The recycling of several types of batteries has created a number of established proccesses.
Tremendous opportunities exist for advanced battery developments and safer and more cost-effective recycling. Government agencies have worked with businesses to ensure that new regulations are met and that technologies that will help to ensure the protection of our environment and health are developed.
Demand for batteries in the U.S. is expected to increase steadily over the next several years. In 1998 more than three billion industrial and household batteries were sold in the U.S. alone. This demand for batteries will continue, spurred on by the ever-growing technological advances in the battery industry and the portability of battery operated equipment.
Battery Solutions Inc., Brighton, Mich., is among the companies playing an active role in the battery recycling process.
Companies that recycle batteries use a variety of techniques and processes to maximize resource recovery safely and profitably.
Lead Acid Battery Recycling
In high-volume, approved operations, the battery is broken apart in a hammer mill, a machine that hammers the battery into pieces. The broken battery pieces go into a vat, where the lead and heavy materials fall to the bottom and the plastic floats. At this point, the polypropylene pieces are scooped away, and the liquids are drawn off, leaving the lead and heavy metals. Each of the materials goes into a different “stream.”
Plastic. The polypropylene pieces are washed, blown dry and sent to a plastic recycler where the pieces are melted together into an almost liquid state. The molten plastic is put through an extruder that produces small plastic pellets of a uniform size. The pellets are sold to a battery manufacturer of battery cases, and the process begins again.
Lead. The lead grids, lead oxide and other lead parts are cleaned and then melted together at smelting furnaces. The molten lead is poured into ingot molds. After a few minutes, the impurities, known as dross, float to the top of the still molten lead in the ingot molds. The dross is scraped away and the ingots are left to cool. When the ingots are cool, they are removed from the molds and sent to battery manufacturers where they are re-melted and used in the production of new lead plates and other parts for new batteries.
Sulfuric Acid. Old battery acid can be handled in two ways. The acid is neutralized with an industrial compound similar to household baking soda. This turns the acid into water. The water is treated, cleaned and tested to be sure it meets clean water standards. Then it is released into the public sewer system.
Another way to treat acid is to process it and convert it to sodium sulfate, an odorless white powder used in laundry detergent, glass and textile manufacturing. This recycles a material that otherwise would have been discarded.
Lead-Acid Recycling Facts |
• The lead battery industry is the nation’s largest user of lead, consuming 80 percent of the lead in this country. • For 10 consecutive years, lead-acid batteries have topped the list of the most highly recycled consumer products with a 96.5 percent recycling rate in 1996. • Every year, the battery industry reclaims 1.7 billion pounds of lead and about 1 billion pounds of plastic and returns both to the battery manufacturing process. • When starting with a 40 pound battery, the material that’s left over after recycling weighs just a few ounces – about as much as a car key. That’s diverting a lot of material out of the waste stream and providing closed loop recycling by delivering the reclaimed lead and plastic back to battery manufacturing – an economic model that works very successfully. |
THE HEAT IS ON NI-CAD BATTERIES
One of the most important changes in nickel-cadmium battery recycling in recent years has been the installation of the cadmium recovery plant at the Inmetco facility in Ellwood City, Pa. The method by which consumer type nickel-cadmium batteries and the industrial nickel-cadmium batteries are processed in this plant involves several steps.
Consumer type nickel-cadmium battery packs are placed in a natural gas fired thermal oxidizer where the plastic is vaporized, leaving clean nickel-cadmium battery cells. Gases from the thermal oxidizer are sent to the plant’s existing rotary hearth furnace where they are completely consumed for heat value. Stack measurements show that no dioxins are released. Also, nickel-hydride batteries are used as a “sweetener” to increase the nickel content in the rotary hearth furnace.
The clean, consumer-type nickel-cadmium battery cells are placed in a cadmium recovery furnace. Cadmium is reduced using carbon, vaporized and condensed, thereby producing cadmium metal. This cadmium is used in the production of nickel-cadmium batteries.
The remaining nickel and iron become feedstocks for the main metal recovery plant. Here the material is used to produce nickel, chromium and iron remelt alloy that is used around the world in the production of stainless steel. (The nickel and iron recovery process will be described later.)
Industrial batteries are recycled somewhat differently. Industrial cells are drained. The potassium hydroxide electrolyte is used as a pH control re-agent in the main facility’s wastewater treatment plant. The cells are dismantled using a large band saw to cut off the tops of the batteries, allowing the nickel and cadmium plates to be separated.
Cadmium plates are placed in a cadmium recovery furnace. Cadmium is reduced using carbon, vaporized and condensed, producing cadmium metal. Along with the cadmium recovered from consumer cells, this cadmium also will be used in the production of nickel-cadmium batteries.
Nickel plates again become feedstock for the main metal recovery plant. They are used to produce nickel, chromium and iron remelt alloy that is used in the production of stainless steel.
Nickel and iron from the cadmium recovery operation joins nickel, chromium and iron by-products coming mainly from stainless steel mills to the main metal recovery plant. These materials, known in the steel industry as electric arc furnace dust, mill scale and swarf, have been mixed with carbon palletized and pre-reduced in a rotary hearth furnace.
All nickel, chromium and iron bearing materials are transferred to an electric arc furnace (EAF). Here the submerged arc furnace performs a smelting operation to produce a nickel, chromium and iron alloy.
In the EAF, lime, silica, alumina and magnesia separate to form a slag/metal bath. Metal and slag are tapped periodically from the furnace. Slag is collected and hauled to a slag cooling area. This co-product is sized and sold for use in building roads, parking lots and commercial driveways.
