1. What is SWEED’s solution for processors looking to break into wire chopping and nonferrous recovery?

Sweed Machinery
Recycling System
Sales Representative
Although SWEED is recognized for providing customized solutions, we now offer our S2000 Series of wire chopping lines. This standard system efficiently handles up to 2,000 pounds per hour and is designed with flexibility for future expansion. This is a great option if you are entering the wire chopping business or considering an upgrade from simpler systems. SWEED has strategically stocked parts and components for the S2000, ensuring swift builds and shipping, which allows processors to get up and running as quickly as possible.
2. How do you recommend handling materials containing brass connectors and plug ends?
Handling materials like harness wire and power cables, which often contain brass connectors and plug ends—think harness wire, computer charging cables or extension cords—we recommend incorporating a screening process after the primary separation. This involves sizing the finished copper to isolate larger brass pieces. Unlike wire, brass connectors and pins maintain a consistent size throughout the process. Using screening is a smart, cost-effective method to eliminate contamination, ensuring a purer and more refined end product.
3. What is the best approach for handling stainless steel that cannot be removed using a conventional magnet?
SWEED can provide a stainless steel separator that uses a special high-gauss magnetic drum designed specifically for stainless steel removal. Depending on the stainless steel percentage, the separator can be integrated into the process before the granulator or after primary copper separation. A vibratory feeder or other metering device can be used to ensure proper material presentation and the greatest separation efficiency.
4. How should wires or cables that are on reels or spools be processed?
The approach depends on the size of the spools. Smaller plastic spools can be placed directly into the prechopper or preshredder; the plastic spool material will be removed with the insulator. Larger steel or wooden spools are best handled with our 5703 XHD Scrap Chopper. This specialized linear chopper automatically despools cables, reducing the cable length depending on the cutter configuration. This is a great option for those processing overhead power cables, underground distribution cables and telecommunication cables. Many of these cables incorporate an aluminum component that can be recovered after the primary copper separation process.
5. What other considerations should be taken into account when designing a wire chopping line?
Designing a wire chopping line requires a thoughtful approach. As a manufacturer, we know the significance of completely understanding the unique materials and operational challenges our customers face. This is where SWEED excels, tailoring the equipment package to align with your specific application requirements. Even subtle adjustments, such as a strategically placed metering device, can enhance a system’s performance; an extra 500 pounds per hour of system capacity can have a significant financial impact. Equally essential is postsale support, and SWEED is committed to guiding you through operational considerations, ensuring not only a successful launch but also sustained profitability. With SWEED as your trusted partner, you not only acquire cutting-edge recycling equipment but also secure ongoing support for continued success.
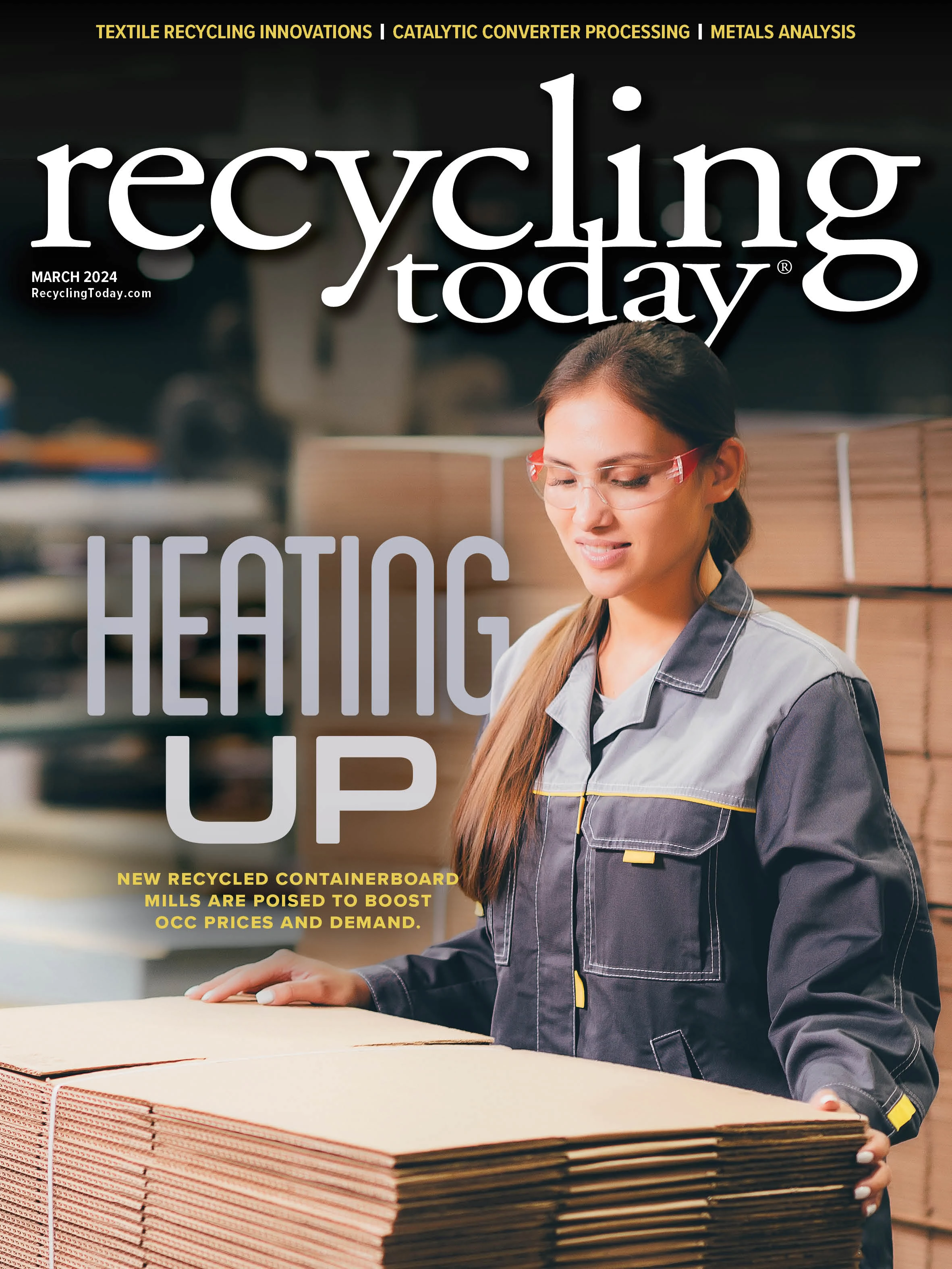
Explore the March 2024 Issue
Check out more from this issue and find your next story to read.
Latest from Recycling Today
- Aqua Metals secures $1.5M loan, reports operational strides
- AF&PA urges veto of NY bill
- Aluminum Association includes recycling among 2025 policy priorities
- AISI applauds waterways spending bill
- Lux Research questions hydrogen’s transportation role
- Sonoco selling thermoformed, flexible packaging business to Toppan for $1.8B
- ReMA offers Superfund informational reports
- Hyster-Yale commits to US production