
When the U.S. Department of Energy (DOE) announced funding for seven hydrogen hubs throughout the U.S. this past October, Cleveland-Cliffs Chairman, President and CEO Lourenco Goncalves was among those expressing support.
“Today’s announcement marks the very beginning of a new era in steel producing,” he said. “With clean hydrogen in our backyard, Cliffs’ hydrogen-ready blast furnaces and direct reduction plant will be the first in the world to replace CO2 with a new byproduct that does not contribute to global warming: This new byproduct will be H20.
“Furthermore, Cliffs’ willingness and ability to offtake a significant portion of the entire production of the hub eliminates the chicken-and-egg dilemma associated with clean hydrogen development and, in doing so, makes hydrogen viable for other industries, including the automotive sector.”

Cutting the carbon
Cleveland-Cliffs, the largest flat-rolled steel company in North America, defines vertical integration.
The Ohio-based company is involved in everything from iron ore and coal mining to iron pellet, coke and hot briquetted iron (HBI) production to ferrous scrap processing to downstream finishing, stamping, tooling and tubing. That level of integration lends advantages to a firm with ambitions to reduce its Scopes 1 and 2 greenhouse gas (GHG) emissions by 85 percent by 2030, using 2017 as the baseline. As of 2022, Cliffs had achieved a 32 percent reduction, Goncalves said Nov. 2, 2023, to a crowd assembled at the United Steelworkers Local 979 hall in Cleveland.
Cliffs gathered union and community representatives that evening to gauge their reactions to its plan to use hydrogen in its steelmaking process, with many in attendance voicing their support.
Hydrogen and green energy are part of a four-prong approach the company is using to reduce the carbon intensity of its steelmaking.

A multifaceted approach
In addition to hydrogen and green energy, the tactics Cliffs is employing to reduce its GHG emissions involve using direct-reduced HBI, which it produces in at its plant in Toledo, Ohio, in its blast furnaces; increasing the amount of prime ferrous scrap it uses; and injecting natural gas into its blast furnaces.
Goncalves said using HBI in its blast furnaces has yielded “enormous” benefits. “That material goes to the blast furnace prereduced, so the oxygen portion of that iron has already been removed,” he said. Therefore, no coke is needed, resulting in less carbon emissions. “It’s as simple as that.”
Maximizing its use of scrap allows Cliffs to use the same amount of iron to produce more steel. “The normal charge of scrap in a BOF [basic oxygen furnace] is between 10 [percent] and 18 percent,” he said. “In our plant, we use between 25 [percent] and 30 percent. So, we are using the same amount of pig iron, therefore the same amount of coke, therefore generating the same amount of CO2 to produce more steel.”
With Cliffs’ operations being based in the Midwest, the company also has access to natural gas. “We have access to a reductant and to a fuel that’s extremely efficient and green,” Goncalves said. “Keep in mind that natural gas is 96 percent CH4, so there is a little carbon, but there’s a lot of hydrogen in natural gas.”
Cliffs also has experimented with using hydrogen in one of its blast furnaces and is working with the Roosevelt Project out of the MIT Center for Energy and Environmental Policy Research to help facilitate this transition.
Tapping into hydrogen

Cliffs’ blast furnace in Middletown, Ohio—the smallest of its seven furnaces, including two in Burns Harbor, Indiana, two in Cleveland and one in Dearborn, Michigan—operated for half a day using hydrogen. “It cost me a fortune,” Goncalves said. “But I proved my point. We can reduce iron using hydrogen.”
Through the Bipartisan Infrastructure Law, the U.S. government is helping companies like Cliffs gain access to hydrogen through $7 billion the Department of Energy (DOE) has made available to help fund Regional Clean Hydrogen Hubs (H2Hubs).
The DOE says the H2Hubs will kickstart a national network of clean hydrogen producers, consumers and connective infrastructure while supporting the production, storage, delivery and end-use of clean hydrogen. The H2Hubs are expected to accelerate commercial-scale deployment of hydrogen that can help to decarbonize industries such as steelmaking and transportation.
According to the agency, the seven hubs were selected based on technical merit and impact, including the ability to produce at least 50 to 100 metric tons of clean hydrogen per day.
