
Wieland Group is the world’s leading supplier of semifinished products made from copper and copper alloys. The 200-plus-year-old company established in 1820 in Ulm, Germany, has expanded to 80 locations across Europe, North America and Asia and continues its growth, investing in its operations in response to the megatrends of globalization, urbanization, digitization and decarbonization that require copper.
Wieland is increasing its recycling and melting capacity in Europe with an 80 million euros ($85.8 million) investment at its Vöhringen, Germany, facility, which was announced in fall 2022. It says the approximately 80,000 metric tons of additional annual recycling capacity “represents a significant next step in the company’s strategy to expand its recycling capabilities worldwide.”
That investment joins another major investment in Shelbyville, Kentucky, which broke ground in June of 2022. The 78-acre site will be able to produce approximately 85 million pounds of low-carbon copper annually, with room for significant expansion.
The recycled content in Wieland products will reach an average of 80 percent globally after these facilities come online, the company says, but it has a larger number it’s working toward.
Matt Bedingfield, president of recycling, Wieland North America, says the company has committed to 90 percent recycled content in its products by 2030, and its investments in the U.S. will play a significant role in achieving that.
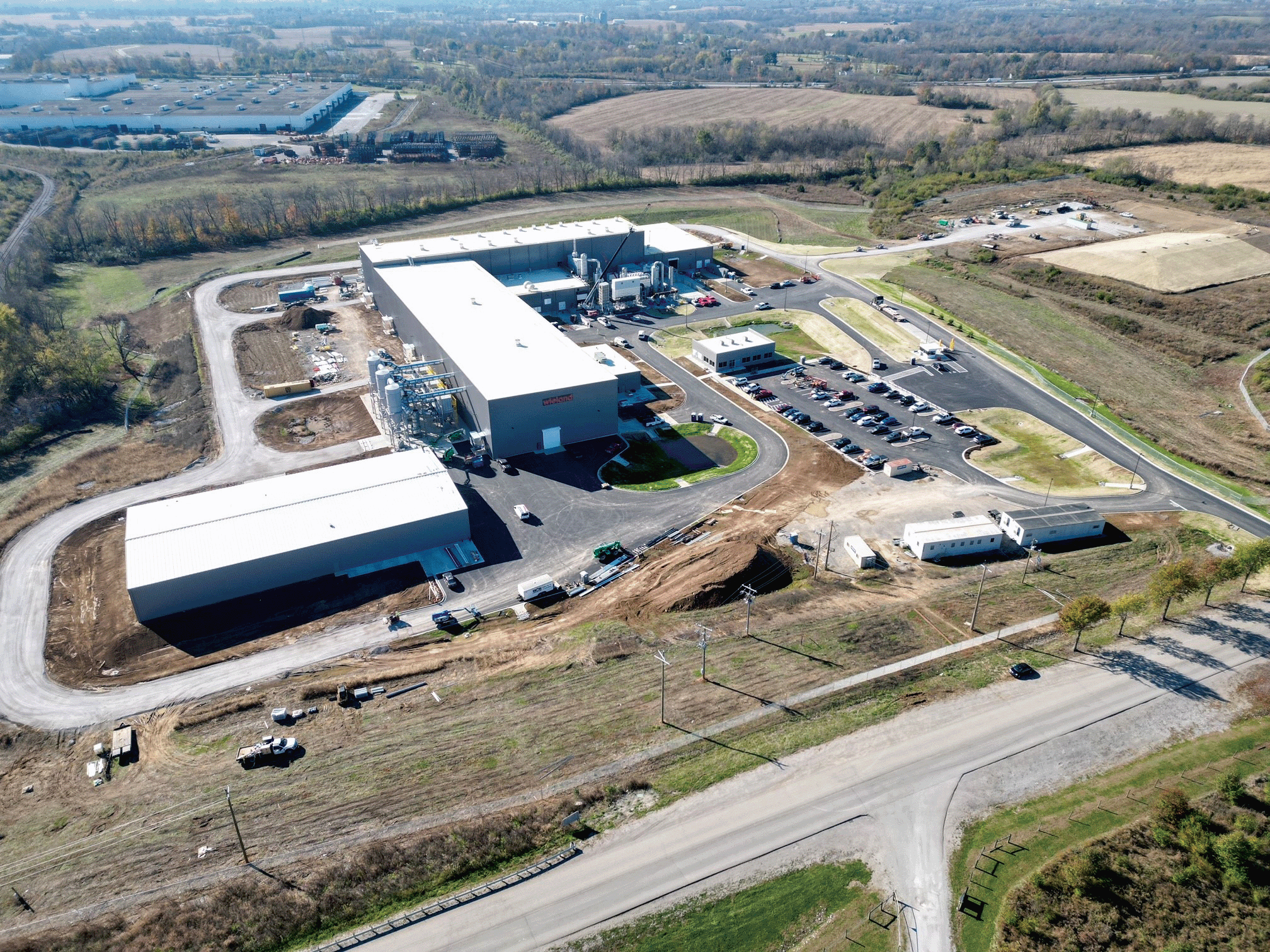
Expanding in America
Bedingfield references Wieland’s long history of operating in the U.S. but notes its purchase of Global Brass and Copper (GBC) in 2019 took it to a new level.
