
Demand for nickel has grown at a fast pace over the last decade. According to the International Nickel Study Group (INSG), Lisbon, Portugal, global demand for nickel in 2000 stood at 1.1 million metric tons and grew 21 percent to 1.4 million metric tons in 2010. By 2020, however, demand for this metal grew by 41 percent to reach 2.3 million metric tons.
Nickel production has been unable to keep up with this growth in demand, with the World Bureau of Metal Statistics (WBMS) in the United Kingdom reporting a 41,100 metric ton deficit in the nickel market in the first half of this year.
Refined nickel demand in the first six months of this year exceeded output by nearly 100,000 metric tons, with demand expected to increase further by 255,000 metric tons in 2021 compared with the previous year, according to data from the WBMS.
Much of this demand is being led by the rise in nickel consumption by the electric vehicle (EV) batteries industry.
EV batteries and nickel
Nickel is a key raw material in most lithium-ion batteries used in EVs because its properties help deliver higher energy density and higher storage capacity at a lower cost. The most used batteries are nickel cobalt aluminum, or NCA, which consists of 80 percent nickel, and nickel manganese cobalt, or NMC, which contains 33 percent.
Production of nickel-based EV batteries also is set to leap with growing demand for and production of EVs across the world. The Electric Drive Transportation Association, Washington, has projected new EV sales to grow by 10 percent to 8.5 million units by 2025, by another 28 percent to reach 26 million vehicles by 2030 and by 58 percent to 54 million vehicles by 2040.
According to a publication by the Nickel Institute, Toronto, demand for energy-dense nickel-containing batteries will continue to grow for applications in EVs and renewable energy storage. The institute states that 39 percent of lithium-ion batteries contain nickel, with this number expected to increase to 58 percent by 2025.
Long before EVs became a popular nickel consumer, stainless steel was a key consumer of this metal.

Stainless steel growth
Although chromium is the main alloying element in stainless steel, nickel enhances this metal’s formability, weldability and ductility. The Nickel Institute estimates that nickel-containing stainless steel grades account for 75 percent of the total stainless steel production today.
According to a report released in May by the International Stainless Steel Forum (ISSF), Brussels, stainless steel production in 2020 fell by only 2.5 percent from the prior year, despite the disruptions caused by the COVID-19 pandemic. In the first quarter of this year, global stainless steel production increased by 24.7 percent on an annual basis.
Tim Collins, the secretary general of ISSF, writes that demand for stainless steel has been growing by 5 percent on an annual basis since 1980. This, in turn, means that demand for nickel also has been increasing since then.
The question then arises, will the rise of EV batteries affect the supply of nickel available for stainless steel?
Not really, Collins says, pointing to the development of nickel-free stainless steel and low-nickel duplex stainless steel, which are likely to balance the overall demand for nickel in this sector. He says with the growing requirement for these grades, nickel use also could be curtailed in stainless steel.
New forms of stainless steel

Nickel use in stainless steel has been curbed with the introduction of low-nickel or nickel-free grades, stainless steel scrap and nickel pig iron (NPI).
According to the INSG, the annual production of NPI, which was first made by China in 2005 in many forms and grades, has increased. In 2010, NPI production stood at 160,000 metric tons and grew to 505,000 metric tons over the next decade.
Indonesia also started producing NPI in 2014, and its production reached 605,000 metric tons in 2020. INSG notes that all this NPI is being used in the production of primary stainless steel in the place of traditional raw materials, such as nickel metal and stainless steel scrap.
Still, Collins writes, we do not capture all the stainless steel scrap that becomes available at the end of life. Around 20 percent of it is lost to a combination of landfills and general steel industry usage, which could potentially be added back to producing primary stainless steel and could reduce demand for nickel.
All these factors have resulted in stainless steel becoming a self-sustainable metal where the requirement for nickel is not growing in proportion to the rising demand for stainless steel.
Collins cautions that while the growth of EV batteries remains an unknown and is not likely to affect the availability of nickel for use in stainless steel, a dramatic rise in battery electric vehicles and fuel cell electric vehicles could change the situation to some extent.
That said, battery technology also is evolving, and the requirement for nickel in batteries also could change in the medium to long term.
Countries that could fill the gap
The INSG reports that in 2007, nickel output was close to 1.4 million metric tons and slumped to 1.3 million metric tons in the 2008-2009 time frame during the global economic crisis. The market recovered again in 2010 to 1.4 million metric tons and kept increasing further until 2013 to 2 million metric tons. In 2020, global nickel production hit almost 2.5 million metric tons, according to INSG.
The explosion in nickel demand also is benefiting a few countries as illustrated in the tables on the opposite page.
