In 1983 a young Doug Raisch had only been out of college a few years, but was managing his family’s company’s products division, Raisch Products, in northern California.
Included were two natural stone quarries that allowed customers to dump their waste concrete and asphalt at those sites when they loaded up their trucks with stone. He admits that at the time, the quality of the quarries’ stone wasn’t good enough to make even a high-quality road base, let alone concrete aggregate.
The company needed new, good hard rock deposits, but where to economically get them anywhere near the rapidly expanding Bay Area? He was mulling this question over one day while standing on a pile of the waste asphalt and concrete, when he looked down and realized he already had plenty of hard rock tied up right there. All he had to do was figure out how to unlock the material.
Entering the Secondary Industry
Today, Doug Raisch is president and CEO of Raisch Companies, with its biggest subsidiary being Raisch Products, a construction materials concern based in San Jose, Calif.
The company was born out of a firm started in 1851 by Raisch’s great-great-grandfather, an original 49er who went bust looking for gold but found success cobblestoning streets and laying sewer in early San Francisco.
Recycling is now half of this company’s more than $30 million a year business, and according to Raisch, “recycling is our business, not secondary or tertiary like some of our competitors.”
But integral parts of Raisch Products include its two hot-mix asphalt plants and two quarries, and both figure in the recycling mix. Raisch Products owns two 2-stage crushing spreads and operates four concrete/asphalt recycling yards, or “urban quarries” as Doug Raisch calls them, around the south end of the San Francisco Bay.
Raisch said the two crushing plants are almost identical, although they were purchased at separate times. Both have 30 inches-by-54 inches Cedarapids jaw crushers, Diester 6 feet-by-20 feet triple-deck screens, and Eljay 4-1/4-feet rollercones. They are similar, says Raisch, because he believes in the Southwest Airlines equipment model.
“Southwest relies basically on one type of plane. It makes it easier for different crews to run and repair the equipment and lowers the number of spare parts that need to be kept around.”
The plants are used for both recycling and natural stone processing. The cone crushers have expandable chambers that allow them to be more easily dug out when they are buried. In addition, the company has developed a screen cloth able to handle wire mesh. Such ideas were not in place when the company began recycling, Raisch says.
Raisch Products started out recycling asphalt, trying to separate the already-sized aggregate while avoiding creating any more fines. At first they used a small crusher, putting 5-feet-long chunks in and expecting 3/4-inch pieces out. Production rates, understandably, were very low. Raisch says they must have spent “about $1 million” developing their current recycling system. Most of the asphalt currently recycled is fed into the company’s hot-mix asphalt plants.
Raisch Products also processes concrete rubble. Doug Raisch says his company was the first in Northern California to do that, and was able to meet the Class II base specification from CalTrans, California’s department of transportation, right from the beginning. “The biggest issues for recycled road base always have been the deleterious materials,” says Raisch. “We have found ways to successfully remove virtually 100% of the unwanted material.”
Cultivating the Market
The next step was convincing the region’s road owners and builders to use the recycled material. The contractors found the material had excellent workability and it set up nicely, says Raisch. Most local highway agencies have seen the economic benefits of using recycled road base, if only for saving on the tipping and transportation costs.
For example, Sunnyvale, Calif., said that in 1986-1987, Raisch was responsible for saving the city nearly $2 million in tipping fees. Savings like that continue today, although hardly anybody brings the material to the landfill sits any more. Any that does go there is immediately set aside for temporary roads.
However, there still are a few local agencies that have not yet seen the light on recycled road base, according to John Armando, Raisch’s manager of marketing, business development, and recycling. “There are still a few holdouts,” he says. “They are concerned about leachate from the asphalt, or might think that natural aggregate is better. It is really just an ongoing education process to show them the facts.”
Another idea Armando believes in is the need to have all recyclers legally permitted. Raisch Products has crossed the “t”s and dotted the “i”s for its permits. Some other crusher operators in Northern California have not, he contends. “Permitting is difficult to get in California,” he says. “Because it is so difficult, some companies don’t take all the necessary steps. The problem is that Raisch and some others jump through the hoops to get the permits, take on that added expense, and then you have the contractors who come through, aren’t permitted, make serious mistakes, and give the industry a bad name.”
Recycling concrete and asphalt is a thriving business is Northern California, said Armando. “We can sell everything we process,” he says. In 2000 Raisch Products processed about 750,000 tons.
Raisch’s two-stage systems lend themselves to bigger jobs, says Armando. It takes more than a day to set up the large plants, and another day to knock them down for moving. For that reason, Raisch Products markets itself mostly for very large onsite jobs, or keeps the plants working in their recycling yards. “Our current minimum job size is 70,000 tons,” says Armando. “To bring a plant like ours on site for 30,000 tons is not economically feasible.”
Onsite crushing for smaller projects is something Raisch Products is seeing done by others and is monitoring and is considering doing itself. “(Onsite) is not having an impact on our business yet,” the company owner says. “It is not affecting the amount of material coming into our sites. At some point it may, and we may enter the market.”
Does not entering that market allow for competitive entry by other companies? “That is difficult to tell,” Raisch comments. However, because of the large population base in the area Raisch Products covers, he expects a consistent stream of waste material to continue to come in to be recycled.
Beyond Rock Crushing
Raisch Products has been aggressive in other related recycling markets. One ongoing project has the hot-mix asphalt plants using the fines generated by a nearby glass recycler into a mix with the company’s natural aggregate in order to make a road base product.
Also tested was the use of processed waste asphalt shingles in hot mix, a test that was successful on the newer of Raisch’s two hot-mix plants, according to Armando. The company was able to successfully incorporate various percentages of the shingles into the hot mix. Says Armando, “Asphalt shingle recycling is the next up-and-coming market. Someday it will be as accepted as concrete and asphalt recycling, and none of it will go to a landfill.” He cautions, though, that there is still a lot of work to be done, especially in the processing arena. “Once this is resolved I think you will see a bigger market for this material, and more people doing it.”
Armando is a long-time proponent of another cutting-edge idea in C&D, an “eco-park” for C&D recyclers. There, recycling companies of different capabilities would gather in one site and process waste, either from outside or from each other, such as the glass fines cited above. None for C&D have been developed so far, and the hang-up remains the costs of land.
“It’s a Catch-22,” Armando says. “If an urban area needs an eco park, there isn’t enough economically priced space in which to put it. And if you have the space to put it in, say way out in [a rural area], you don’t have the material and markets to support it, or the transportation costs will kill you. A lot of cities that are starting to grow need to set aside property for this type of recycling application,” he states.
Raisch Products itself has been thinking this far forward for some time. Doug Raisch’s great-great-grandfather founded the basic building blocks of the modern company in 1851, after failing as an original “49er” looking for gold. Today, Raisch Products has found gold in the recycling industry.
The author is C&D Recycler’s associate publisher and is executive director of the Construction Materials Recycling Association. He can be contacted via e-mail at turley@cdrecycling.org.
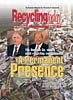
Explore the January 2001 Issue
Check out more from this issue and find your next story to read.
Latest from Recycling Today
- ReElement, Posco partner to develop rare earth, magnet supply chain
- Comau to take part in EU’s Reinforce project
- Sustainable packaging: How do we get there?
- ReMA accepts Lifetime Achievement nominations
- ExxonMobil will add to chemical recycling capacity
- ESAB unveils new cutting torch models
- Celsa UK assets sold to Czech investment fund
- EPA releases ‘National Strategy to Prevent Plastic Pollution’