Up to $1 billion of the funding has been allocated to the hub being developed by the Midwest Alliance for Clean Hydrogen (MachH2).
“MachH2 is expected to generate numerous sources of clean hydrogen production across the U.S. Midwest, including in northwest Indiana near Cleveland-Cliffs’ two largest steel plants, Indiana Harbor and Burns Harbor. Cleveland-Cliffs currently is building a pipeline to bring hydrogen from the fence to Indiana Harbor Blast Furnace No. 7,” the company said when the DOE announced the funding in late October of last year.
Cliffs said its “large, stable hydrogen offtake ensures the hub’s viability and will mark a major step forward for the continuation of aggressive CO2 emissions reductions by Cleveland-Cliffs’ integrated steel mills. These integrated mills are uniquely capable of producing the most advanced steel products demanded by the automotive industry, for national defense applications and numerous other important industrial sectors.”
Other hubs to receive funding are the Appalachian Hydrogen Hub in West Virginia, Ohio and Pennsylvania; the Gulf Coast Hydrogen Hub in Texas; the Heartland Hydrogen Hub in North Dakota, South Dakota and Minnesota; the Mid-Atlantic Hydrogen Hub in Pennsylvania, Delaware and New Jersey; the Pacific Northwest Hydrogen Hub in Montana, Oregon and Washington; and the California Hydrogen Hub.
The MachH2 hub spans Illinois, Indiana and Michigan, with the potential to expand into other Midwestern states. Located in a key U.S. industrial and transportation corridor, the MachH2 will enable decarbonization through strategic hydrogen uses including in steel and glass production, power generation, refining, heavy-duty transportation and sustainable aviation fuel, the DOE says. The hub plans to produce hydrogen by leveraging diverse and abundant energy sources, including renewable energy, natural gas and nuclear energy.
When speaking in Cleveland, Goncalves said the DOE funding addresses the chicken-and-egg problem affecting hydrogen: “Nobody uses hydrogen because there’s no hydrogen, and there is no hydrogen because nobody uses [it].”
Goncalves said the MachH2 hub will produce 1,000 tons of hydrogen daily and that Cliffs’ offtake for Burns Harbor alone would be 200 tons, or 20 percent of that total. “That is going to make the hub viable from the get-go,” he said.
Cliffs plans to trial hydrogen at Burns Harbor, the largest blast furnace in the company’s footprint and the U.S.
It also is looking to capture the CO2 it does generate, and the geology in northwest Indiana should lend itself to that. “Hydrogen is coming first,” Goncalves said. “We need to reduce the CO2 emissions and then capture the rest with carbon capture.”
Additionally, Cliffs has an agreement with EDP Renewables in Houston to purchase 7 percent of its electricity companywide from a wind farm in Indiana and is exploring self-generated electricity. “Here at Cleveland works in the last reline of the blast furnace that we did a couple of months ago, we installed a new steam turbine generator to utilize additional blast furnace gas,” he said.

More than steelmaking
Goncalves noted Cliffs’ leading role as an automotive supplier, which he attributed to its integrated steelmaking assets and commitment to blast furnace/BOF steelmaking. “Supplying highly specified automotive-grade materials, particularly exposed parts, dictates the use of blast furnaces and BOFs,” he writes in Cliffs 2022 Sustainability Report. “We believe this will continue to be the case and, over time, we are confident we will be able to drive sustained reductions in carbon emissions from our integrated steelmaking footprint.”
Goncalves concludes the report with this message: “Cleveland-Cliffs has been, and continues to be, built for future generations. The decisions we are making today will resonate for decades, and we do not take that responsibility lightly.”
Get curated news on YOUR industry.
Enter your email to receive our newsletters.
