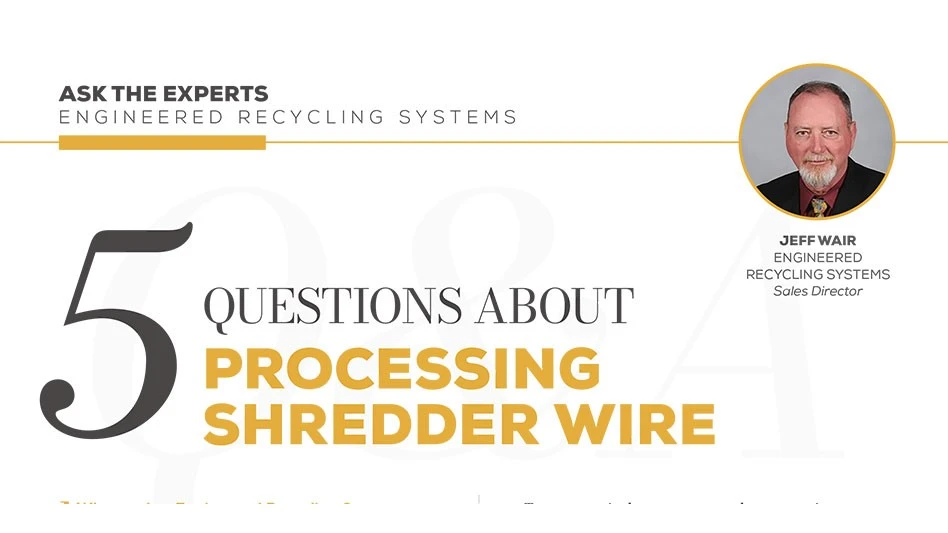

1. What makes Engineered Recycling Systems stand out when consumers are looking to process shredder wire?
Our first ASR system was installed over a decade ago, giving ERS equipment thousands of operational hours processing shredder wire. Listening to our clients through the years as well as continuing to improve and refine our processes have helped set ERS apart and enabled us to provide the best shredder wire system in the industry. We have shredder wire systems throughout North America, from coast to coast, including in some of the largest scrap processors in the world.
2. What are some of the benefits of processing shredder wire?
In the past, scrap metal recyclers that produced shredder wire would bale it and sell it to China. The Green Fence changed that for many processors, requiring a recycler to change sensor sorter settings to achieve a product that contains at least 80 percent insulated copper wire (ICW). Recyclers soon found out that to achieve this level of product quality meant they were leaving a tremendous amount of copper units in the waste stream. By processing shredder wire in an ERS system, you can run the sensor sorters less aggressively or ”dirty” to recover as many copper units as possible. The ERS system can take this “dirty” product from sensor sorters and produce clean base metal products that can be sold domestically as well as into the export market. Many recyclers find that they have much more control and leverage when they are able to produce a product that is easily saleable in domestic markets.
3. What are some of the pitfalls of processing shredder wire?
Shredder wire is full of contaminants that can cause catastrophic damage to traditional ICW chop lines. All it takes is a stainless-steel bolt less than the size of an AA battery to ruin a set of granulator blades or to break a rotor.
Temperature is always a concern when processing shredder wire. The low melting temperature of the plastic material can cause nonstop headaches that lead to too much downtime.
These systems require knowledgeable operators and a well-equipped maintenance department to ensure the system is firing on all cylinders. With copper that tends to hide in fine stranded wire, most systems will lose between 5 percent and 15 percent of the copper units that ERS systems are able to recover.
4. What differentiates ERS’ systems from the competition’s?
We do not use granulators in our system. We use a series of balling mills, magnets, air classification and density tables to separate all metal units from the waste. Our system produces a fine 99 percent No. 2 copper, a copper-rich red metals package (98 percent copper), aluminum, stainless steel and steel, all of which can be sold domestically.
ERS is not only known for designing innovative equipment; our customer service department also reflects the same level of excellence. Considering all the supply chain issues caused by the pandemic, we have taken measures to get ahead of potential shipping delays. We have invested in a 55,000-square-foot warehouse and filled it with equipment and parts inventory. All our most important spare parts are available for expedited shipping from Atlanta.
5. Besides shredder wire systems, what else does ERS specialize in?
ERS also engineers chop lines for No. 1 and No. 2 insulated copper wire, aluminum-copper radiators, ACSR (aluminum cable-steel reinforced) as well as e-scrap. Additionally, we have a division that specializes in dust collection for several different industries. Please check out our CCM OCT Filter systems on our website, www.engineeredrecycling.com.

Explore the December 2022 Issue
Check out more from this issue and find your next story to read.
Latest from Recycling Today
- Aqua Metals secures $1.5M loan, reports operational strides
- AF&PA urges veto of NY bill
- Aluminum Association includes recycling among 2025 policy priorities
- AISI applauds waterways spending bill
- Lux Research questions hydrogen’s transportation role
- Sonoco selling thermoformed, flexible packaging business to Toppan for $1.8B
- ReMA offers Superfund informational reports
- Hyster-Yale commits to US production