016, Lapczenski and Fritz anticipate several operational improvements will take place, including increased automation.
“We’re going to go from five people to two or three people needed, so we’re going to automate two of the positions,” Lapczenski says. “We’ll be able to prep material differently also, so overall we may be able to automate about four positions.”
Fritz adds, “It’s going to be a much cleaner operating system that will be better for the workers, and in the end we’re going to make a better product to sell to the market.”
In terms of its end markets, Lapczenski says, “All of our aluminum and copper chops are sold 100 percent domestically. So to achieve an optimum purity level we’re adding in a better air table and more complex magnets than we have now.”
He concludes, “Our finished product now is very good; but, with the new system, there should be a better end product made while using fewer people and while being able to achieve higher daily throughput than we are now.”
Get curated news on YOUR industry.
Enter your email to receive our newsletters.
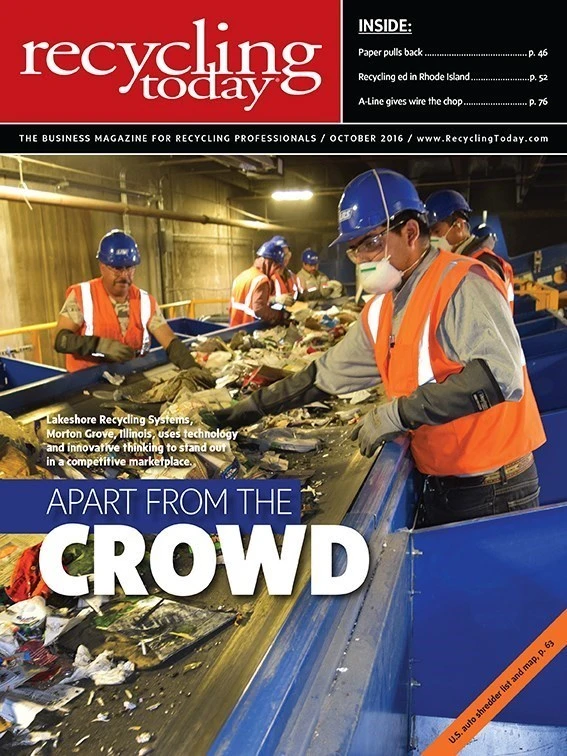
Explore the October 2016 Issue
Check out more from this issue and find your next story to read.
Latest from Recycling Today
- Hitachi forms new executive team for the Americas
- Southwire joins Vinyl Sustainability Council
- Panasonic, Sumitimo cooperate on battery materials recycling in Japan
- Open End Auto Tie Balers in stock, ready to ship
- Reconomy names new chief financial officer
- ICIS says rPET incentives remain weak
- New Jersey officials award $16.2M in annual recycling, waste reduction grants
- Linder Industrial Machinery announces leadership changes