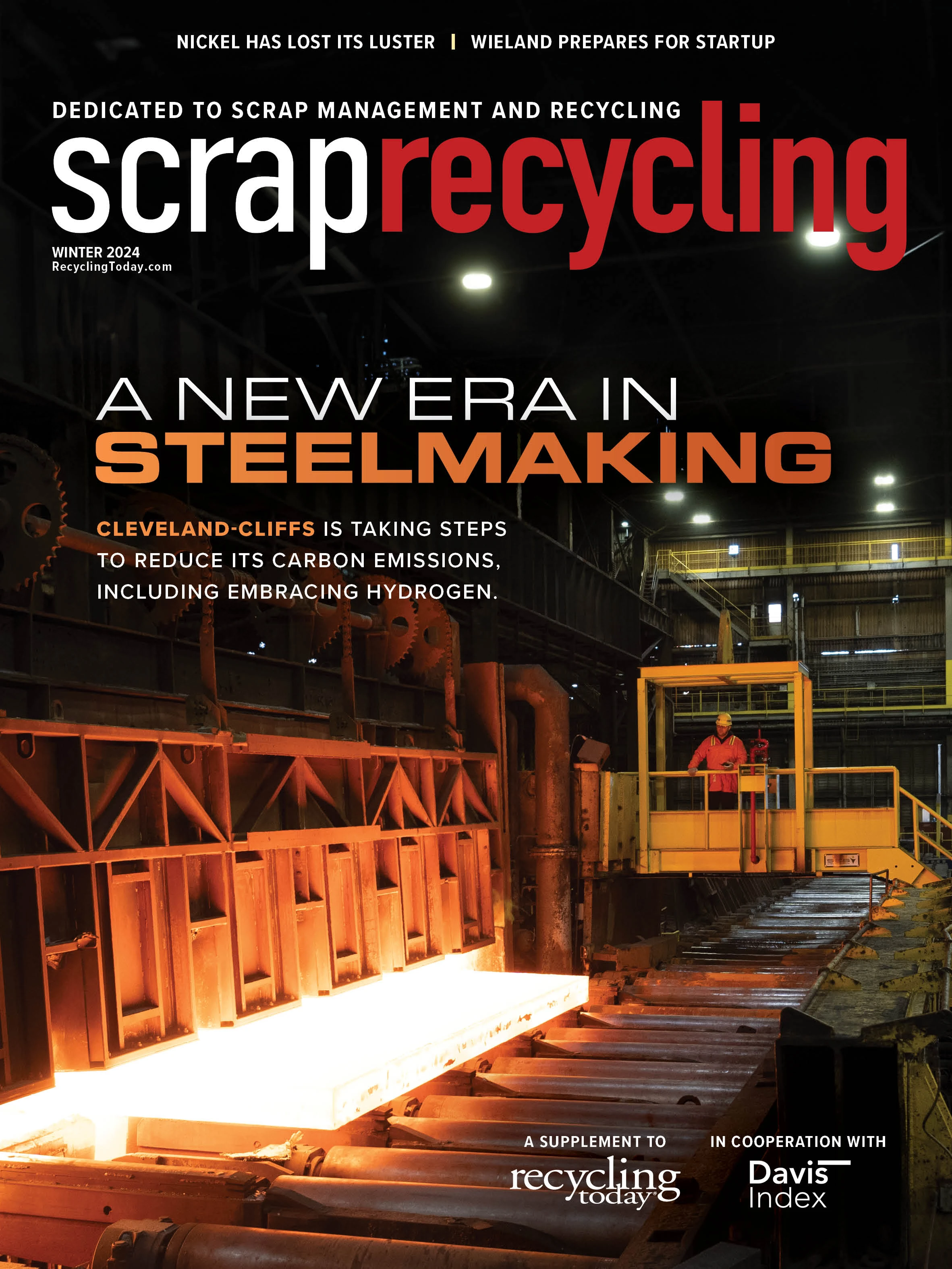
Explore the Winter 2024 Scrap Recycling Issue
Check out more from this issue and find your next story to read.
Latest from Recycling Today
- Eureka Recycling starts up newly upgraded MRF
- Reconomy Close the Gap campaign highlights need for circularity
- Nickel carbonate added to Aqua Metals’ portfolio
- EuRIC, FEAD say End-Of-Life Vehicle Regulation presents opportunity for recyclers
- Recyclers likely to feel effects of US-China trade war
- BCMRC 2025 session preview: Navigating battery recycling legislation and regulations
- Yanmar Compact Equipment North America appoints new president
- LYB publishes 2024 sustainability report