_fmt.png)
1. What makes buying an undermill oscillator (UMO) different from other capital equipment?
It’s like the old joke about mushrooms: Keep them in the dark and feed them %#^$. UMOs are no different. They’re buried underneath extremely powerful shredders and take a beating. They must be built to withstand explosions, impacts and a constant stream of harsh, metal product. If you are not vigilant, you risk purchasing an inferior unit that doesn’t have the ability to last.
2. How do you design a UMO tough enough?
Experience makes the difference when designing for unknown upset conditions. We’ve perfected our SYNCRO-SHEAR™ design, which utilizes rubber toroids along the length of the unit. This design builds stability across the width and guards against impacts that can rock traditional units. As we know, side motion on a vibrating conveyor will negatively impact a UMO’s performance over time. Having integral lateral stability in the design is critical in preventing unplanned downtime. And it doesn’t stop there. We reinforce the entire substructure from top to bottom, upgrading the strength of all moving components and reinforcing the high impact areas of the trough.
3. You mention unplanned downtime; how maintenance friendly are these units?

Extremely. Over the years we’ve simplified access to our SYNCRO-COIL™ spring drive design. Talk to anyone in maintenance and the most requested design detail is ease of access. We locate our drive assembly at the rear of the unit. The drive system is mounted up high and completely accessible for maintenance … no crawling under the trough and over scrap. Furthermore, the drive springs absorb the shock caused by impacts on the trough to spare the bearings constant abuse. This style of drive is not used on other UMOs.
4. Do troughs require frequent replacement?
They are a wear item. That said, they don’t get replaced as often as one might think. We start out with 3/4-inch-to-1-inch thick abrasion-resistant steel along the bottom pan and 3/8-inch thick steel on the sides. This then gets reinforced with stiffeners vertically and across the width to provide a very rigid assembly designed to withstand the constant abuse seen in this environment. Given all that, I’d say they hold up very well.
5. Beyond structural design, what other criteria do you prioritize?
Performance is a priority. If material isn’t moving, then our customers are not meeting their production or financial goals. We track the stroke of both our own units and those of competitors. On average, our machines have a 3/4-inch or greater stroke. The higher stroke allows material to flow better and keep up with demand.
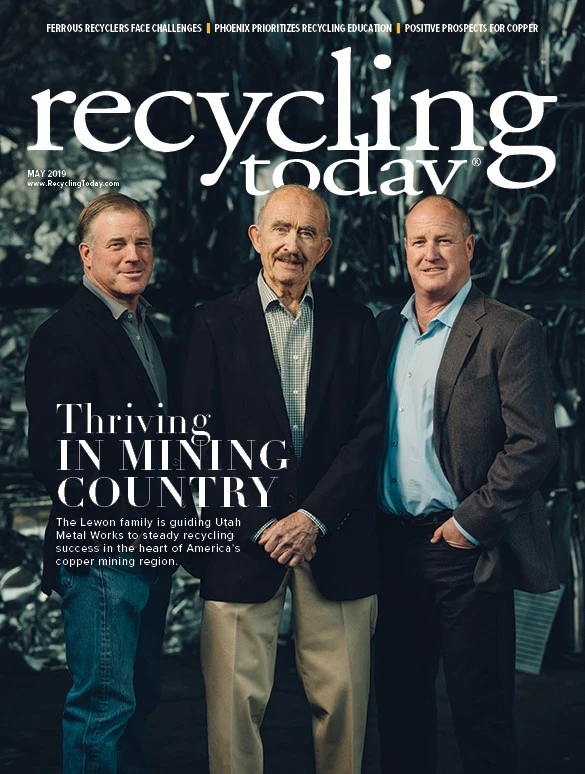
Explore the May 2019 Issue
Check out more from this issue and find your next story to read.
Latest from Recycling Today
- Haber raises $44M to expand to North America
- Canada Plastics Pact releases 2023-24 Impact Report
- Reconomy brands receive platinum ratings from EcoVadis
- Sortera Technologies ‘owning and operating’ aluminum sorting solutions
- IDTechEx sees electric-powered construction equipment growth
- Global steel output recedes in November
- Fitch Ratings sees reasons for steel optimism in 2025
- P+PB adds new board members