
The passion and enthusiasm are contagious at PureCycle Technologies LLC’s Ironton, Ohio, site, where the company is working to ramp up production of its ultra-pure recycled resin (UPR), made using an advanced recycling process that uses a solvent-based technology to remove colors and odors from postindustrial and postconsumer polypropylene (PP).
It hasn’t been an easy road to get to this point, and PureCycle continued to encounter challenges as of mid-September, but the company’s belief in its mission to transform the PP recycling industry has not wavered.
Impassioned people
“I’ve been involved with a lot of new plants, a lot of new technologies, a lot of new projects; I don’t think I’ve ever seen one where the team was more aligned and more excited about working together and accomplishing the goal,” PureCycle Board Chair Dan Coombs says.
Before retiring from LyondellBasell in 2020, Coombs spent five years in various executive vice president positions with the petrochemical company. Prior to joining LyondellBasell, he spent nearly 15 years at Chevron Phillips Chemical Co. and 15 years with Phillips Petroleum.
“I wouldn’t have come out of retirement for anyone else,” he says of PureCycle and CEO Dustin Olson.
Olson has led the company since mid-2022. He replaced former CEO Mike Otworth, who had been in that role since 2017 when the company was formed. Otworth resigned to return to Innventure, PureCycle’s former parent company before it went public in early 2021.

in Ironton, Ohio, up and running. The site includes a PreP area that resembles
traditional mechanical recycling processes, and a purification area where its
patented technology is used to remove color and odors from recycled postindustrial
and postconsumer polypropylene.

Olson served as PureCycle’s chief operating officer and chief manufacturing officer before being named CEO, having led manufacturing and operations since 2021. Now, he leads all global operations for the company, including manufacturing, procurement, sustainability, commercial sales and joint venture partnerships.
Prior to joining PureCycle, Olson spent more than 20 years working in refining, olefins, specialty chemicals and specialty polymers throughout the United States, the Netherlands and China, which included positions with LyondellBasell and its predecessor companies.
Olson says PureCycle has been able to attract some of the best people in the industry—employees with a can-do attitude. He acknowledges he himself might be a little too optimistic at times about the company’s potential.
“We’ve actually had some headaches getting the property up and running reliably,” Olson says of the Ironton facility, which is on the site of a former Dow plant and next door to an AmSty plant making polystyrene and styrene monomer.
Those issues have been mechanical in nature, Olson says, and are not related to the purification technology, which PureCycle licensed from Procter & Gamble in 2017 and has been working as expected.
Preparing for ramp-up
Headquartered in Orlando, Florida, PureCycle completed construction of its Ironton plant at the end of April and submitted documentation for formal certification of completion to the site’s independent construction monitor.
At that time, Olson told Recycling Today that PureCycle’s bondholders hired the independent company to monitor and certify the project upon completion, which was required to achieve key milestones in connection with financing for the facility.
The company prepared final closure documentation consistent with the third party’s requirements and received certification May 1.
The site’s 75 employees then turned their attention to producing pellets, and, as of mid-June, had completed the first run of UPR PP from postindustrial material at commercial scale.
Olson said PureCycle then planned to “build upon this accomplishment to optimize our process in order to demonstrate our technology across a variety of operating conditions and feedstocks.”
But, according to a report the company filed Sept. 13 with the Securities and Exchange Commission (SEC), severe storms in early August caused a two-hour power outage at the Ironton facility, leading to the failure of a seal Aug. 25. The facility was offline for four days for evaluation. The same mechanical component suffered a catastrophic failure Sept. 3, and two repairs were attempted before the component was replaced Sept 9.
PureCycle provided notice of a force majeure event Sept. 13 and, as of press time, said it did not expect to meet its bondholders’ Sept. 30 production milestone, requiring 4.4 million pounds of recycled PP to be made in a month.

“Since the force majeure declaration, we have been in active discussions with bondholders to reevaluate project deadlines and work toward resolving the matter," Olson tells Plastics Recycling.
In a document titled “Ironton Operations Update” dated Sept. 13 that was submitted with the SEC filing, the company writes that the Ironton operations team “is growing into a 24/7 operation, but at times it means slowing down to ensure the development of the right experience. This complements our intent to safely, reliably and methodically operate the Ironton facility.”
“We have a very strong safety culture here, where we are all about doing it the right way every single time,” Olson tells Plastics Recycling. “We hold that to the highest standard, so we do not compromise.”
