
In 1994 when naming the Newell Shredder a National Historic Mechanical Engineering Landmark, the American Society of Mechanical Engineers (ASME) stated:
"Mr. Newell’s original metal shredders were designed to shred steel cans for a leach precipitation process used to refine copper. Demand for the material grew, and as it did the Newell family developed larger shredders to process heavier material."
In the early 1960s, Sammy Proler identified that steel mills using electric arc furnaces could benefit from using shredded, or fragmented, steel scrap. The Prolers had also been shredding steel cans for the copper industry. While the Prolers may never have invented a shredder, they were pioneers in shredding scrap steel with other equipment.
Realizing the market potential for supplying fragmented scrap to steel mills, Alton Newell and Scott Newell Jr. set out to build still larger shredders, which eventually led to being able to shred an entire automobile.
With the realization of one brilliant idea, Alton Scott Newell Sr. revolutionized the scrap metal industry and significantly contributed to the ongoing effort to recycle used metals and conserve the Earth’s precious resources.
Driving continuous innovation
While today the industry refers to shredded scrap, it is technically fragmented steel for recycling. That aside, the Newell family, realizing the market potential, began engineering and manufacturing ever more advanced machines for its operations.
During the 1960s the Newells had metal recycling facilities in San Antonio, Austin and El Paso, Texas, as well as in Tucson and Phoenix, Arizona. They were not manufacturing shredders for others, only for their own use. That changed when a manufacturer from Iowa came to visit Alton Newell to learn more about the shredders they were building with the intention of licensing the technology. Instead, that group set about making its own version of the equipment.
When Alton Newell learned of what he considered a betrayal, he asked his son, Scott Newell Jr., to establish a manufacturing operation in San Antonio and go into business selling shredders. As production at the works grew, the Newell shredder became famous worldwide for its efficiency and productivity. This led to Newell licensing Lindemann of Germany to build Lindemann Newell shredder plants and Fuji Car Mfg. of Japan to build Fuji Newell shredders. Eventually both of these licensees were sold the right to continue to use the Newell designs but on a nonexclusive basis. This led to Newell selling shredding plants directly to users all around the world.
Alton Newell had grown up in the salvage business dismantling cars by hand. He, his family and employees used axes, chisels, hammers and more in the process. That experience informed the design of Newell shredders. While Alton Newell never graduated high school, he was self-taught and eventually was given two separate honorary doctorate degrees. With this self-taught knowledge and experience, he continued to improve the design of shredding plants.
While the original Newell shredder was a side feed and top discharge, the continuing evolution of the equipment, resulted in a side feed, top and bottom discharge shredder. Conventional shredders of the time were top-feed, bottom-discharge. The Newell design allowed the machine to operate with far less horsepower and a smaller rotor. The smaller motor and rotor made the machine more economical. That lowered the initial capital requirements, which allowed shredding steel scrap to become more widely adopted.

An endless quest for efficiency
As Newell produced more shredders, the company learned even more along the way. A unique advantage Newell had was the family members were not just manufacturers, they were operators. At its peak, Newell family processing operations produced one million tons of shredded steel annually. That gave them a huge incentive to learn how to lower the cost per ton to shred.
Among the most important enhancements Newell made to the shredder were:
- the double feed roller;
- the gathering box at the top discharge grate;
- top and bottom discharge grates;
- a discharge reject door for unshreddables;
- understanding the capacity of electric motors; and
- providing operating software.
While many companies copied the Newell shredder, they did not understand the “why” that underpinned the design. Companies hired ex-Newell employees and copied the Newell design by making imitations of existing plants. The Newell family insists, however, that these machines were never as productive as a Newell.
Newell used this productive and efficient shredding equipment to become the, by far, leading manufacturer and supplier of shredding plants around the world.
The reason is simple: the Newell machines are more productive and deliver a lower cost per ton processed. Today it is fair to say that more than 50 percent of the shredders worldwide were either built by Newell or licensed by Newell. The vast majority of the remainder are based upon Newell designs.
Today, more than ever
Scott Newell and his Son Scott Newell III have continued to drive innovation in the metals shredding business. Most recently Newell has introduced a new grate design that enhances tons-per-hour production while significantly increasing material density and preventing pokers from entering the downstream system.
The advanced software platform controlling the shredding plants seamlessly integrates feed-roller speed to maximize the thermal capacity of the shredder motor, maximizing production. The systems also monitor and log all downtime occurrences so these can be managed and avoided.
