
Worn shredder knives reportedly are the most frequent and costly cause of downtime in tire recycling. Increasing wear life by using the correct hardfacing on knives can mean substantial savings for operators.
Knives can be hardfaced in-house for those with proper welding and preheat equipment, outsourced to skilled shops or purchased from selected original equipment manufacturers (OEMs).
Mike Korba, inside sales coordinator at Postle Industries Inc., based in Cleveland, answers some of the most common questions recyclers have when it comes to hardfacing and its application to shredder knives used in tire recycling.
Q: How do shredder knives wear out?
Mike Korba (MK): The actual wear mechanism that takes place is not completely understood as several mechanisms likely are at work. Because of the metal in tires, it would be logical to think the mechanism is metallic wear, or galling. However, many tires come through the shredder embedded with sand, dirt or grit that would lead to abrasion as the wear mechanism. The occasional hammer, rock or other foreign debris also can be present, making wear by impact the contributing factor in these cases. All three are working at some level, perhaps resulting in microchipping of the edge. Heat and corrosion also can contribute.
OEMs generally supply quenched and tempered (Q&T) low-alloy steel knives that tend to wear quickly. Restoring the cutting edges with a hardfacing alloy that is more wear-resistant extends knife life.
Q: What is hardfacing and why should it be considered for this application?
MK: Hardfacing is an arc welding procedure to deposit wear-resistant alloys on new or worn parts to extend longevity. In the case of shredder knives, that longevity can be as much as eight-times longer than OEM Q&T knives. Longer knife life means less downtime and increased productivity.
Q: Why do hardfaced knives outproduce OEM Q&T knives?
MK: Hardfaced knives outproduce OEM knives because of their alloy content. OEM knives usually are made from a Q&T low-alloy steel, such as 4340 (about 4.2 percent alloy) or 4140 (about 2.3 percent alloy), and range in hardness from mid-40s on the Rockwell C (RC) scale to low 50s RC. A hardfacing alloy that contains more elements within the alloy necessary to combat various wear mechanisms and has an as-welded hardness around 62 RC is recommended.
Q: Is the hardfacing of shredder knives a proven technology?
MK: Hardfacing as we know it has been used for centuries, and tire shredder knives have been hardfaced since the time tires began to be shredded. Different applications require different chemistries, or alloys, to combat different types of wear.
Q: How is hardfacing applied?
MK: Hardfacing for shredder knives is almost exclusively done by the gas metal arc welding process with a cored wire, direct current power supply, wire feeder and argon-based shielding gas. The preferred wire is a small diameter, high-carbon, high-alloy cored wire specifically designed to maintain a cutting edge and deposit an alloy to resist abrasion, metal-to-metal wear and impact—more accurately, a premium tool steel.
Preheat and interpass temperatures range from 600 F to 700 F (316 C to 371 C), and deposits are slowly cooled to yield an as-welded hardness of 62 RC. Tempering usually is not required.
Q: Can I just ask for harder knives from the OEM?
MK: Sure, but it will not buy you much more longevity. Hardness is not a good measuring stick to use to evaluate wear; rather, it is the metallurgical composition and microstructure that counts. If OEM Q&T knives were hardened to 62 RC, they still would not perform as well as knives hardfaced with a premium tool steel.
Q: I thought hardfacing alloys always check crack?
MK: It is true many arc-welded deposits have check relief cracks, but not all. An alloy that does not crack is recommended. Occasionally a crack will develop upon rebuilding, but they are not detrimental.
Q: How much better are hardfaced knives over OEM Q&T knives?
MK: It has been reported that in some operations, a set of OEM Q&T knives may only last two weeks, while hardfaced knives may last up to two months. The numbers are so impressive that many OEMs are hardfacing new Q&T knives and participating in the rebuilding process.

Q: How many rebuilds can I expect out of a set of knives?
MK: It depends on how badly they are worn and the size of the knives. Large knives are worth salvaging and can be rebuilt indefinitely if the bulk hardness does not drop significantly because of the heat of the hardfacing process. Excessive deposit cracking also limits rebuilds. In many cases, removing old hardfacing and starting over is all it takes to increase the number of rebuilds. Rebuilding smaller knives with excessive wear might not be economically feasible.
Q: How long can I expect a set of hardfaced knives to last?
MK: That depends on several factors. Passenger tires are easier on the knives than truck tires. Removing the truck tire bead helps increase knife life, and removing debris such as metal parts, sand and rocks help increase wear life.
Proper welding, preheating and postheating procedures help ensure hard, tough weld deposits, and this usually leads to longer wear life. Shortcuts can produce disastrous results.
Q: Can the base alloy be changed?
MK: Yes, 4340 and 4140 base materials can be changed to a tougher, more wear-resistant alloy, such as abrasion- resistant (AR) 400, 450 and 500 steels.
AR knives are not affected by the heat of hardfacing, if proper welding procedures are followed and excessive heat is not generated. AR knives also are easier to weld on because of their lower carbon content.
Hardfacing alloys easily can be welded on AR plates, providing proper techniques are maintained.
Q: Do OEMs hardface knives?
MK: Yes, many will supply new knives with hardfacing and also will hardface worn knives. Check with your vendor to determine if its knives are hardfaced.
Q: What types of hardfacing weld beads are used?