He adds that a previous delay at the Ironton site was related in large part to ensuring the safety of the site engineering, saying, “I understand why our investors and shareholders want to see this plant succeed. No one wants to get this plant up and running at full capacity more than I do, but safety has to come first. We’re going to be purposeful. We’re going to be methodical. We’re going to be careful with everything that we do.”
The process
What PureCycle is doing in Ironton is divided into two areas: prep and purification.
Before the recovered PP enters the purification plant, which Olson refers to as a “molecular washing machine,” it undergoes preprocessing, or PreP, which is a conventional grinding process. Incoming bales are broken, and the PP is washed and reduced in size before it can go on to the next process, which consists of seven main stages as the company explains on its website:
- Melting and filtering of the reclaimed, ground PP removes large contaminants.
- In the polymer/solvent mixer and extraction column, the PP is introduced to the solvent solution at conditions that start the purification process. During extraction, the solvent pulls out color and odor from the solution.
- In the polymer mixer, additional solvent is mixed with the PP solution to reduce the polymer concentration before the large particle settler allows contamination and other plastics, also known as insoluble solids and polymers, to settle out of the process.
- Conditions are altered to create an environment where similar things stay together, and the solution is filtered to remove micron-sized particulates.
- The solution is further polished through contact with a solid, media-packed filtration column, removing color, tiny particles of contamination and other contaminants based on their physical and chemical properties.
- Process conditions are altered to separate the purified PP from the solvent added initially. The PP settles in the product decanter, where the remaining solvent is removed and returned to the feed tank for reuse.
- The purified PP is fed into the final product extruder and additives that the process removed during the final extrusion are added back.
Olson says the PP spends approximately 12 to 16 hours in the purification process.
The process itself does not use heat. However, the company uses steam to heat the outside of the pipes in its molecular washing machine, which facilitates the movement of the PP through the system.
Reusing the solvent is “environmentally friendly and also cost-effective,” Olson says. “We’ve got really low variable costs. We don’t use a lot of electricity, steam or solvents. We don’t use any catalysts … it’s really like a washing machine.”

Improving circularity
PureCycle says its process helps it to close the loop on end-of-life plastic while making recycled plastics more accessible at scale, something Coombs and Olson say is necessary.
“Plastic is super efficient, very lightweight and very versatile,” Coombs says. “It makes life better in so many ways. But the waste problem has to be solved, and that’s what we’re trying to do.”
He says PureCycle’s advanced recycling process is low in carbon emissions and produces a high yield of recycled PP that is as good as or better than virgin plastic.
According to PureCycle, the Ironton facility is projected to use 79 percent less energy than the production of virgin PP and is estimated to release 35 percent fewer carbon emissions than new PP manufacturing.
Planning for growth
As it ramps up production at the Ironton site, PureCycle also is executing a growth strategy that includes a second purification location in Augusta, Georgia, with initial site development expected in the fourth quarter of this year, as well as two new PreP locations to supply that plant. The company says additional projects in South Korea, Belgium and Japan also are making progress.
The company broke ground on the Augusta plant, which is in the Augusta Corporate Park, in early 2022. That site will house up to eight purification lines that collectively will be able to produce approximately 1 billion pounds of recycled PP annually, according to the company. Last August, PureCycle announced plans to add a PreP facility at the Augusta site that will be able to sort 263 million pounds of plastic annually and wash 331 million pounds annually.
To support the Augusta purification plant, PureCycle also announced plans for a PreP facility in Denver, Pennsylvania, with the ability to sort 175 million pounds annually.
The company’s team in Belgium has continued site engineering work at the Port of Antwerp to support the permitting process, which is expected to be completed by late 2024, according to an Aug. 8 update from PureCycle, while its joint venture team in South Korea has been working on engineering plans and evaluating various feed sources in accordance with the priorities defined by the joint venture with SK Geo Centric. The company continues its joint venture agreement discussions with Mitsui in Japan that began in late 2021, and PureCycle says the agreement is expected to be executed in the fourth quarter of this year and the list of purification plant locations to be narrowed down as well.
The company’s plans are ambitious, but Olson says determination and discipline will lead to success.
He describes PureCycle as being at the intersection of entrepreneur and establishment. “We’ve got to have a can-do attitude,” Olson says. “But we’ve also got to have a sense for how to build the right system to run it long-term. And we find that challenging but also awesome because it’s like a true example of diversity in action: Diversity of technology, diversity of experience, diversity of concepts, diversity of science. The intersection of all that is where this kind of concept begins to work.”
Get curated news on YOUR industry.
Enter your email to receive our newsletters.
