
Van Dijk
Van Dyk
Recycling Solutions
Sales & Special Projects
1. Why should I invest in a food depackaging system?
Depackagers take packaged food waste and liberate the organics, creating a purified organic slurry, and press the discarded packaging fraction for maximum recovery of organics. A robust depackager achieves capacity in excess of 18 to 20 tons per hour (tph), higher recovery of organic material with increased purity, faster unloading times and helps you comply with state mandates (like California’s S.B. 1383) for organic recovery and diversion from landfill. Accepted materials include preconsumer packaged food waste, preconsumer mixed source-separated organics (SSO), postconsumer food waste, supermarket and restaurant waste, frozen foods, beverage cartons and bottles and canned food and beverages. With a depacking system, you won’t have to turn away organic tonnage in packaging!
2. What are the different kinds of food depackagers?
Manufacturers use either a horizontal design or a vertical design. A vertical design allows gravity to feed the unit via a feedhopper, creating a compact and inexpensive feed system. Horizontal designs use feed systems requiring slightly more space. An inground feed hopper system blends and stores a variety of bulk materials, which are then conveyed to the depackager. Horizontal depackagers are more suited to high-capacity operations receiving bulk items and are easily fed by a loader or by collection trucks dumping directly into the bunker.

3. What are the advantages of the horizontal depackager?
As mandates for organics recycling become widespread, contamination in SSO material will increase. This is problematic for vertical depackagers as heavy nonorganic contaminants are not easily ejected vertically. Capacity and screening surface are limited, resulting in losing more organics to residue. Horizontal depackagers easily eject heavy contamination, and a gentler hammermill design can be used that features flexible hammers spinning at a much lower rpm. A large, rotating 360-degree screen results in higher throughput with limited downtime, a minimal amount of organics lost to residue and very few microplastics in the organics.
4. Do I need a shredder or presort station prior to my depackager?
Depending on your inbound SSO contamination rates, mechanically removing oversized residue/film prior to the depackager can be beneficial. The SMICON depackager system does not require presorting and is able to handle the wide array of nonorganic residue typically seen in SSO material. Basic floor sorting using a material handler or loader is sufficient, and problematic items can be identified on the tipping floor to be crushed or removed before entering the depackager.
5. What are the end markets for this material?
The organic slurry, or ‘cake’ (depending on moisture levels), can be sold to composting, sewage treatment, animal feed operations or anaerobic digestion companies for recycling or waste-to-energy applications. Each end market will have different purity and moisture requirements. Contact Van Dyk for more information.
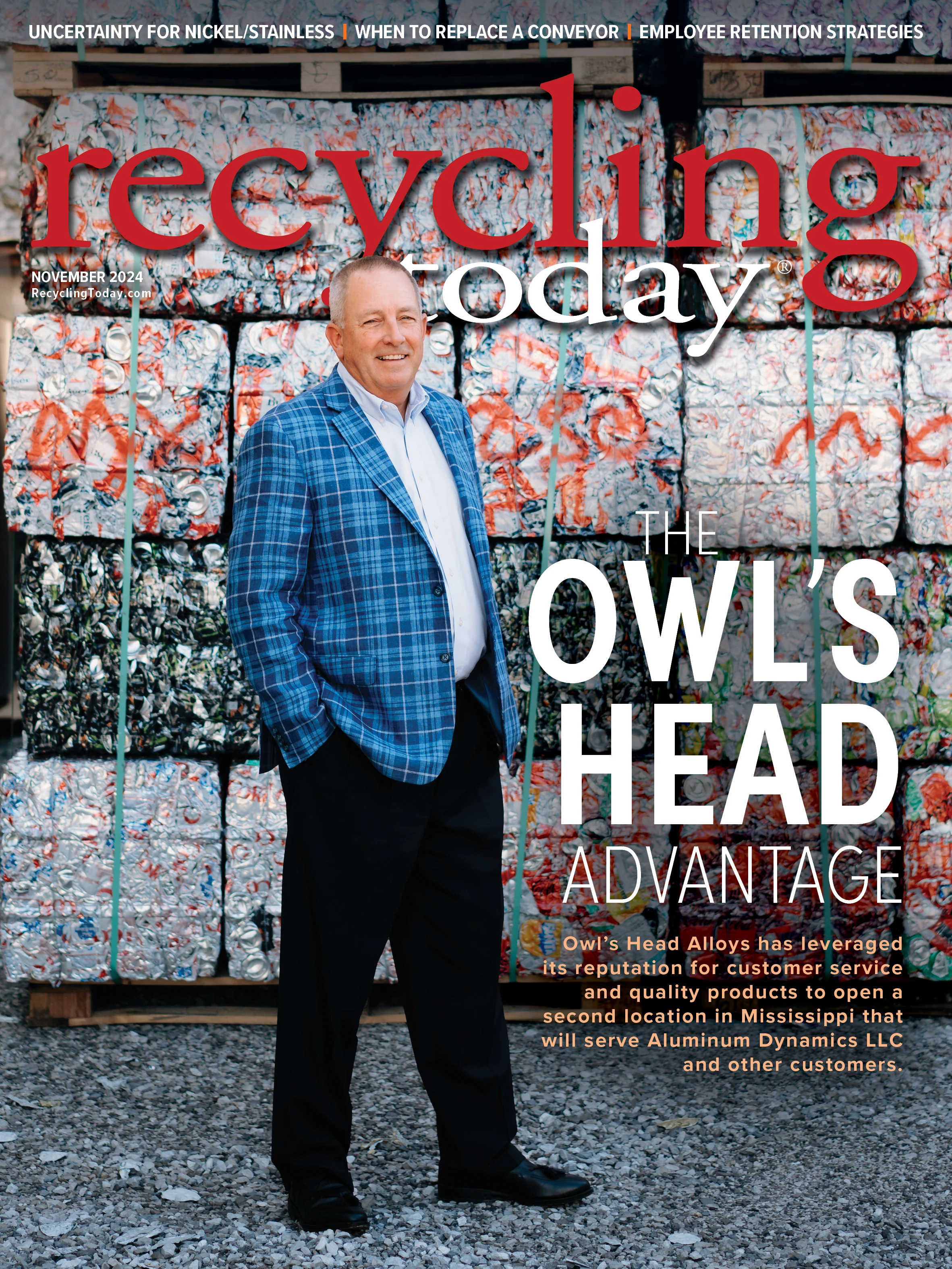
Explore the November 2024 Issue
Check out more from this issue and find your next story to read.