1. Why is mobile shear maintenance so critical to performance and longevity?

Loren LaGesse
Genesis Attachments
Technical Trainer
Owning a mobile shear is a hands-on operation that should be managed with a proactive routine. Good operating and maintenance practices go hand in hand and will help keep the shear operating as intended. Balancing production figures, maximizing run time and controlling operating costs are all important factors in keeping the shear profitable. Skipping daily tasks might save you up front but often will cost you in the long term.
2. How do you recommend getting in a good maintenance routine, understanding the daily tasks as well as the long-term maintenance items?
Simply read the manual! Mobile shears are an integral part of many demolition and scrap operations and should be treated as such. Shear and excavator packages can cost hundreds of thousands of dollars or more, and there’s an excellent chance the equipment manual will cover topics you weren’t even aware existed. Whether it be related to the shear or the carrier, almost anyone could benefit from improved familiarity with the product manuals and the information they contain.
3. What is the ideal maintenance interval for a mobile shear?
It’s easy to let the daily task intervals get extended, especially when the tool is new and operating at tip-top performance. Regardless of age, daily attention is required, starting with 4-hour grease intervals and extending into daily blade and pivot group inspections. Later, long-term care items, such as hydraulic resealing or even major overhauls, will come due. Approaching these items at a daily level will require some understanding of the forces at play and a desire to keep the tool running at top performance. Having personnel who are onboard with tackling these items proactively will have a significant, positive impact on staving off unscheduled repairs and associated downtime.
4. Who is responsible for the single easiest and cheapest preventive care item that is often overlooked or doesn’t get performed correctly?
This typically falls on the operator, but in some yards, it could be a lube technician. Proper grease intervals are ultra important because mobile shears have a wide range of motion while also creating immense force. They also use bushed load surfaces rather than roller type bearings, meaning grease film strength is the sole element responsible for withstanding that pressure.
Just as important as the interval is using the right type of grease. Our recommended grease intervals are 4 and 8 hours, and we recommend extreme pressure lithium (No. 2) grease. Using cheap lubricants or base compounds containing moly doesn’t get the job done.
5. What shear maintenance practices often are lacking?
Watching an operator cut hardened material is always excruciating given the violent pressure spikes and toll it takes on a mobile shear, but from a maintenance perspective, it’s blade neglect. Shears use steel to cut steel. Neglecting blade maintenance makes everything else on the shear work harder. It slows processing time, increases cutting stresses and increases the likelihood of material jamming in the jaw, among other things. Blade gaps, bolt torque and edge radius maintenance aren’t the most glamorous aspects of equipment care, but, in the shearing world, these are the details that matter. It can seem a bit tedious, but a head-on approach to blade care day to day will keep the shear performing far better for far longer.
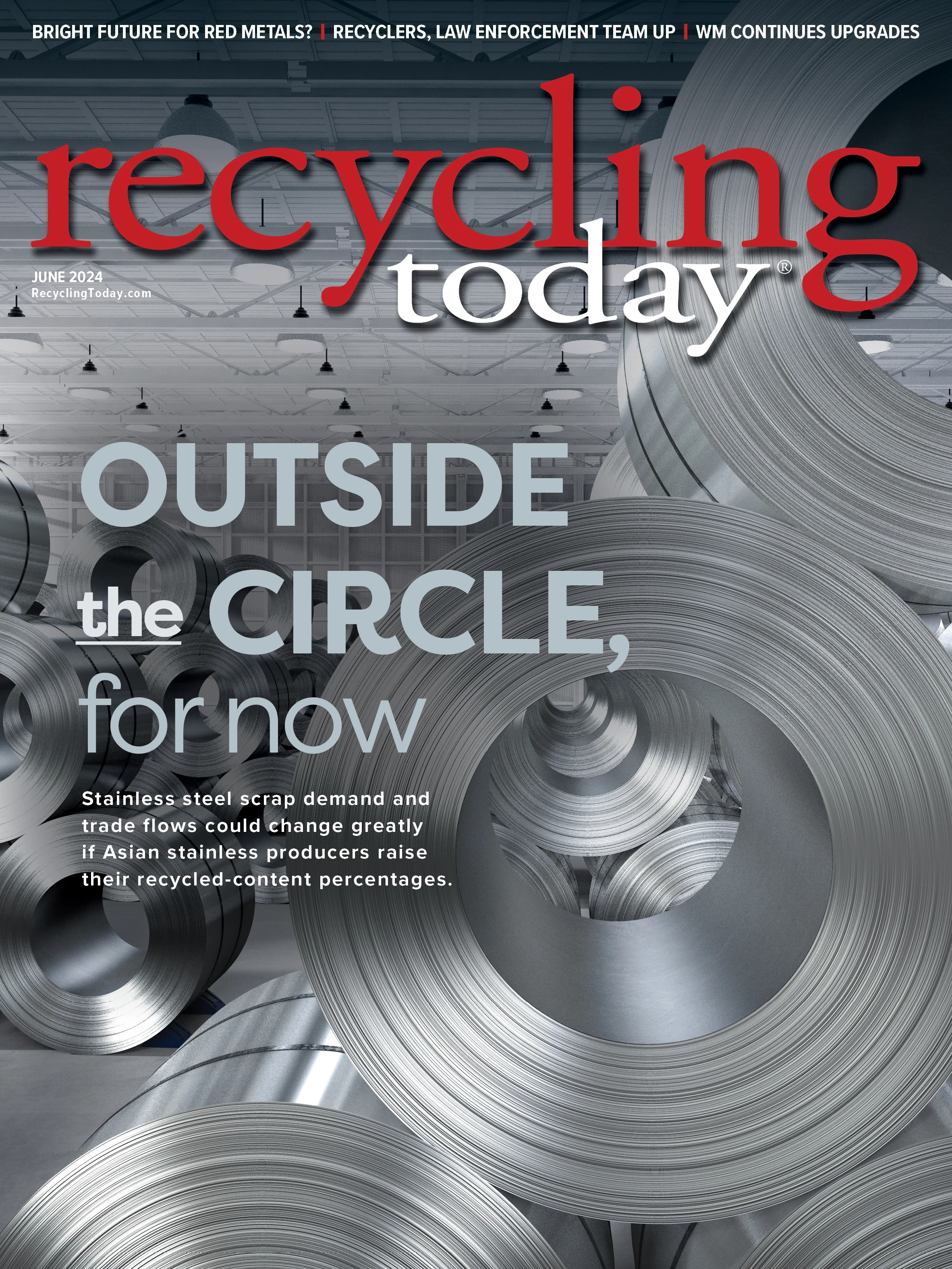
Explore the June 2024 Issue
Check out more from this issue and find your next story to read.
Latest from Recycling Today
- CATL, Ellen MacArthur Foundation establish battery partnership
- Greif announces price hike for all grades of URB products
- Ascend Elements appoints new president, CEO
- Culligan International to provide aluminum water bottles at Chicago running events
- Returpack reports increased DRS activity in Sweden
- Trade groups align against European export restrictions
- Construction, auto sectors show mixed signals
- Politics in Turkey threaten recycled steel outlet