
Waste and recycling environments pose unique challenges to keeping truck scales functional and profitable. Since most recycling and solid waste facilities are heavily trafficked, keeping a truck scale up and running can be somewhat difficult. Additionally, properly maintained truck scales provide a hedge against losing thousands of dollars because of inaccurate weights.
Recycling operations need to consider four factors to maintain scales and weighing systems: the scale foundation; hardware, load cells and wiring; inspection and calibration; and scale usage and movement. It’s also wise to develop a course of action for potential issues that could affect truck scales and weighing systems.
1. The scale foundation
This area can cause the most trouble but is the easiest pitfall to avoid. Providing a sure foundation in the proper location is the first step in setting up a truck scale.
Because loose debris is associated with recycling or solid waste environments, it is always good to consider a truck scale design that discourages buildup around load cells and wiring. Some digital truck scale designs place load cells up into the scale deck, providing protection from garbage and dirt that accumulates near load cell stand bases.
If the load cells follow certain digital designs that are near the ground, frequent power washes will be necessary to clear debris buildup. It is vital to know the ingress protection (IP) rating of the load cells and wiring to prevent water and pressure damage during cleaning, so operators should become familiar with the IP rating system and know what level their load cells can handle when cleaning.
2. Inspect hardware
Digital truck scales are built to eliminate many of the problems associated with electronic scale designs. Many checks can be made by scale owners to prevent downtime and damage. Because junction boxes are eliminated in certain designs and most of the wiring is reduced, just a few places might cause issues.
End users also should inspect load cell cover plates. These fit snugly above the load cell pocket, so if the cover plates do not fit correctly, the chance of moisture and debris making their way down to the load cells increases.
Check to make sure load cell connectors are tight when fastened onto each individual load cell. Load cell connectors should not show signs of damage. Load cell cables should be examined for damage or chew marks from rodents. Any voids or areas that can be exposed to moisture or sediment can cause unreliable weighing or a lack of load cell readings.
Recycling and solid waste scales are exposed to highly acidic conditions that can damage paint and surfaces. Regularly check paint for rust and areas where paint has been eaten away because of corrosion. Truck scale manufacturers use heavy-duty paint and curing methods to prevent metal exposure, but truck scale owners must be diligent to protect their investments. Concrete-deck truck scales can provide a good option as they largely are unaffected by the corrosive elements that can damage steel-deck truck scales; however, steel-deck truck scales can be replaced and moved much more easily, so there is a trade-off.
Additionally, concrete, if not installed correctly, can crack and eventually damage the deck until it is irreparable, so scale owners should remain vigilant for signs of cracking.

Certain truck scale platforms have eliminated traditional checking systems that stabilize the scale for fast weighments, which simplifies problems associated with damaged checking equipment. These designs also greatly reduce rocking and movement that can damage a truck scale. For scales with traditional checking, check rods and bars should be examined for damage, and bumper bolts should be checked for cracking and fracturing. If either one of these failures is observed, it should be corrected immediately to prevent permanent damage to the scale deck.
Operators always should keep an eye on the deck of the truck scale. High volumes of overweight vehicles can damage the scale deck and render it useless.
3. Inspection and calibration
A calibration or inspection schedule should be arranged by a truck scale dealer the operator can trust. Truck scales used in recycling and solid waste likely will receive a great deal of wear and tear, so working out a calibration schedule with a qualified scale service company can be important. Normally, a yearly or twice-per-year schedule will suffice, but if a facility is heavily used, increased calibration frequency might be necessary.
Digital truck scale models can offer an advantage over analog truck scales because they can be monitored remotely by the dealers that place the truck scales in service. Information about the scale’s location, load cell configuration and specific load cell issues are all at the dealer’s fingertips with digital load cell systems. Some scales even are capable of transmitting warnings that alert the truck scale dealer to issues with the home run cable and load cell cables, among other items.
4. Scale usage and movement
Truck scales are designed to withstand abuse from trucks that enter and exit the weighbridge platforms. Truck scales that feature traditional checking are designed to move with traffic. Newer truck scales that have eliminated these traditional checking systems are designed to move slightly before settling into a steady position. Both systems will have longer life cycles if the scales are spared the stress of trucks coming in and out quickly.
Sponsored Content
Labor that Works
With 25 years of experience, Leadpoint delivers cost-effective workforce solutions tailored to your needs. We handle the recruiting, hiring, training, and onboarding to deliver stable, productive, and safety-focused teams. Our commitment to safety and quality ensures peace of mind with a reliable workforce that helps you achieve your goals.
Clearly marking entrances and exits with very low speed limits will reduce damage related to excessive speed. Guiderails also can alert a driver of the scale ahead and prepare him or her to slow down and help line up the vehicle with the lines of the weighbridge. Card readers and gating can help control traffic, as well.
Digital truck scales can provide an advantage over older types of weighbridge technologies. They can feature remote monitoring and eliminate burdensome traditional checking components and protect load cells to prevent many expensive repairs and downtime that can burden a recycling center or solid waste location. Diagnosis also can be done much more quickly.
A final note
Truck scale owners must take an active role in protecting their investments by following these tips. Applying this information will help to keep digital scales running for much longer, protecting operations’ profits and productivity.
Get curated news on YOUR industry.
Enter your email to receive our newsletters.
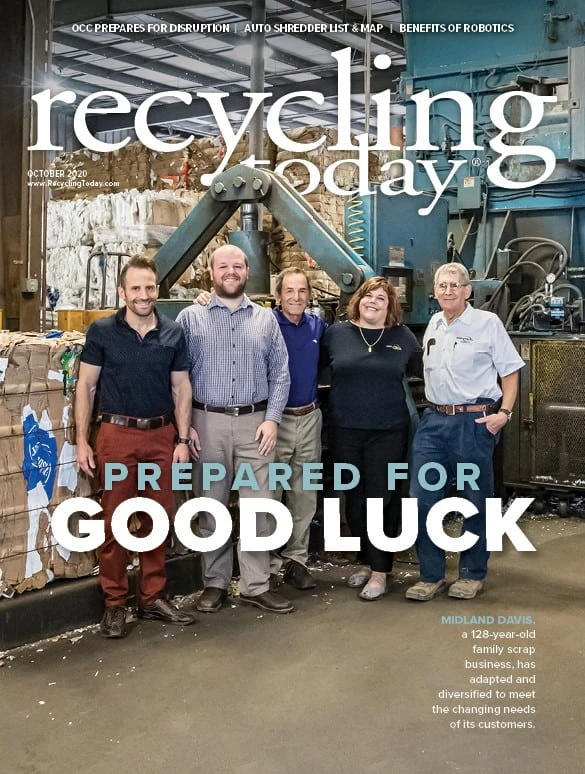
Explore the October 2020 Issue
Check out more from this issue and find your next story to read.
Latest from Recycling Today
- CP Group announces new senior vice president
- APR publishes Design Guide in French
- AmSty recorded first sales of PolyRenew Styrene in 2024
- PRE says EU’s plastic recycling industry at a breaking point
- Call2Recycle Canada, Staples Professional expand partnership
- Circular Services breaks ground on north Texas MRF
- Tariff uncertainty results in choppy nonferrous scrap flows
- CATL, Ellen MacArthur Foundation establish battery partnership