
Workplace hazards are abundant in scrap yards and at other scrap processing facilities. The field of industrial hygiene is centered on keeping workers safe by controlling workplace health hazards.
Because of limited time and resources, companies could be inclined to jump right into industrial hygiene assessments. However, it’s important to understand all aspects of industrial hygiene before making those assessments.
Industrial hygiene has five main principles: anticipate hazards, recognize hazards, evaluate hazards, evaluate results and control hazards.
Anticipate hazards
Anticipating workplace health hazards is the first step in keeping employees safe.
Safety data sheets (SDS), documents that list the properties of each chemical an employee could come into contact with, will help identify potential hazards. The U.S. Occupational Safety and Health Administration (OSHA) says, “Employers should also ensure that they receive their scrap supply from reliable sources that follow the established guidelines and should obtain [SDS] and labels for the scrap materials where available.”
During this phase, any potential exposure issues related to the work environment also should be identified. For instance, employees could have greater exposure if they work in areas where ventilation is limited or if a process generates a great deal of dust.
While OSHA’s most recent data on scrap metal workers is from 2001 (because of industry code changes), the agency says that in the nonferrous recycling industry “the most common causes of illness were poisoning (e.g., from lead or cadmium), disorders associated with repeated trauma, skin diseases or disorders and respiratory conditions due to inhalation of, or other contact with, toxic agents.”
Companies should identify the OSHA-regulated materials at a facility and their associated occupational exposure limits.
Other hazards that could be present at scrap processing facilities include noise, fumes and dust from torch cutting, volatile organic compounds or ammonia, acids or carbon monoxide.
Recognize hazards
By understanding processes, potential chemical and physical hazards at a facility can be uncovered. Employees should be asked how they complete their work, and the plant’s layout should be considered because adjacent activities could affect employee exposures.
Evaluate hazards
After anticipating and recognizing hazards, it’s time to evaluate them through an industrial hygiene assessment. This is the most extensive part of the process because it determines the who, what, where, when and how of monitoring:
- Who – It’s common to monitor the highest and lowest exposed employees. Industrial hygienists also generally group workers with the same general exposure profile for an agent into a similar exposure group (SEG). Workers in an SEG perform the same task at the same frequency, use similar materials in a similar process and perform the work similarly.
- What – Consider physical, biological and chemical agents.
- Where – Monitoring should take place in certain areas of the facility where exposure is suspected based on previous observations and process information.
- When – Exposures can vary between shifts. Companies should measure during routine work and random and nonrandom tasks and might want to consider measuring during other events, such as facility maintenance shutdowns.
- How – If potential hazards at a facility are airborne, the air must be sampled. Biological monitoring will be necessary for facility other hazards, such as lead.
Some companies have environmental, health and safety professionals qualified to conduct monitoring; but, if a company does not, the American Board of Industrial Hygiene recommends working with a certified industrial hygienist (CIH).
Companies should never collect a sample without knowing what they will do with the results if they indicate exposure risks.
Airborne hazards can be detected using active or passive sampling methods. With active monitoring, a worker wears a pump that collects air pulled through a filter. With passive sampling, the air passes over a monitoring device called a badge, also worn by a worker. Active sampling generally is preferred by industrial hygienists; however, passive sampling is a good alternative if the population or area to monitor is very large or if cost constraints are an issue.
Active sampling methods are varied:
- direct reading instruments, which have a sensor to instantaneously measure gases, vapors, aerosols and fine particles in the air;
- integrated sampling using a pump to pull air into a filter or sorbent tube sample, which is sent to a lab for analysis; and
- grab samples, air captured in an empty bag or canister and sent to a lab for analysis.
“How” also applies to the number of samples that are needed for adequate analysis. Typically, six or seven samples are considered a good number from which to build an exposure profile.
Evaluate results
Industrial hygienists use qualitative and quantitative analysis to determine if the exposure results are acceptable, unacceptable or uncertain. When evaluating results, it’s important to know the hazard’s occupational exposure limit, which varies based on the regulating body (e.g., OSHA or American Conference of Governmental Industrial Hygienists). Limits are different, including a time-weighted average that measures the average exposure over an eight-hour workday, and short-term exposure, which is typically a 15-minute time-weighted average exposure. Ceiling limits—the concentration that should not be exceeded during any part of the working exposure—also exist.
Certified industrial hygienists can assist with determining if results are acceptable or uncertain.
Control hazards
When exposures are deemed unacceptable, it’s time to implement controls. Many employers rush to require personal protective equipment (PPE, such as respirators), when, in theory, the hierarchy of controls offers many alternatives. Removing or replacing the hazard, isolating workers from the hazard or changing the way workers do their tasks should all be considered before protecting workers from exposure with PPE.
Final confirmation
Now it’s time to verify employees are safe using program management, continuing education and reassessment. Companies also should consider re-evaluating employee exposures whenever they make changes to the facility layout or equipment, work practices or materials that could affect exposures.
While industrial hygiene assessments have many steps, it’s critical to follow each step to ensure the well-being of a company’s best assets.
Get curated news on YOUR industry.
Enter your email to receive our newsletters.
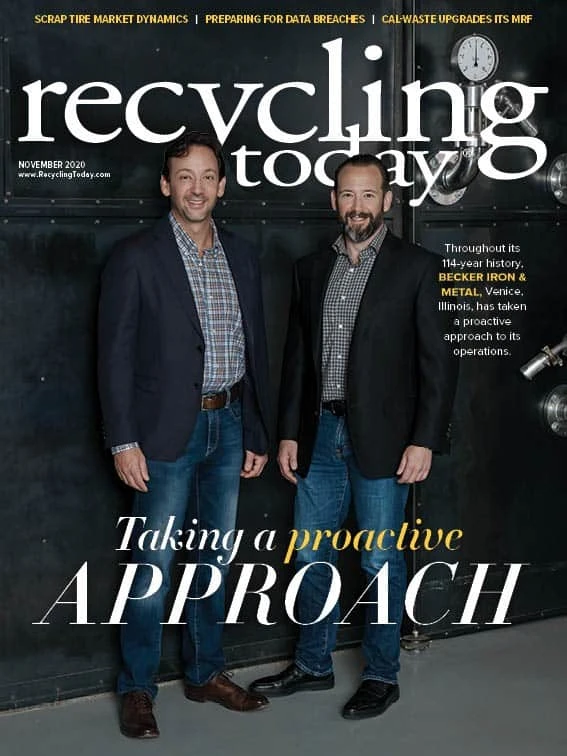
Explore the November 2020 Issue
Check out more from this issue and find your next story to read.
Latest from Recycling Today
- Electrostatic technology vies for role in ASR sorting
- ReMA board to consider changes to residential dual-, single-stream MRF specifications
- Trump’s ‘liberation day’ results in retaliatory tariffs
- Commentary: Waste, CPG industries must lean into data to make sustainable packaging a reality
- DPI acquires Concept Plastics Co.
- Stadler develops second Republic Services Polymer Center
- Japanese scrap can feed its EAF sector, study finds
- IRG cancels plans for Pennsylvania PRF