GBC was a converter, fabricator, processor and distributor of specialized nonferrous products, including a range of sheet, strip, foil, rod, tube and fabricated metal component products. The company operated under the Olin Brass, Chase Brass and A.J. Oster brand names in North America and specialized in processing copper and copper alloys. It used scrap, virgin metals and other refined metals to melt, cast, roll, draw, extrude, weld and stamp finished and semifinished alloy products.
Bedingfield says the acquisition enabled Wieland to get its rolling, extruding and distribution capabilities in the U.S. to match those in Europe.
Since the GBC acquisition, Wieland has acquired 13 other companies in the U.S. Most recently, it purchased Farmers Copper Ltd., a copper, brass and bronze alloys supplier founded in 1980 with two operating sites in San Antonio and Texas City, Texas, that serve the aerospace, marine, defense, oil and gas and electrical market segments. It also recently purchased Small Tube Products, a principal producer of small-diameter and thin-wall specialty tubing made of copper, copper alloys and aluminum headquartered in Duncansville, Pennsylvania. Its precision redraw tube mill serves the automotive, electrical, transportation, heat transfer, welding and consumer product industries.
“We see North America as an extremely attractive market. These markets are in need of more and more copper as we move forward toward the sustainable future. We are seeing rapid movements toward green energy and the electrification of vehicles.” – Matt Bedingfield, president of recycling, Wieland North America
“We see North America as an extremely attractive market,” Bedingfield says, noting Wieland supports a strong manufacturing base in the country’s automotive, aerospace, building construction and HVAC sectors. “These markets are in need of more and more copper as we move forward toward the sustainable future. We are seeing rapid movements toward green energy and the electrification of vehicles.”
Following Wieland’s announcement of its Shelbyville investment, Bedingfield said, “This is viewed [as being] greater than another standard business investment.” Instead, he said it’s seen as a “foundational long-term commitment” to its customers, its employees and the planet.
Bedingfield mentions how the U.S. secondary copper refining market has disappeared over the last couple decades. “It’s led to the U.S. needing to export about 50 percent of our scrap, which is equal to roughly 1 million tons,” he says. In addition to exporting nearly half of the copper scrap generated in the country, the U.S. imports 1 million tons of refined copper annually.
“It doesn’t make sense,” Bedingfield adds. “It’s the least sustainable tactic. Now that technology has caught up with today’s environmental regulations and restrictions, we believe it’s time to bring [secondary copper refining] back.”
Serving customers
Bedingfield says Wieland’s recent investments are designed to help its customers close the loop by managing their scrap and supplying them with low-carbon-footprint products.
Wieland is working to establish closed-loop relationships with its customers. “We have increased the amount of customer scrap that we’re taking back,” he says. “We’re looking forward to doing that even more; that’s the most efficient way to do it.
