Bigger is better seems to have become the operating philosophy for recyclers in all segments of the industry in the past decade, as having one large processing facility is now considered more efficient than having several recycling outposts.
The combination solid waste-recycling companies have been busy retrofitting their processing plants, often putting in automated sorting systems and high-production balers. Similarly, scrap metal companies may keep some feeder yards open to attract obsolete scrap, but they are often doing their processing and baling in one central plant.
Although bale dimensions themselves are not getting any larger, most recyclers have been eager to churn out more bales in one shift at one plant than they were just a few years ago.
ALL IN ONE. The trend toward massive material recovery facilities (MRFs) in the municipal segment and larger "super yards" in the scrap sector has created several challenges for plant managers and equipment providers.
According to equipment suppliers, installing high-volume balers is just part of the solution. Plant operators also want to be able to measure results, have reliable equipment and increasingly possess machinery that can handle a variety of materials efficiently.
In addition to large MRFs and scrap facilities dealing with more volume, they usually also handle a wide variety of materials. In the case of MRFs, this material may enter the plant in a commingled form, providing an entire additional set of challenges and equipment needs before material ever reaches the baler (or balers).
After material has been through all the automated sorting equipment and past the sorting line stations, what emerges at a MRF are several grades of paper and several types of separated rigid containers that need to be baled.
MRF operators can take different ways of handling this cross-section of grades, according to equipment suppliers.
Ken Ely of recycling equipment distributor Ely Enterprises Inc., with locations in Cleveland and Chicago, says some of his customers are handling enough material to have designated balers for certain materials. "One of my larger customers has five balers at their plant," Ely comments. "One is for news grades (ONP), another for OCC (old corrugated containers), another is for rigid containers. We’re seeing more balers designated for one material."
A plant manager may choose this option because one baler simply won’t handle everything; because certain styles of balers are more suitable for certain materials; or even because some recyclers are reluctant to have just one baler on hand in case a worst-case scenario of unplanned downtime throws production hopelessly behind.
"There are still some people who think it’s risky to have a single machine, because if the plant doesn’t have room to store more than one day’s worth of incoming material, then if you have prolonged downtime it creates serious problems," says Joe Szany of Marathon Equipment Co., Vernon, Ala.
Szany also says that MRFs that bale considerable paper and container volumes may choose different style balers for these two portions of their output.
"Many non-fibrous items, such as plastic containers, steel cans, aluminum used beverage containers (UBCs), don’t bale very well in anything but a two-ram baler," says Szany. "Companies that don’t make two-ram balers might profess otherwise," he adds, "but you have to allow the density of the bale to relax before you tie it."
On the fiber side, however, those putting out high volume have gravitated toward single-ram extrusion balers. "People feel they can get more fiber tonnage out of a single-ram extrusion baler, and I would agree with that," says Szany. "If you want to do 6,000 to 9,000 tons per month, you may need an open-end [extrusion] baler."
Conveying Some Thoughts |
When handling multiple materials, some recyclers are shifting to a dual conveyor system, says Joe Szany of Marathon Equipment Co., Vernon, Ala. "When switching grades, it’s not so much the baler that slows down, but the baling process. Operations feeding a baler with multiple conveyors can store one grade on a conveyor while feeding the other grade into the baler. Thus, with two conveyors, you may not have to stop making bales while cleaning out your conveyor." Ken Ely of Ely Enterprises Inc., Cleveland, notes, though, that not all plants can install this system because of space constraints. "It’s a great idea if you have the room, but the space is often too tight to allow that," he remarks. Whether using a second unit or planning for a longer single conveyor, recyclers should certainly plan for growth, agrees Jeffrey Van Galder of conveyor manufacturer Karl W. Schmidt & Assoc., Commerce City, Colo. "I have never heard a plant manager say, ‘I wish I had less conveyor,’" he quips. Additional considerations to be given to conveyors can include changing the incline angles and the belt speeds, using wear-resistant parts and purchasing conveyors "designed to abate excessive housekeeping and ensure ease of inspection and maintenance," according to Van Galder. "If a conveyor isn’t engineered properly or built to handle the load or the wear, it can prove to be a significant Achilles heel in the whole process," Van Galder remarks. "A recycler can’t buy a premium baling machine and then go to the lowest bidder on the conveyor," he continues. "It’s like setting your table with your best china and then having guests eat with plastic forks and spoons. The delivery mechanism has to be considered as a critical component to the system." |
European equipment makers such as Macpresse, sold in the U.S. through Sierra International Machinery Inc., Bakersfield, Calif., and Bollegraaf, sold in the U.S. through Van Dyk Baler Co., Stamford, Conn., have had success selling to large MRFs and paperstock plants with models that offer superior throughput.
With these machines retaining the heavyweight title, makers of smaller machines can still serve the large MRF market as secondary units baling containers and handling streams where grades entering the chamber may change frequently.
Equipment makers are offering modifications to address just this situation, according to Ely. "Anytime you switch grades, you’re losing production. But some newer balers are coming out with bale separation features such as a bale separation door," he notes.