MK: Stringer beads as well as a slight-weave bead are preferred for the cutting edge faces. Generally they are ½ inch (12.7 millimeters) wide but could be wider to support the hard weld metal.
The sides can be solid across the thickness direction or in an X-crosshatch pattern. The area around the hex hole or shaft hole also can be hardfaced up to ½ inch (12.7 millimeters) wide.
Some machines allow material to get down between the knives, increasing the operation’s horsepower requirements.
Hardfacing the areas between the shaft hole and cutting edges with circular or weave patterns aids in shredding this material and reduces the overall horsepower needed.
Hardfacing makes good economic sense, and in an age when steel is at a premium and lead times are long, it might be the only way for a tire shredding operation to maintain productivity and profitability.
Get curated news on YOUR industry.
Enter your email to receive our newsletters.
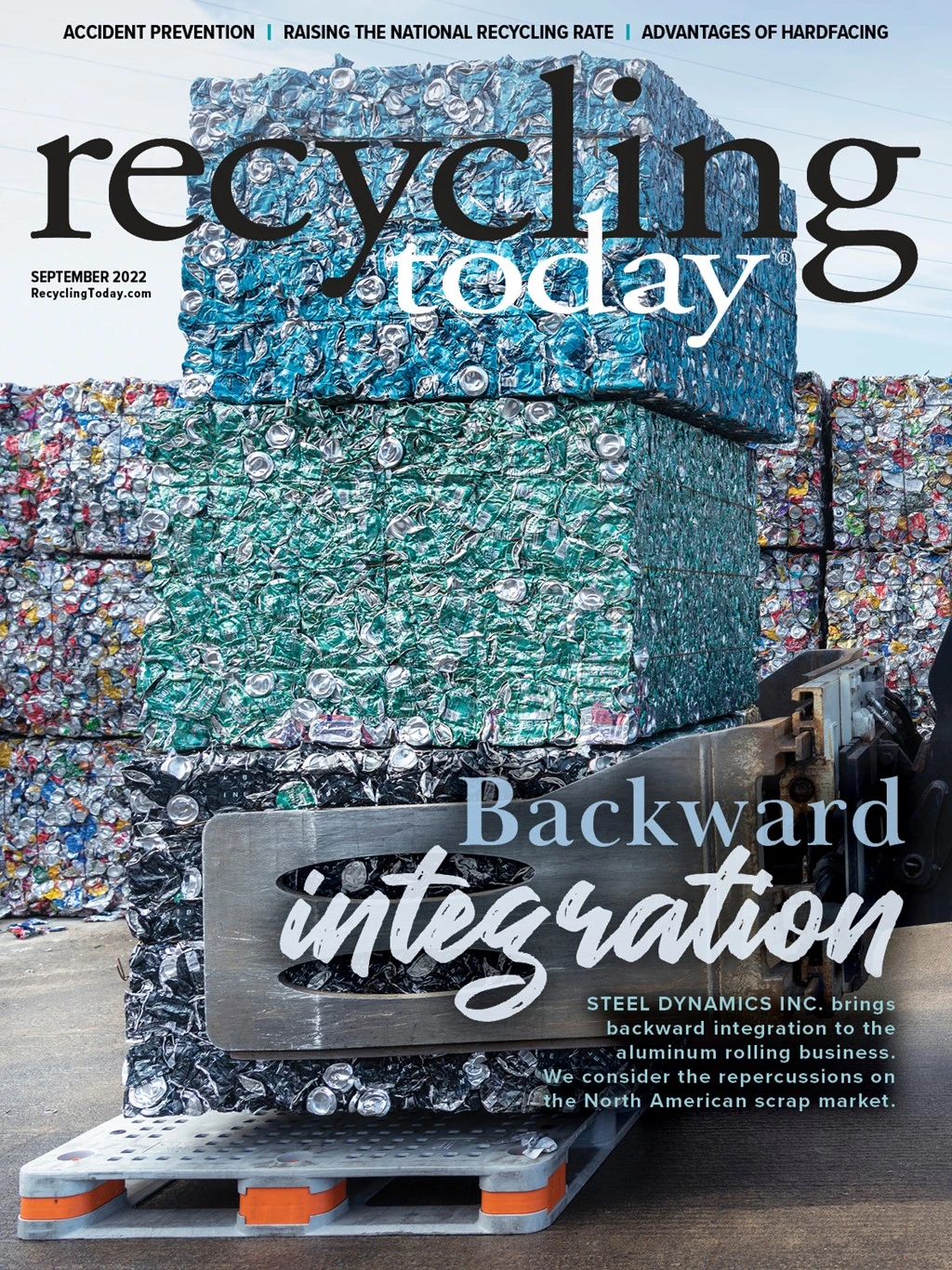
Explore the September 2022 Issue
Check out more from this issue and find your next story to read.
Latest from Recycling Today
- Astera runs into NIMBY concerns in Colorado
- ReMA opposes European efforts seeking export restrictions for recyclables
- Fresh Perspective: Raj Bagaria
- Saica announces plans for second US site
- Update: Novelis produces first aluminum coil made fully from recycled end-of-life automotive scrap
- Aimplas doubles online course offerings
- Radius to be acquired by Toyota subsidiary
- Algoma EAF to start in April