Processors are paying closer attention to the efficiency of their heavy-duty shredders in an attempt to squeeze out more profits.
It is getting tougher and tougher to make a living these days, so the old saw goes, and the auto shredding business is no exception. For many years there was only a smattering of heavy-duty shredders across the United States, and even seven years ago there were only about 180. Today, there are 211 shredders in the U.S., and more keep coming on line.
Auto hulks have been the primary food for shredders, and they still are with about 10 million being processed annually, according to the Automotive Recyclers Association, Fairfax, Va. However, cars are not "juicy" hulks of iron and steel anymore. Today’s automobiles are built with thinner-gauge, higher-strength steels and more plastics, thus they are lighter in weight. So, to keep going, processors are shredding other large scrap items such as appliances.
Reports from the field indicate that shredding profit margins are okay, but thinning, as processors compete for material to shred. The situation has forced many to take a hard look at how they operate and scrutinize how their behemoth shredders are being powered. Although AC motors are still the predominate and proven drive for heavy-duty shredders, alternative drives such as DC motors, diesel engines and diesel conversions show promise for increasing profits.
AC VERSUS DC
In order to shred auto hulks and large pieces of metal, heavy-duty shredders need plenty of power to grind the scrap into fragments or "frag" as it is referred to in the industry. Shredders can require 3,000 to 6,000 horsepower to operate, and processors are finding that choosing the right drive for their shredder is a good place to start when considering cutting costs and operating more efficiently.
An AC motor is one that uses "alternating current," meaning that the current reverses direction at regular intervals. Typically, lights, heaters and most household appliances use AC power because it does not effect their operation. Because the alternating current produces a constant magnitude, or fixed frequency, AC motors are able to maintain a constant (or nearly constant) speed even with changing loads – that’s why they are popular in many industrial applications.
"The motor’s speed is directly proportional to the frequency, and in the U.S. that AC frequency is fixed at 60 cycles," says Jim Kelly, manager of operations at General Electric Apparatus Services, Cleveland, Ohio. "The best way to change the speed is with a ‘variable frequency drive’ (electronic converter) that can be retrofitted to the motor. Another method involves dampening the voltage to slow the motor during light loads, but that method is an inefficient use of power."
Conversions, however, may not be appropriate for heavy-duty shredding. "Electronic converters can be placed on AC motors to adjust the speed, but the components are not able to withstand the shock loads," says Pete Albert, president and owner of Dutch Electric, Reading, Pa. "Although I feel that these converters may be ready in the near-term future, I would not use one today, and we are not recommending them for shredders."
Without a converter, an AC-drive system normally only includes the motor itself and a starter with an on/off button.
On the other hand, a DC motor is one that uses "direct current," meaning that the current flows in only one direction. Batteries also generate DC current and most electronic devices require DC power to operate. Since the power supplied via incoming lines is AC, DC motors or DC-operated electronic devices require a rectifier (also called a converter/controller) to "rectify" the incoming current so that it flows in one direction. On a car’s engine, for example, the alternator (which converts mechanical energy into electric energy) generates AC current, but the battery and all the onboard electronics require DC. Therefore, a rectifier is needed.
The rectifier also serves to control the level of voltage so that the DC motor can vary its speed. Thus, the popularity of DC motors lies in their ability to adjust speeds to varying loads. However, for the large DC motors that are required for heavy-duty shredding, the rectifier and extra circuitry is an added expense that has to be considered, according to Albert.
"For DC drive you need the motor, a rectifier (or converter/controller), and a transformer," says Albert. "With an AC system, only the motor and a starter are needed. The type of rectifier needed for a large DC motor for shredding is specifically called a silicon controlled rectifier."
This type of rectifier uses thyristors instead of diodes. A diode can only change the current, whereas a thyristor can convert the current and also control the voltage. This is important because the voltage control provides better control of the motor.
"There are currently six- and 12-pulse SCRs on the market, and we recommend installing 12-pulse ones," continues Albert. "A higher pulse rating uses more thyristors to smooth out the DC waveform, and with a smoother DC waveform there is less harmonic distortion travelling back to the power company – sort of like one-foot waves hitting the beach instead of 10-foot ones. Before, this distortion was ignored, but now utility companies are cracking down on large users. So, it pays to go with the higher pulse rating."
According to Ohio Edison, Akron, Ohio, increased harmonic distortion can damage transformers and other equipment. "If we find a situation with a lot of harmonic distortion we try to work with the company causing the problem," says Randy Frame, industrial supervisor at Ohio Edison. "If the problem cannot be resolved, then we would have to shut the operation down because we cannot risk damaging our equipment."