If you are seeking the most productive shredder for ferrous scrap and materials liberation for downstream materials recovery, don’t compromise. Go with a Newell. The family will not only supply a shredding plant but also welcome you into a community of operators dedicated to maximizing production, recovery and value.
Get curated news on YOUR industry.
Enter your email to receive our newsletters.
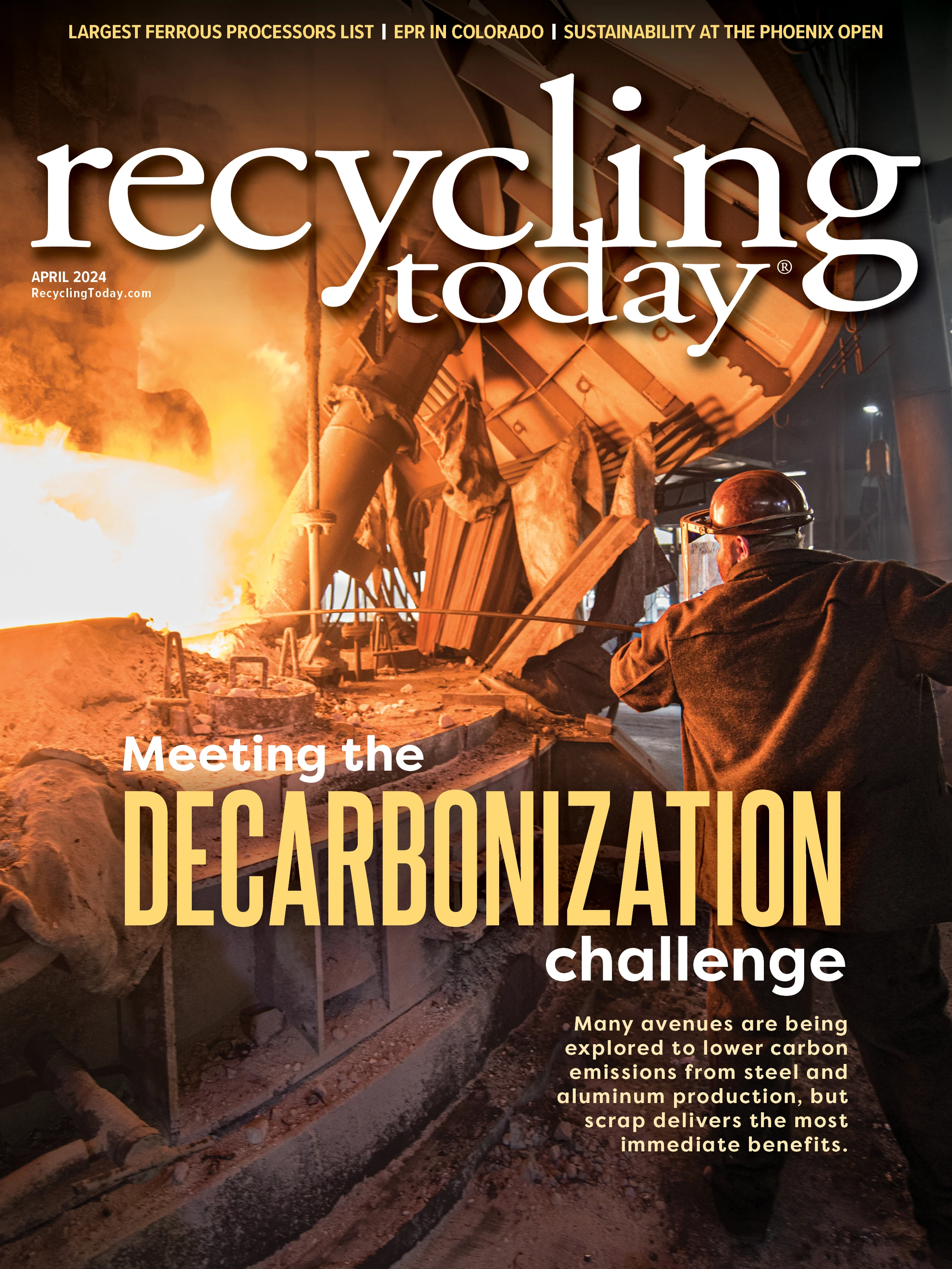
Explore the April 2024 Issue
Check out more from this issue and find your next story to read.