Lehigh Technologies, based in Naples, Fla., combines a patented cryogenic preprocessing technique and a centrifugal screener from Kason, Millburn, N.J., to turn recycled tire granules into fine rubber powders. The company’s 80- to 140-mesh (177- to 104-microns) fine powders and its super fine powders, 140 mesh (104 microns) and finer, are opening new applications in sealants and coatings and expanding rubber powder consumption in new tires and recaps.
Recycled rubber particles have long been used as fillers and performance enhancers for more costly elastomers. Approximately 1 billion pounds will ship this year for use in carpet underlay, flooring material, belts, hoses, engine mounts and dampers, wire, cable, paints and adhesives. While the market has been growing at a robust 25 percent per year, even greater growth is predicted.
"As we make powders finer, the market for them becomes almost unlimited," notes Bill Meckert, Lehigh vice president of engineering.
A number of manufacturers ship rubber powders measuring 40 mesh (420 microns) and larger, and a few produce powders of up to 100 mesh (149 microns), but no one matches Lehigh’s 240 mesh (60 microns) rubber powder, according to the company. Ultra-fine powders in the 200- to 240-mesh (74- to 60-microns) range are essential for applications such as sealants and automobile undercoatings. These materials are applied using fine orifice nozzles that would clog if larger particles were used.
The smaller the particle size, the more rubber powder can be added to tires and recaps. Finer particles present a larger surface area for bonding and, therefore, lower the risk of delamination. Since recycled rubber powder costs about half the price of virgin material, the higher the powder content, the greater the cost benefits. One pound of recycled rubber added to a tire saves almost 1 gallon of crude oil, the amount required to produce an equal amount of virgin rubber.
PRODUCTION PROCESSLehigh’s manufacturing site in Tucker, Ga., is one of the largest and most-advanced rubber powder manufacturing facilities in the world. Here, the company’s proprietary technology is combined with commercially available industrial equipment to produce consistently sized rubber particles measuring 40 mesh (420 microns) and smaller that are sold under Lehigh’s Polydyne label.
The company’s raw stock is 100 percent recycled content, granulated rubber obtained from tire processors in sizes ranging from three-quarters of an inch (19.05 millimeters) down to 10 mesh (2,000 microns). Delivered in bulk bags or by truckloads, the material is dumped into a hopper and shaker-screened to classify the granules into sizes from 6 mesh (3,360 microns) to 14 mesh (1,410 microns). Granules exceeding 6 mesh (3,360 microns) are ground down before the sized material is stored in bins.
Upon demand, stock is drawn from the bins and fed by insulated screw conveyor into the liquid-nitrogen-cooled cryogenic chamber where temperatures, typically between -100 Fahrenheit to -130 Fahrenheit (-73 Celsius to -90 Celsius), is regulated based on the particle size desired. Freezing turns the rubber granules into a glass-like state that fractures easily during grinding in a high-speed attrition mill. After size-reduction, the material passes through a rotary drum magnet that removes steel belting that was freed during the grinding process.
SIMULTANEOUS JOBSAt this stage, the powder exhibits an oily texture and is electrostatically charged, causing the particles to agglomerate and making them difficult to screen. A flow aid, such as finely ground talc or fumed silica, is metered in, and the mixture is screw-fed into a Kason model MO-CS Centri-Sifter centrifugal screener that blends the two, causing the rubber particles to separate.
Inside the screener’s horizontally oriented cylindrical chamber, rotating helical paddles break up soft agglomerates and continuously propel the material against a 20- to 30-mesh (84- to 589-microns) woven nylon monofilament screen. The centrifugal force accelerates the on-size particles through the apertures and scalps any fiber from the tire cord. The fibers ball up like cotton and are discharged through the open end of the screen cylinder, along with any oversized rubber and residual steel from the tires.
"The Centri-Sifter screener, which we purchased from Cino Equipment Co., Berkeley Heights, N.J., does everything simultaneously, which is why we use this equipment," Meckert says.
The Centri-Sifter centrifugal screener’s ability to work efficiently within the demanding production environment contributes to the quality of powder processed on the line. Its heavy-duty construction makes it well suited for continuous inline operations, according to Lehigh. The unit is compact and operates quietly with vibration-free action. A large access door facilitates cleaning, and screens can be changed in less than two minutes.
THE FINAL STEPFollowing the Centri-Sifter screener, the rubber powder is discharged into a proprietary tumbler screening process that classifies the material. According to Lehigh, the line produces 2,500 pounds (1,134 kilograms) per hour of powder in sizes that range from 40 to 240 mesh, depending on the application.
Currently, products are shipped only within the United States, but at the request of Lehigh’s globally diverse customer base, the company will begin shipping its products internationally.
"Our growing production will ensure a good supply of powder for our customers and enable them to lower their production costs by increasing the amount of recycled material in their products," Meckert says.
In the future, Lehigh foresees blending rubber with plastics to increase their durability and flexibility as well as to improve their UV resistance so they are less susceptible to brittleness and cracking from sunlight. This application, which is still in the embryonic stage, will require even finer rubber powders than are now being produced, and, according to Meckert, Lehigh Technology’s centrifugal screener will adapt to the new requirements with a simple change of screens.
This feature was submitted on behalf of Lehigh Techologies (www.lehightechnologies.com) and Kason Corp. (www.kason.com).
Get curated news on YOUR industry.
Enter your email to receive our newsletters.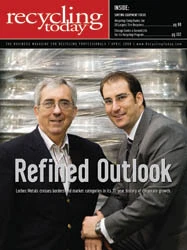
Explore the April 2008 Issue
Check out more from this issue and find your next story to read.
Latest from Recycling Today
- Athens Services terminates contract with San Marino, California
- Partners develop specialty response vehicles for LIB fires
- Sonoco cites OCC shortage for price hike in Europe
- British Steel mill’s future up in the air
- Tomra applies GAINnext AI technology to upgrade wrought aluminum scrap
- Redwood Materials partners with Isuzu Commercial Truck
- The push for more supply
- ReMA PSI Chapter adds 7 members