One way to process scrap tires is to grind them down, remove the steel and fiber, take the rubber and make it as fine a particle as possible. This powder, in turn, can be used as an additive in new products, held together by special binders to enhance the products’ design.
Edge Rubber At A Glance |
Location: Chambersburg, Pa.
Facilities: One 33,000 square-foot building
Employees: 38
Equipment: Wet and ambient grinding machine lines, plus two trucks
Product: Crumb rubber and powder (30 to 200 mesh)
Output: 40 million pounds of crumb annually
Customers: Tire manufacturers, brake lining companies, paints and coatings |
Edge started out as Baker Rubber in 1988. Then, after various company changes, Edge Capital I, an investment group based in Michigan, bought the company in 2003 and infused new cash and a new attitude. Ever since, Edge has been growing at a rapid pace.
SECOND-TIER ACTION
"We have been able to achieve a 20 to 30 percent growth rate per year since 2003," says Sam Kauffman, vice president and chief operating officer of Edge. "That’s because we have focused on sophisticated applications for our end product." Those applications include new tires, brake linings and paints and coatings. According to Kauffman, these industries provide year-round sales for his company. "Unlike the soil additive or asphalt paving industries, these high-end industries keep our plant operating five days a week, 24 hours per day. We did not want to be in markets that could not provide that stability for us."
Edge Rubber is a second-tier processor. The company does not deal with whole scrap tires, but instead buys shredded passenger and truck tires only from certain local processors.
In fact, Edge Rubber will only buy tires that have been shredded to about 1 inch. "Good quality has been a historical problem in our industry," say Kauffman, "so we want to make sure the product we are receiving meets our standards." Edge Rubber mainly buys shreds from processors that collect tires throughout Pennsylvania and into outlying regions, such as Columbus, Ohio; Buffalo, N.Y.; and Baltimore. Kauffman claims that this area provides all the scrap product the company needs for now.
When the shreds arrive at Edge Rubber, they can be processed in one of two ways—wet grind or ambient grind. Each has its own benefits. The wet-grind method (which uses a water slurry, which is later treated and filtered for discharge) produces the company’s finer-mesh products, from 40 all the way to 200 mesh crumb. In addition, Kauffman says that the crumb produced with this method has rough edges and "craters," which make it more receptive as an additive to the higher-end products, such as new tires and paints and coatings.
The ambient grind is simply a dry-grind method that breaks the shreds down to 30 or 40 mesh. This crumb can be used in applications such as brake linings and even the roofing industry. While ambient grind makes up 40 percent of the product, wet grind accounts for the other 60 percent produced by Edge Rubber. The company markets its products under the names Granulite™ and Micron™.
MARKETS AND QUALITY
The Long View |
Two terms commonly used in the crumb rubber industry are “mesh” and “micron.” Both terms are used to describe the size of the recycled particle. Mesh is a term used to describe the number of holes in a 1-inch by 1-inch screen. For instance, 40 mesh means 40 holes of the same size in an inch square. As the mesh number increases, so does the number of holes per inch, and therefore, the hole size decreases. So, 200 mesh would have 200 holes of the same size in a 1-inch square.
A micron is a unit of measure equal to about 39 millionths of an inch or 0.00039 inch. Or, 1 inch equals 25.4 mm or 25400 microns. Comparing mesh to micron, it works out like this: 40 mesh size is roughly 0.0165 inches or 0.42 mm or 420 microns. For 200 mesh, which is ultra-fine crumb powder, the numbers are more staggering: 200 mesh is the same as 0.0029 inches or 0.074 mm or 74 microns. |
Edge Rubber claims to supply 85 percent of all the recycled crumb rubber to new tire manufacturers. "There are some tire manufacturers where we supply 100 percent of the crumb," says Kauffman. Of the 40 million pounds of crumb Edge produces annually, 60 percent goes into the making of new tires, 20 percent to brake linings and 20 percent goes to paints, coatings and industrial applications.
To secure contracts in the "sophisticated product market," as Kauffman calls it, Edge Rubber has to maintain strict quality controls. The company’s on-site lab tests under ASTM International standards and accounts for levels of carbon black, hydrocarbon, moisture and acetone extractables, among others, using thermogravimetric analysis.
Another part of Edge Rubber’s success was its achieving ISO 9001 certification. "That certification was key to showing our customers that we are a quality-minded and controlled company," says Kauffman.
MOVING MATERIAL OUT
Although Edge Rubber ships most of its product FOB from its plant through customer-hired trucking, it has branched out with its own trucking operations by using two full-time trucks to deliver product and pick up incoming shred. The outgoing crumb product is bagged in many various sizes all the way up to a super sack which contains about 2,000 pounds of crumb.
Kauffman says that the company ships all across North America and routinely ships product to Brazil, Chile, China and Thailand. "There was some consolidation in the tire industry a few years back," says Kauffman. "Plants were closed or consolidated, so we were a little worried. But that industry has since settled down. Our biggest fear is some overseas operation ramping up and taking away that part of our business," he says.
As for some of the other issues facing the scrap tire industry, Kauffman says he believes a lot of progress has been made. "In our area, Pennsylvania and the Northeast, the scrap tire problem is virtually under control," he says. "You just don’t hear about people finding big piles of tires dumped somewhere anymore."
Kauffman also says he believes that adding a fee, suchas at the retailer, to cover the proper recovery and disposal of scrap tires certainly could help the first-tier processors that collect and shred the tires.
"Those savings can be passed all the way down the line," says Kauffman.
Currently, he sees the cost of high fuel prices affecting everyone, but feels that the first-tier processers may be affected more. "So far, we have really been immune to the shrinking economy," he says of his company.
GROWTH OPPORTUNITIES
Edge Rubber says it expects flat growth for the next year or so, but a spike in business around 2010. That is because the company is working with plastic manufacturers to create a hybrid material that includes conventional plastics and scrap crumb rubber. "Plastics is petroleum based, so the cost to produce it is going up," says Kauffman. "If we can help to bring that cost down, then we can expand our own business. We are definitely seeing more interest from the plastic folks."
In the meantime, Edge Rubber will keep doing business as usual by providing a quality product for many industries. "I feel that, in general, you have to be honest, fair and treat people with respect," says Kauffman. "Shaking my hand is OK with me if you want to do business—I can always read the legal jargon later."
The author is a freelance writer based near Cleveland.
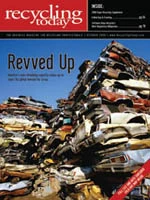
Explore the October 2008 Issue
Check out more from this issue and find your next story to read.
Latest from Recycling Today
- New recycling grant program launches in Massachusetts
- Tire Recycling Foundation names executive director
- Dock 7 named 2025 Exporter of the Year at New Jersey International Trade Awards
- Waste Connections reports ‘better than expected’ Q1 results
- Commentary: How EPR is transforming the packaging industry
- Acerinox names new North American Stainless CEO
- Greenwave closes 2024 books with red ink
- Steel Dynamics nets $217M on record shipments