
Atlanta-based Pirkle Inc. has added an auto shredder to its processing capabilities, and the new equipment comes from one of the sector’s newest suppliers.
Grand Prairie, Texas-based 3Tek Global supplied a NEXT 7400 shredder and a NEXT 2100 Power Module to Pirkle. Bill Padula, 3Tek vice president of sales and marketing, says 3Tek also supplied a drum magnet and an infeed conveyor.
Readers with equipment buying or shopping experience may recognize Grand Prairie as the home of Granutech Saturn Systems, a long-time supplier of processing equipment to the recycling industry. Granutech Saturn is one of the three companies that have put the “3” in the 3Tek Global name.
Combined powers
3Tek Global bills itself as a worldwide provider of “world-class, affordable, hammer mill processing and sorting solutions.” While it may be a new kid on the block, it has what it calls “deep, proven scrap roots” in the form of its founding companies, Granutech Saturn Systems; San Antonio-based Riverside Engineering; and Charleston, South Carolina-based Peninsula Equipment.
Padula says he and other key employees at 3Tek gained experience and cultivated relationships from having worked for one of these three companies or other long-time suppliers to the scrap industry.
He says he had sold equipment previously to Pirkle, and the decision-maker there “trusted the newly created company as a result.” Padula adds, “People buy from people.”
The three founding companies each bring technology,
In terms of each company’s specific contributions, 3Tek’s website states, “Riverside Engineering brings its hammer mill design knowledge; Granutech Saturn Systems, its technical depth and manufacturing technologies; and Peninsula Equipment brings its depth of Caterpillar diesel engine and track capabilities.”
Riverside Engineering makes and markets its own line of shredders, with models featuring rotors ranging from 60 to 120 inches in width. The company has four MegaShredder models and two Super Heavy Duty models it says are designed as “tough, strong machines,” some of which it bills as the highest-capacity machines available.
3Tek has intentionally focused on the smaller end of the capacity spectrum, with its shredder rotors ranging in size from 48 to 74 inches. While the Next 7400 installed for Pirkle in Atlanta can handle auto bodies, Padula says it will be fed “largely white goods and mixed metals.”
Another selling point, according to 3Tek, is that its products are made in the United States, at facilities in Texas and South Carolina. (Replacement and wear parts also are being stored in those two states.) At the same time, the extensive international experience of the founding companies means 3Tek “can provide excellent product support to small scrap yards worldwide,” the firm says.
Although 3Tek will have no qualms about working with larger companies, the shredder supplier is specifically targeting the small-to-midsized company niche.
Specific purpose
On its website, 3Tek states, “We see the future of scrap processing and believe the processing power is shifting to the small yards. Our sole focus is to arm small scrap yards with world-class, affordable hammer mill processing and sorting solutions.”
Padula says the company’s approach involves less customization compared with some of its competitors, but the trade-off is greater affordability. “3Tek wants to provide affordable shredding systems to the small yards. To make it affordable with quick delivery time, we cannot make customized one-off type systems,” he comments. “We build a standard product and will do some customization of the infeed and downstream systems to match a customer’s needs.”
The company’s website makes the same points: “If you produce less than 100,000 tons per year and want to take control of your destiny by processing your own scrap, you have come to the right place.”
3Tek says its Next
Regarding downstream sorting capabilities, 3Tek says it offers “simple to complex downstream separation machinery sized to match [its] line of hammer mills.”
Padula says in the case of Pirkle, the company had a preexisting downstream system that focuses on producing clean ferrous scrap and a
The Next 7400 shredder Pirkle purchased has a mill that is 74 inches in diameter (100 inches wide), powered by a 2,100-horsepower Caterpillar 3516 model diesel engine.
3Tek says the Next 7400 has “all the design features of a Riverside Engineering Mega Shredder but scaled to fit [a smaller] sized yard.” The shredder weighs in at 330,000 pounds (165 tons), according to 3Tek, and includes 2-inch-thick
The entire unit can be mounted on the same tracked undercarriage used for Caterpillar 345 model excavators.
Pirkle fits within the scope of companies that 3Tek is targeting for installations. On its website, the scrap processing company describes itself as having started “as a simple, service-oriented scrap business [that] has grown into a sophisticated, efficient institution.”
The company’s facility—situated not far from the junction of Interstates 95 and 20—is located just southwest of Atlanta’s downtown.
Pirkle purchases industrial and commercial scrap and conducts retail business, which can provide an additional stream of obsolete scrap to feed its new shredder.
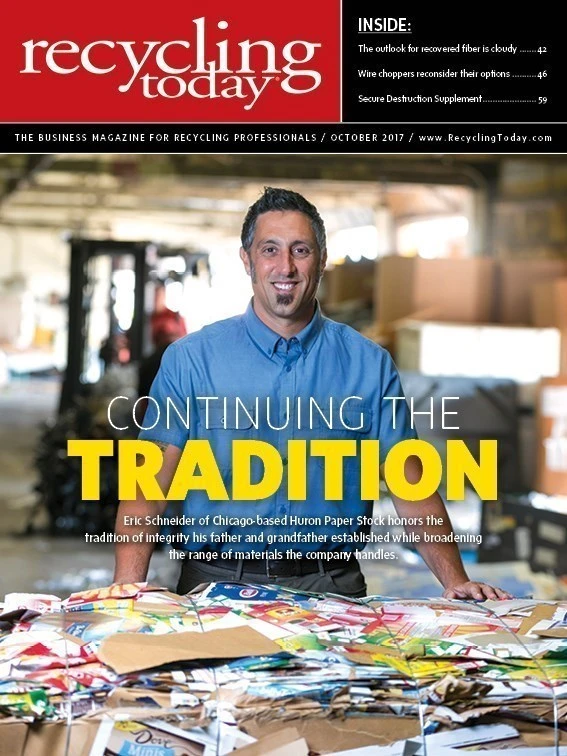
Explore the October 2017 Issue
Check out more from this issue and find your next story to read.
Latest from Recycling Today
- Aqua Metals secures $1.5M loan, reports operational strides
- AF&PA urges veto of NY bill
- Aluminum Association includes recycling among 2025 policy priorities
- AISI applauds waterways spending bill
- Lux Research questions hydrogen’s transportation role
- Sonoco selling thermoformed, flexible packaging business to Toppan for $1.8B
- ReMA offers Superfund informational reports
- Hyster-Yale commits to US production