1. How can modern technology and automation be leveraged to enhance maintenance practices and predict potential failures before they occur?

Machinex
Startup Coordinator
Easy access to maintenance areas is the first consideration and paramount to enhance maintenance practices.
Modern automation often includes supervisory control and data acquisition (SCADA) systems. These controls provide historic trending and data that can help forecast component replacement through preventive maintenance (PM) prior to failure. Speaking of PM, investing in periodic PM visits from the system manufacturer can be very valuable.
2. Can you explain the significance of proactive maintenance over reactive maintenance?
Proactive maintenance is crucial in MRFs because it helps prevent downtime, which directly translates to financial losses. Implementing daily, weekly and monthly PM protocols ensures equipment remains in optimal condition, reducing the likelihood of unexpected breakdowns.
On the other hand, reactive maintenance is often a temporary solution that addresses problems after they arise. These “band-aid” fixes are not intended to be permanent and can lead to repeated issues, increased wear and tear on machinery and higher long-term costs.
By prioritizing proactive maintenance, MRF operators can ensure smoother operations, extend the lifespan of their equipment and maintain consistent productivity.
3. How can MRF operators optimize their workforce to enhance efficiency and productivity?
One effective strategy for optimizing the workforce in MRF operations is to reduce labor in areas that are becoming more automated or less critical and redirect those resources to areas that need more attention. This not only helps in managing labor costs but also ensures that the most critical areas of the operation are adequately staffed.
Additionally, having employees who have grown with the company and understand the evolving changes in the industry is invaluable. These experienced workers can provide insights and contribute to smoother transitions during periods of change.
4. What common practices can MRFs adopt to improve operations and achieve more success?
A common denominator that MRFs can work on is engaging and empowering their workforce. What sets the most successful facilities apart is the passion and commitment of their operators. By involving employees in the decision-making process and giving them a sense of ownership, MRFs can foster a motivated and proactive workforce.
Encouraging operators to take part in the process and providing them with the authority to make decisions not only boosts morale but also leverages their on-the-ground insights and expertise. This participatory approach can lead to more innovative solutions and improved operational efficiency.
5. How can modern MRF designs enhance the flexibility and efficiency of commodity recovery, and what considerations should be made when implementing these designs?
Modern MRF designs offer significant flexibility in producing more and higher-quality commodities. For example, increasing the recovery of small OCC (old, corrugated containers) can dramatically reduce its presence in mixed paper, thereby improving the quality of both materials in certain market conditions. Additionally, PET (polyethylene terephthalate) can be separated by color or packaging type, though it’s important to evaluate whether the benefits outweigh the costs (the delta).
Modern MRF systems designed with adequate bunker storage can handle an increased number and variety of commodities. Keeping options open for recovering more types of materials is a prudent consideration. This flexibility not only ensures the facility can adapt to changing market demands but also maximizes material recovery.
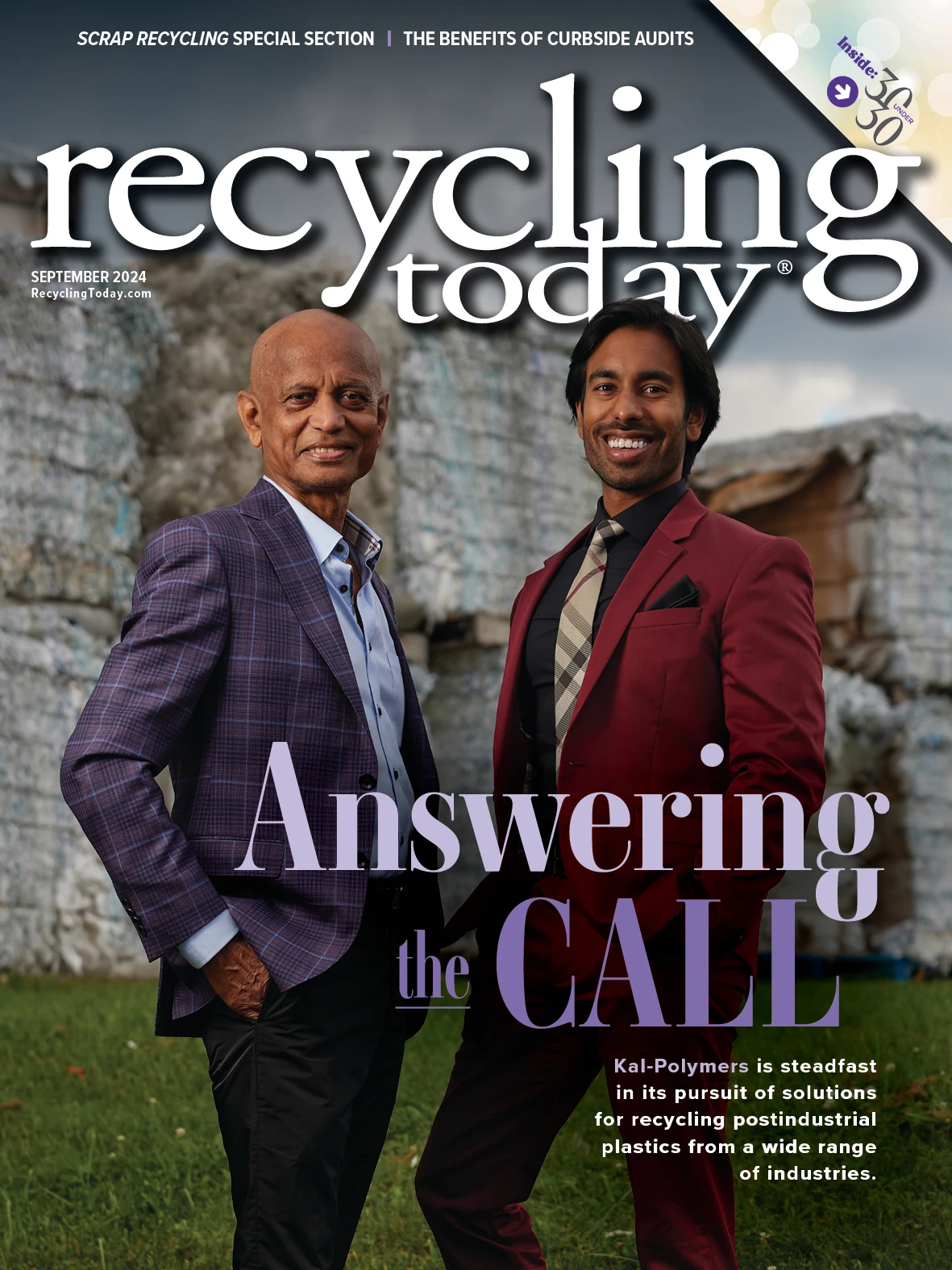
Explore the September 2024 Issue
Check out more from this issue and find your next story to read.
Latest from Recycling Today
- Call2Recycle Canada launches program in Alberta
- The history of SAS Forks: Celebrating 50 years
- SAS Forks partners with NED at Green Recycling in Houston, Texas
- DRKhorse’s RCC series at Gorick Construction in Endicott, New York
- Balar Equipment to operate under Enviro-Clean Equipment name
- Li-Cycle reports 2024 financials
- Wisconsin Aluminum Foundry acquires Anderson Global
- PureCycle, Landbell Group working to advance PP recycling in Europe