1. Which application trends have been growing in demand this decade for primary shredders and why?
We have seen gaining momentum and demand for primary shredders in North America for waste-to-energy, composting, wood waste, natural disaster cleanup and construction and demolition applications. The general need for volume reduction of materials previously thought to be too tough or bulky for existing technology also has increased.
With mobile primary shredders, you have the ability to bring the reduction equipment to the waste stream, which typically reduces hauling costs by as much 10:1. Shredding these bulky materials on-site also greatly reduces material handling costs.

2. How can primary shredders benefit companies with multiple application shredding needs?
Sites such as transfer stations can benefit immensely from using this machine for batch processing as it can shred wood one moment, then move on to white goods, mattresses, solid waste and more.
The HAAS TYRON transportable shredder has the ability to process materials ranging from green waste to baled aluminum extrusions to mixed streams, such as construction debris, and more. By simply adjusting the settings on the machine, we can vary shred size, throughput and even capability in terms of capturing and shredding difficult material.
3. What advantages can transportable hydraulic shredders offer in terms of durability and output?
The HAAS TYRON has been designed to operate 24/7 in all weather conditions, ranging from extreme heat to frigid climates. The machines are equipped with proven Scania industrial engines, top-of-the-line closed loop hydraulic systems and an easy-to-use operator interface.
Throughput rates can be optimized and even controlled by simple program changes to match downstream equipment requirements.

4. What features should waste processors look for in a primary shredder?
Choosing a shredder with an independent shaft control will provide you with the most versatility when processing varying material streams. HAAS TYRON shredders have the ability to run either shaft in forward or reverse, together or separately, and at different rates per minute for varying lengths of time. The main advantage of this feature is that tough materials can be broken down with a random shredding action from the back-and-forth shaft motion (always reorienting material in the cutting chamber), so soft pliable materials such as plastics and wire will not wrap the shafts.
5. What are the maintenance considerations for owners of these shredders?
Ideally, choose a shredder with cutting tools that can be maintained and rebuilt on-site. The HAAS TYRON’s cutting chamber is a unique design of welded, hard-faced tools, combs and breaker bars that can be easily touched up or repaired back to their original state when worn. With regular service, these chambers will last for years, maintaining their original reduction performance. There are no tips to replace, break off, wear or seize in their holders and no chamber screens to wear or jam.
Shredders without internal chamber screens typically have the highest throughput with the least chance of damage from materials that cannot be shredded.
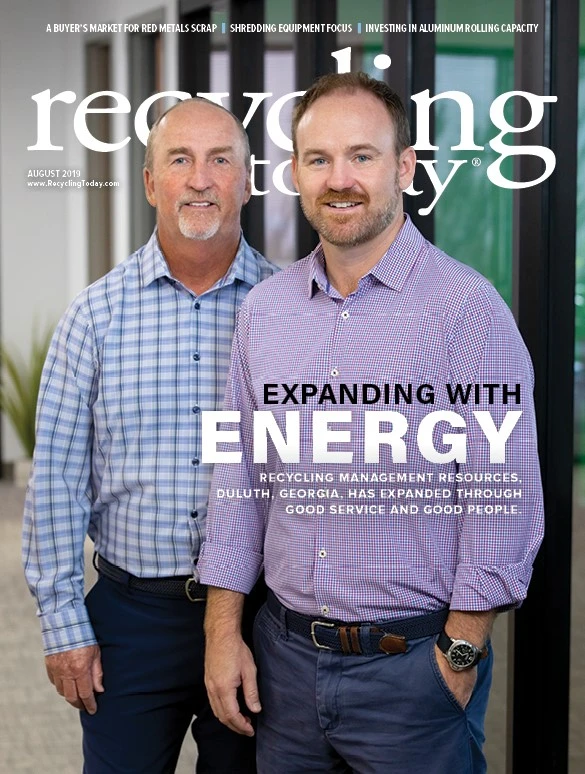
Explore the August 2019 Issue
Check out more from this issue and find your next story to read.
Latest from Recycling Today
- Nucor receives West Virginia funding assist
- Ferrous market ends 2024 in familiar rut
- Aqua Metals secures $1.5M loan, reports operational strides
- AF&PA urges veto of NY bill
- Aluminum Association includes recycling among 2025 policy priorities
- AISI applauds waterways spending bill
- Lux Research questions hydrogen’s transportation role
- Sonoco selling thermoformed, flexible packaging business to Toppan for $1.8B