Many stainless steel- and EV-producing nations have increased their imports of nickel to match growing demand for the metal, and the current nickel supply appears to be sufficient to fulfill the growing demand for both stainless steel and EVs as of now.
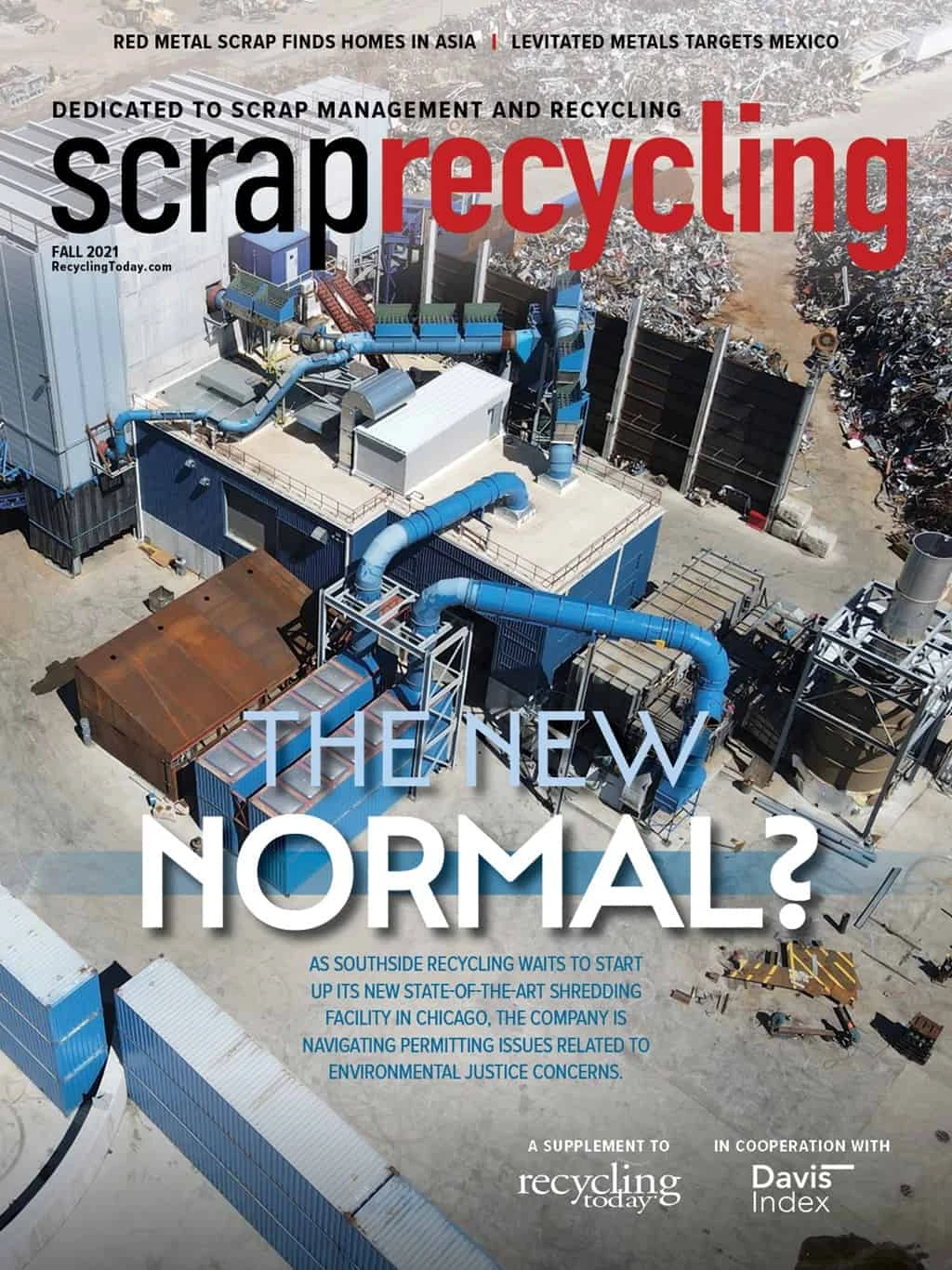
Explore the Fall 2021 Scrap Recycling Issue
Check out more from this issue and find your next story to read.
Latest from Recycling Today
- LumiCup offers single-use plastic alternative
- European project yields recycled-content ABS
- ICM to host colocated events in Shanghai
- Astera runs into NIMBY concerns in Colorado
- ReMA opposes European efforts seeking export restrictions for recyclables
- Fresh Perspective: Raj Bagaria
- Saica announces plans for second US site
- Update: Novelis produces first aluminum coil made fully from recycled end-of-life automotive scrap