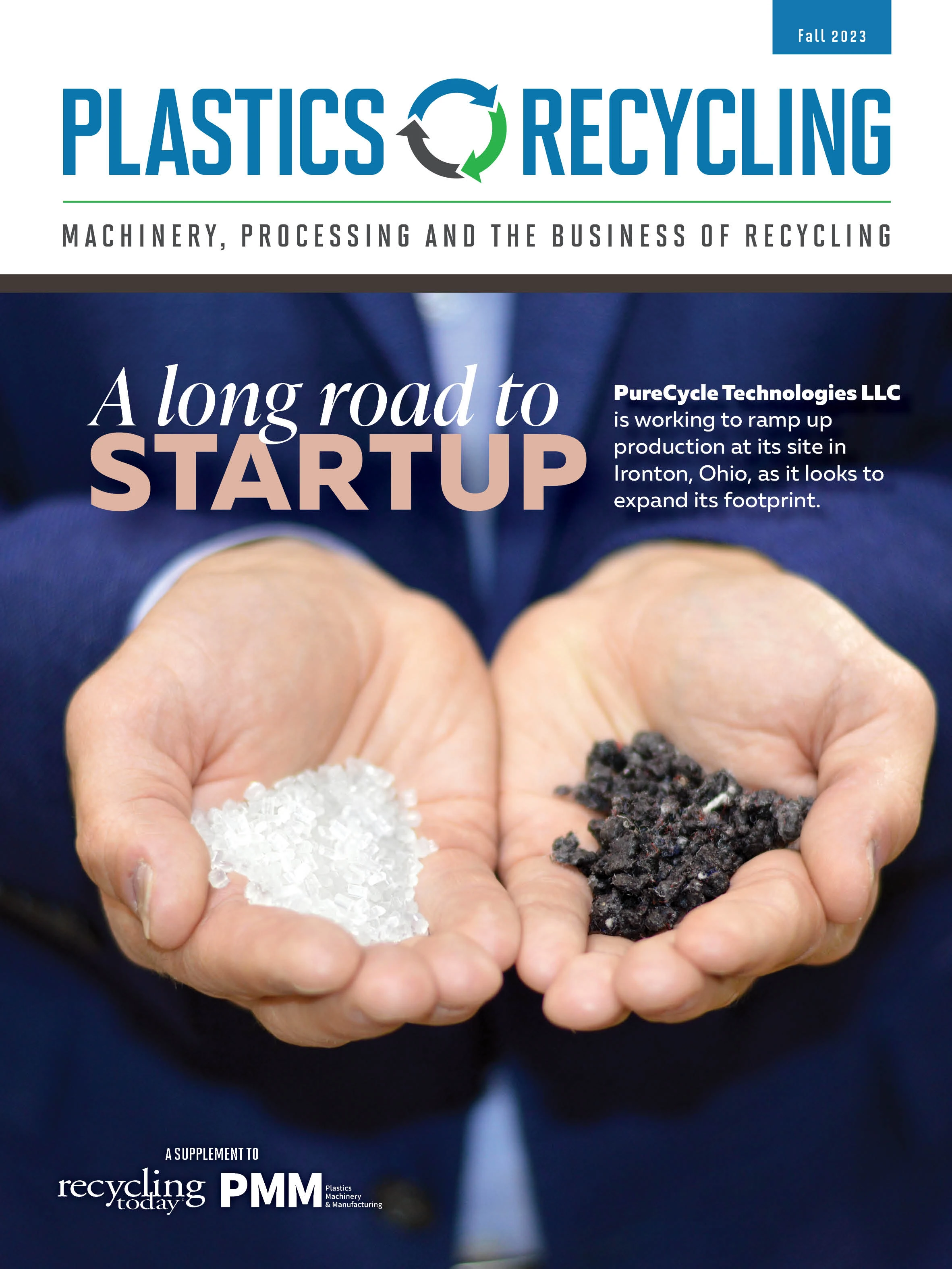
Explore the Fall 2023 Plastics Recycling Issue
Check out more from this issue and find your next story to read.
Latest from Recycling Today
- New Jersey officials award $16.2M in annual recycling, waste reduction grants
- Linder Industrial Machinery announces leadership changes
- First phase of EPR scheme launching in Alberta
- Veolia technology helps PetStar with water conservation
- Athens Services terminates contract with San Marino, California
- Partners develop specialty response vehicles for LIB fires
- Sonoco cites OCC shortage for price hike in Europe
- British Steel mill’s future up in the air