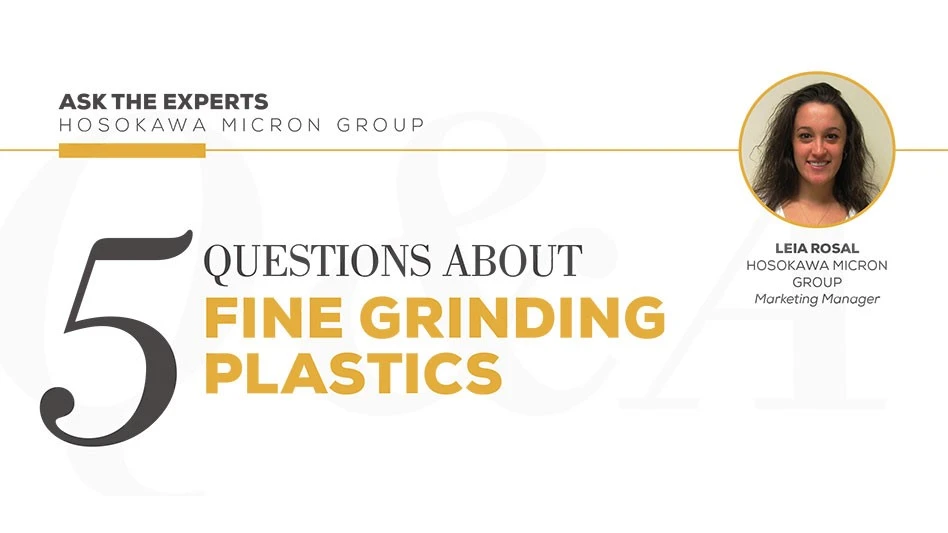

1. What limitations does the plastics industry face when it comes to size reduction and fine grinding polymers?

Marketing Manager
Manufacturing polymer products is increasingly becoming a challenge since the trend is moving towards finer products to benefit many applications. Currently, the size reduction of polymers is limited by several constraints including heat generation and the ability to control particle top size. The current size-reduction systems include impact or attrition mills followed by screening decks to control particle top size. These classification devices are limited by the screen size that will allow significant throughput without blinding. Typically, screening is done at 50 to 60 mesh and the very top end particle size that can be efficiently screened is approximately 80 mesh, or 180 micrometers. Heat-sensitive polymers also can be processed using liquid nitrogen for cooling the product.
2. Does liquid nitrogen need to be used when grinding soft, heat-sensitive materials?
No. The Hosokawa Mikro® V-UMP Mill is a vertical shaft, high-speed, cutting mill designed for the fine size reduction of plastics, polymers and fibrous materials that do not respond well to other forms of impact milling. This unique mill design that allows for interchangeable rotor configurations depending on the fineness required and developed to grind heat-sensitive and soft materials without liquid nitrogen or conditioned air.
3. What type of system configuration allows for size reduction of polymers and plastics?
Hosokawa has designed and installed a new system in our testing facility specifically for the size reduction of heat-sensitive polymeric materials. This fine grinding system configuration incorporates ultramodern milling and classification equipment and controls allowing for the grinding and classification of a wide range of materials in both fine and coarse applications. The system can run under cryogenic or ambient conditions which adds to its flexibility and can be used with a counter-rotating pin mill or attrition type mill depending on the final particle size requirements. An integrated air classification system will improve material capacity, efficiency and cut point for finer applications where mechanical screening is not practical.
4. What type of applications would benefit from a cryogenic fine grinding system configuration?
This system configuration allows for a cryogenic cooling screw conveyor to be used. It is designed for heat-sensitive applications, which will allow liquid nitrogen to be used with the feed. This makes the feed brittle and easier to grind into a powder and perfect for applications like 3D printing, medical device manufacturing and many of the engineered resins that are now used throughout the industry for specialty applications.
5. Can my existing components be incorporated into a fine grinding system?
Absolutely. System integrations are an effective way to maximize the use of existing equipment with life left in it. With an in-house team of engineers, Hosokawa Micron Group system designs are completely customizable for individual applications or special installations.

Explore the July 2022 Issue
Check out more from this issue and find your next story to read.
Latest from Recycling Today
- Radius to be acquired by Toyota subsidiary
- Algoma EAF to start in April
- Erema sees strong demand for high-volume PET systems
- Eastman Tritan product used in cosmetics packaging
- Canada initiates WTO dispute complaint regarding US steel, aluminum duties
- Indianapolis awards solid waste contract, updates recycling drop-off program
- Novelis produces first aluminum coil made fully from recycled end-of-life automotive scrap
- GPR’s hubbIT platform recognized in Georgia State University’s Marketing Awards for Excellence in Innovation