“Between our Granite City facility, formerly Totall Metal Recycling, and our new operation in Shelbyville, we’re going to be able to accept virtually any scrap from our customers, regardless of whether we sold it to them.”
Totall Metal Recycling was formed in 1993 to provide toll processing of scrap wire. It later added purchasing and recycling of copper scrap, electronic scrap, lead, tin, zinc, aluminum, nickel, cobalt, titanium, residues and other recyclables. It processed approximately 100,000 tons of scrap per year when Wieland purchased the company in late April 2022.
At the time, Wieland said Totall Metal Recycling “perfectly integrates” into its North American operations given its location near Wieland’s foundry in East Alton, Illinois, as well as its plant in Shelbyville.
That plant will allow Wieland to supply “100 percent-recycled-content, extremely-low-carbon-footprint” metal with a purity of “99.99 percent and higher” to its customers, Bedingfield says. “This should enable many applications that previously couldn’t prioritize recycled content to begin using this material in their processes and thereby lower their carbon footprint, as well.”

Procuring obsolete scrap
In addition to creating closed loops with its industrial customers, Bedingfield says Wieland has centralized scrap procurement in the U.S. through the recycling group and Vice President of Recycling Procurement Sebastien Perron.
Foundry grades the company traditionally purchases include brass shells and other brass scrap; No. 1 copper, including chops and bare bright; and No. 2 copper.
For Shelbyville, Wieland will purchase scrap with 85 percent copper content or higher, Bedingfield says, including a birch/cliff-type product with copper content ranging from 92 percent to 96 percent to a light copper package to No. 3 copper. “Then we’re looking to expand that mix into things like enameled wire,” he continues. “With Totall Metal Recycling, we’re able to take virtually anything.”
Wieland is targeting early 2024 to start operations in Shelbyville. During the ramp-up phase, the company will be adjusting its assets and processes, Bedingfield says.
“Following that, we’ll start introducing variation into the product mix and get more creative in our mixes to produce the high-purity ingot.”
Wieland has been operating a pilot program to buy and sort small volumes of scrap for Shelbyville. “We’ve been working with some key suppliers that’ll support us during startup, and we’re open to discussions with others interested in supplying the plant,” Bedingfield says. “We’re interested in developing multiple relationships to broaden our options and ensure our suppliers have options, as well.”
“When you think about the applications of this copper for green energy [and] electrification of vehicles, it’s a no-brainer that it should be low-carbon-footprint, high-recycled-content [copper].” – Matt Bedingfield, president of recycling, Wieland North America
Wieland is building traceability into its Shelbyville and Granite City operations.
“We have different scales as we’re shredding and sorting on the front end, so we can understand the recovery,” he says. “We’ll be able to send that information back to our suppliers so they can understand their supply chain and identify potential issues.
“On the back end, we’ll be able to take buttons as it’s coming out of the furnace, so we know the actual chemistry on every single heat. This information will be invaluable to our customers who need to understand the exact chemistry of our product,” Bedingfield adds.
Wieland plans to purchase approximately 100 million pounds of input material to generate roughly 85 million pounds of 100 percent-recycled-content, fire-refined ingot at Shelbyville. The other 15 million pounds of scrap the company sorts out at Shelbyville either will be used at other Wieland facilities or marketed outside the company.
The average carbon footprint per ton of copper cathode produced is 4.1 tons, and Bedingfield notes Wieland will produce 0.97 tons of carbon per ton of ingot made in Shelbyville.
“When you think about the applications of this copper for green energy [and] electrification of vehicles, it’s a no-brainer that it should be low-carbon-footprint, high-recycled-content [copper],” he says. “Otherwise, the story doesn’t hang.”