So what’s the better drive for shredders – AC or DC? AC motors have the weight of tradition behind them; however, DC motors offer more operational flexibility and electrical cost savings.
"AC motors are most efficient when operating at full load," says Kelly, "and as the load decreases, the AC motor becomes less and less efficient. DC motors, on the other hand, are more efficient with changing loads because their rpm can be changed. However, with the added circuitry of a DC motor, there is more maintenance than with an AC one."
MOTIVES FOR CHANGE
If DC drives are so much better in terms of operation and efficiency, why aren’t they more widely used?
"The reason DC drive was not used before in large shredding applications was that the DC motor could not handle the mechanical shock of shredding," says Albert. "Today, because of the shredder design and advancements in drive technology, there is not as much shock put back into the drive."
Another reason why DC motors are now becoming popular is because of the different types of materials going into shredders. Before, it was mainly just autos. Today, it includes appliances and other large items. So the shredder is constantly shredding varied loads and does not need to operate at the same speed or working load to operate effectively. And a DC motor adjusts to those loads, saving power and machine wear.
In addition, processors are facing pressure from local power companies to better control and even reduce their power consumption, according to Paul Rembach, president of OMC Controls, Houston.
"In many cities, since there’s already so much heavy industry, power companies don’t want you to bring a massive AC motor on line with them, because there’s no control to limit the current spike you get when there’s a shredder type load," he explains. "For a DC motor, since the conversion of AC to DC is electronically controlled, you can ramp up the DC current very smoothly, plus you can limit its absolute peak electronically. Power companies like that because it doesn’t shock load their lines."
According to Rembach, DC drives weren’t used more in the past because shredder operators didn’t need to vary the speed of their loads – the drains on power companies weren’t as great and the processors were shredding more uniform material. There was also an issue of marketing, he adds, as AC drives were marketed towards shredder applications and DC drives were marketed towards other applications such as oil extraction and submarines.
Today, processors also want to save money, says Rembach. "There are very few areas where you can actually cut your costs in a shredder operation. Your labor is pretty much fixed, insurance is a constant, what you buy and sell for is always fluctuating. But if you can reduce the power that you use, then that’s a direct cost reduction. And you can do that with a DC drive."
Not only does the DC motor save money by drawing less power, its various speeds also help to unjam a shredder – sort of like pushing the various speed buttons on a kitchen blender. The DC motor can also be operated in reverse.
Another benefit of DC drive is that it can be stopped faster than an AC motor. "With regenerative braking, a DC drive motor can be stopped in 30 seconds, eliminating excessive shut down time," says Harrison Franke, sales manager for OMC. Large AC motors operating at high rpms, on the other hand, can take about 30 to 45 minutes to wind down.
DOING DC
To date, there are still only a handful of processors that have made the switch to DC drive, but the conversion is gaining popularity. Marc Olgin, Liberty Iron, Erie, Pa., has two auto shredders that shred about 150,000 hulks annually. Both shredders have DC motors and he says that the installation is not complex and that the motors are running smoothly without any problems.
"We just had our shredder with its DC drive installed recently, and it is doing great," says David Wilson, president of Johnson City Iron & Scrap.
"Before I bought it, I talked to several engineers that are friends of mine and other processors with DC drive, and everyone recommended it. I like the DC configuration because it does not stall even at every low rpm. An AC motor will stall. One shredder nearby with an AC motor can’t accept baled appliances because they keep stalling his shredder. We, however, can shred them without any problem. Our shredder will go from 600 rpm to as low as 100 rpm without stalling and still maintain proper torque. In fact, I watched a car being shredded the other day and it had five engines in it – its original engine, plus two in the front seat, and two in the back. The DC motor went from 575 to 300 rpm and it took only about 10 seconds to recover."
Still, AC-motor power is the predominate drive for large shredders, and each situation will dictate the best setup depending on many factors.
Second in a two-part series for 1995 on auto dismantling and recycling.
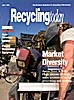
Explore the July 1995 Issue
Check out more from this issue and find your next story to read.
Latest from Recycling Today
- USTR announces phased measures designed to address China’s shipbuilding dominance
- APR, RecyClass release partnership progress report
- Clearpoint Recycling, Enviroo sign PET supply contract
- Invista expanding ISCC Plus certification program
- Redwood partnership targets recycling of medium-format batteries
- Enfinite forms Hazardous & Specialty Waste Management Council
- Combined DRS, EPR legislation introduced in Rhode Island
- Eureka Recycling starts up newly upgraded MRF