Control panels now allow operators to change baler settings with the touch of a button when shifting from one material to another. Touchscreens that come with balers made by IPS Balers Inc., Baxley, Ga., "have a minimum of 15 materials programmed in; operators just hit a button," says IPS president Sidney Wildes.
IN AND OUT. Dealing with mixed materials is one challenge for recyclers, but a bottom line consideration for many is baling as much material as possible in one hour, one shift or one month. Additionally, with more material heading overseas, how to most quickly fill an export container is also a consideration.
"People are looking for balers that can provide them with bale weights heavy enough to max out an overseas container so they can export this product," says Wildes. "They are also looking for the highest throughput they can get through a machine."
IPS has introduced increasingly high-volume machines to compete with the European equipment makers who have dominated this market. Wildes says the new Conquest model from IPS is the highest volume machine yet made by his company. "It is an extrusion baler, a single-cylinder model with a double-hinge side and it can be equipped with an opening as large as 72 inches by 72 inches."
Van Dyk Baler Corp. has been offering its models to the North American market since Pieter Eenkema van Dijk emigrated to the U.S. from the Netherlands in 1984. The company’s high-volume extrusion models have been received warmly and can be found at MRFs and paperstock plants throughout the U.S. and Canada.
Similarly, Sierra International Machinery sells the Italian-made Macpresse line through offices in Keller, Texas. The company has seen an interest in its high-volume extrusion models, with buyers like Metro Waste Paper Recovery Inc. in Toronto installing its first Macpresse model nearly two decades ago.
The Sierra Macpresse 111AS.1 model is advertised as being able to bale up to 30 tons per hour of OCC and up to 60 tons per hour of ONP. With the trend toward larger plants, baler makers will most likely continue to introduce new models designed to make heavier bales in a hurry.
In addition to making dense bales quickly, balers need to be fed efficiently, and cycle time remains important.
On the conveyor side, Szany says, "Most recycling companies are going to buy a conveyor that can handle more than the baler can process, and that’s a wise decision. You can adjust the conveyor to the baler’s production; it’s tough to do it the other way around."
Sponsored Content
Labor that Works
With 25 years of experience, Leadpoint delivers cost-effective workforce solutions tailored to your needs. We handle the recruiting, hiring, training, and onboarding to deliver stable, productive, and safety-focused teams. Our commitment to safety and quality ensures peace of mind with a reliable workforce that helps you achieve your goals.
Cycle time can be largely dependent on conveyor efficiency. "Every baler will displace so many cubic feet per hour; it’s a mathematical given," says Ely. "The question is: How full can you keep that machine to maximize it? The key is keeping the conveyor belts fed so that the balers are busy all the time and there is no downtime—as opposed to a baler sitting idle for 30 seconds or 10 minutes before cycling again."(See the sidebar on page 52 for more on conveyors.)
CUTTING COSTS. The move toward larger recycling plants is generally made for cost reasons—producing more material at a lower cost per ton.
While consolidating operations is one way to do that, recyclers are also looking at each baling cost, including labor and wire. "I think more buyers today are thinking about the cost of baling as opposed to the cost of the baler," notes Szany.
Says Wildes, "I think buyers are more cognizant of their business expenses. They are interested in throughputs and cost per ton and they are interested in long-term equipment. They will pay a little more for a baler that will last."
For these reasons, balers that are largely self-operating—or more accurately that can be operated intermittently by an employee performing other tasks—have gained popularity.
"Ten years ago, most facilities had two-ram machines that had to have an operator," says Ely. "Now a worker can keep an eye on that machine while also feeding the baler with a loader carrying away finished bales with a forklift."
In studying costs, Szany says, "One of the biggest surprises of my life was finding that a large volume recycler is going to spend more on wire over the life of the baler than was spent on the cost of the baler. You don’t notice it as much because you’re spending a little bit at a time."
Szany says buyers should consider the differences of balers that may use $1.60 worth of wire per ton versus a model that uses only $1.00 per ton.
The equipment vendors agree that the examination of such issues has increased over the past decade as plant managers in a relatively new industry—the collection and processing of curbside recyclables—have gained experience.
"Today’s MRF operators understand equipment," says Ely. "These operators have come through a tremendous learning curve over the past 10 or 15 years, and have gained a lot of knowledge."
The author is editor of Recycling Today and can be contacted via e-mail at btaylor@RecyclingToday.com.
Get curated news on YOUR industry.
Enter your email to receive our newsletters.
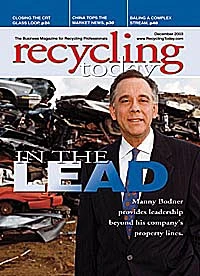
Explore the December 2003 Issue
Check out more from this issue and find your next story to read.
Latest from Recycling Today
- Steel Dynamics cites favorable conditions in Q1
- Hydro starts up construction in Spain
- Green Cubes unveils forklift battery line
- Rebar association points to trade turmoil
- LumiCup offers single-use plastic alternative
- European project yields recycled-content ABS
- ICM to host colocated events in Shanghai
- Astera runs into NIMBY concerns in Colorado