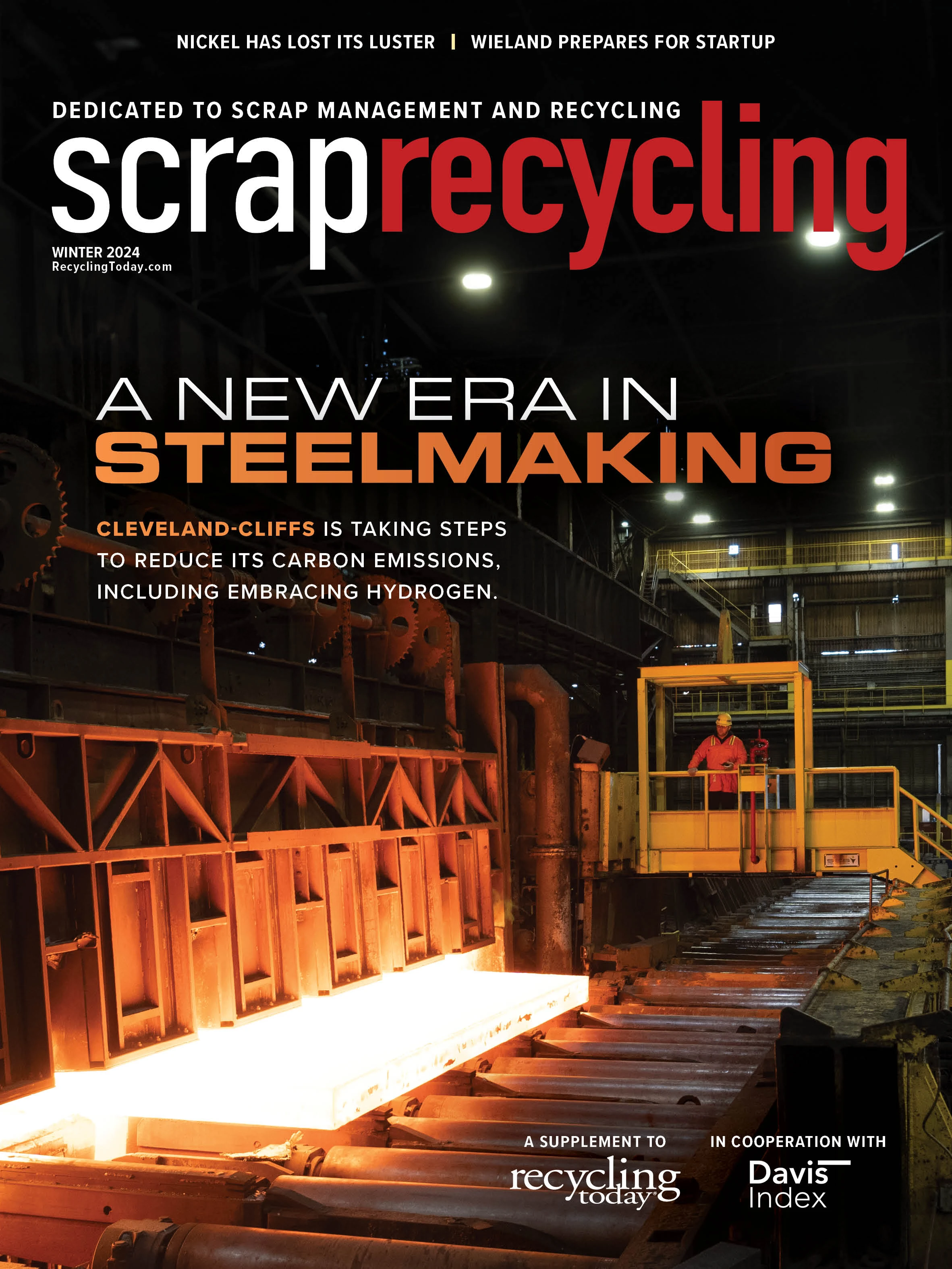
Explore the Winter 2024 Scrap Recycling Issue
Check out more from this issue and find your next story to read.
Latest from Recycling Today
- Aqua Metals secures $1.5M loan, reports operational strides
- AF&PA urges veto of NY bill
- Aluminum Association includes recycling among 2025 policy priorities
- AISI applauds waterways spending bill
- Lux Research questions hydrogen’s transportation role
- Sonoco selling thermoformed, flexible packaging business to Toppan for $1.8B
- ReMA offers Superfund informational reports
- Hyster-Yale commits to US production