Molten metal is tapped from the EAF into a refractory-lined ladle. The 15-ton ladle is carried to the twin stand pig caster by an overhead traveling crane where the molten metal is cast into pigs. Metal is poured from the ladle through a central channel that branches out into molds. The molds are water-cooled. After cooling, the pigs are grouped into lots of approximately 20 tons and shipped to stainless steel mills to be used as remelt alloy.
The typical composition of the pig is 12 percent nickel, 14 percent chromium and 68 percent iron. The balance of the pig is essentially manganese, molybdenum and carbon.
The cadmium reclaimed from this new operation is returned to nickel-cadmium battery manufacturers. Nickel and iron become part of the remelt alloy that is used to make stainless steel. Landfill liability is eliminated and natural resources are preserved.
LITHIUM RECOVERY
The cryogenic process described for recovering resources from lithium batteries was invented and is used by Toxco, Anaheim, Calif. In this process, liquid nitrogen is used. The contents of the batteries are exposed using a shredder for large and medium sizes or a high-speed hammer for smaller sizes. Afterwards, they are submerged in a large volume of caustic (basic, not acidic) water. The caustic solution neutralizes the electrolytes. The lithium goes into the solution.
Ferrous and nonferrous metals (aluminum, tin, brass, copper and steel) are recovered. The clean scrap metal then is sold to metal recyclers.
The solution is then filtered. The carbon is recovered and pressed into moist sheets of carbon cake. It has very little fuel value. Some of the carbon is recycled with cobalt, and the remainder is land filled. The paper and plastic components are not recycled. The quantities are too small and of a mixed grade and consequently not useful to users of recycled paper and plastic.
The lithium in solution (lithium hydroxide) is converted to lithium carbonate, a fine white powder. What results is technical grade lithium carbonate. It is sold to several companies including those that make lithium ingot metal and foil for batteries and also provides lithium metal for resale and sulfur dioxide batteries.
The percentage of the batteries that are actually recycled ranges from approximately 65 percent for cell phones, camcorders, watches and hearing aid button cells to 90 percent for military purposes.
This process does not generate hazardous waste material, has no air emission problems and does not use municipal sewers.
The tremendous growth in the rechargeable lithium battery area has stimulated efforts to at least reclaim the most valuable components of lithium ion cells. Many lithium ion cells contain cobalt. Since cobalt is a relatively expensive material compared to the other battery constituents, its recovery is one of the primary objectives in the recycling processes.
Nickel-Cadmium Recycling Facts |
•The Rechargeable Battery Recycling Corporation (RBRC) is a non-profit organization that operates a recycling program called Charge Up to Recycle! For Ni-Cd rechargeable batteries that enlists retail storesand communities nationwide to serve as collection sites for used Ni-Cd batteries. RBRC is committed to conserving natural resources and prevents Ni-Cd batteries from entering the solid waste stream. •It is now estimated that more than 75 million Ni-Cd batteries are sold annually in the U.S. alone. Only one in six households say they recycle rechargeable batteries. This is because most people don’t know that used Ni-Cd batteries, which no longer hold a charge, can and should be recycled. Consequently, there are strong efforts to correct this though RBRC’s international environmental initiatives, such as “Battery CheckDay” and other educational campaigns. |
Besides the cobalt, which is recovered as cobalt carbon cake, iron and other metals are also recycled from the used lithium ion cells. Recovered lithium salts and other lithium products are marketed for use in the lubricant, cement and battery manufacturing industries.
ALKALINE BATTERY RECYCLING
For “Zero Added Mercury” (<.025 percent by weight mercury) battery recycling, the batteries are shredded and given a slight acid bath to neutralize the electrolyte. This material is run through a rotary kiln to dry.
At this point, carbon steel turnings are blended in at a ratio of 20 or more to one part battery material. This blended material is pressed into bricks that are magnetic. This material is transported to a steel mill for processing. In the mill’s furnace, the zinc is fumed off into a vacuum baghouse for recovery.
The zinc recovered from the vacuum baghouse is resold as zinc-oxide. The manganese dioxide becomes an alloy in the production of re-bar steel. Up to now, very few alkaline batteries have been recycled. However, because of the increasing concerns people have about our environment and pollutants, more alkaline batteries are being recycled, and their recycling rate is growing.
The Mercury-Containing Rechargeable Battery Management Act of 1996 prohibits or otherwise conditions the sale of certain types of mercury-containing batteries in the U.S. RT
The authors are officers with Battery Solutions Inc. Chris Sova can be contacted via e-mail at csova@batteryrecycling.com. This article is a modified version of one that originally appeared in Battery Power Products & Technology magazine.
Get curated news on YOUR industry.
Enter your email to receive our newsletters.
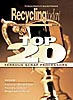
Explore the March 2002 Issue
Check out more from this issue and find your next story to read.
Latest from Recycling Today
- Call2Recycle Canada launches program in Alberta
- The history of SAS Forks: Celebrating 50 years
- SAS Forks partners with NED at Green Recycling in Houston, Texas
- DRKhorse’s RCC series at Gorick Construction in Endicott, New York
- Balar Equipment to operate under Enviro-Clean Equipment name
- Li-Cycle reports 2024 financials
- Wisconsin Aluminum Foundry acquires Anderson Global
- PureCycle, Landbell Group working to advance PP recycling in Europe