
One can say postconsumer plastics, particularly mixed plastics bales, have been hit most heavily by the Chinese central government’s changes to its import policies for recyclables. Two-thirds of bales comprised of Nos. 3-7 plastics were exported in 2016, says More Recycling CEO Nina Butler, who is based in Chapel Hill, North Carolina.
More Recycling is a research and consulting company with more than 20 years’ experience in recycling postconsumer materials, specifically plastics
“Pricing offers the best insight, and you can see a sharp drop as prices move into the negative as nearly all demand dries up,” Butler says.
In response to this greatly diminished demand, she says, “Some MRFs (material recovery facilities) have stored material, moved mixed plastic bales at negative pricing or let material run into the residual line while they focus on getting the highest quality fiber, given that’s their largest volume stream.”
The subject of this month’s cover story, Mid America Recycling, with MRFs in Des Moines, Iowa, and Lincoln, Nebraska, is among the MRF operators that have been able to keep this material moving, though not at a profit. Mick Barry, the company’s president, says a regional processor is taking its 3-7 plastics bales for further sorting. Mid America typically generates one load per quarter, which the processor picks up, but no money has been changing hands.
In an attempt to fill the void that exists in the market and to take advantage of the abundant material that is available, some processors, including Sims Municipal Recycling’s Sunset Park MRF in Brooklyn, New York, and Plastic Revolutions, Reidsville, North Carolina, have begun further sorting residential mixed plastics.
Stepping up

Maite Quinn, director of business development and sales, Sims Municipal Recycling, says China’s import restrictions mean her company has seen more opportunities to bid on 3-7 material in the last year. But the company has been further sorting mixed plastic bales for a few years.
“After the Green Fence in 2013, we started shooting on PP (polypropylene),” she says of Sims’ Sunset Park MRF. “At the time, many people did not have homes for their 3-7 [plastics], and we had the capacity, so we started offering the solution to local MRFs.”
Quinn says her company finds 3-7 bales, in particular, to be “a very mixed bunch.” She adds, “Every MRF produces a different quality. That is why it is very important to do audits of the material. Generally speaking, our quarterly audits on the same customers are pretty consistent.”
She says Sims pays suppliers based on the material composition of their bales. “The more high-value material in their bales, the more we pay. The numbers vary.”
Ed Handy, general manager for Plastic Revolutions, says his company began further sorting bales of Nos. 1-7 plastics earlier this year, investing $600,000 to add new equipment in the form of a baler and 16-station sorting line. Plastic Revolutions also added 35 employees to sort the material by hand.
The company, which specializes in recycling high-molecular weight plastics, as well as postconsumer plastic bottles, recovers the high-density polyethylene (HDPE) in these bales for further processing at its facility and the polyethylene terephthalate (PET), which it sells to Unifi, Greensboro, North Carolina.
While Handy says Plastic Revolutions can sort the material, he adds that it has not been without difficulty. “We can do it,” he says. “Making money at doing it is the problem,” he adds, despite obtaining this material for free or inexpensively.
Plastic Revolutions previously attempted to sort mixed bulky rigids by hand but abandoned that effort because of the economics.
To make processing the 1-7 bales more economical, he says the company is looking to add optical sorting equipment, preferably purchasing equipment from a plant that is no longer operating.
Stepping away

Butler says “many” MRFs are moving away from making a mixed plastic bale because of the current market. “There are markets for plastics beyond 1 and 2 bottles—if the material is segregated into discrete resins,” she continues. “So instead of producing a 3-7 bale, some MRFs are sorting for the higher volume/value portion of that 3-7 stream,” which is the PP. This type of plastic comprises 23 percent to 29 percent of a 3-7 bale, depending on whether the bales contain other rigid plastics or only small rigid plastics, respectively, Butler says.
“Not all MRFs have the capacity for further sorting,” she adds.
Liz Bedard, rigids program director for the Association of Plastic Recyclers (APR), headquartered in Washington, says that when China introduced Green Fence in 2013, some MRFs, particularly those on the East Coast, “saw the writing on the wall and made changes then.” Those changes involved producing a tubs and lids bale instead of a 3-7 bale.
The APR defines the tubs and lids bale as: “Any whole, injection-molded (occasionally formed from other processes) container containing polypropylene with the ASTM D7611 or Society of the Plastics Industry’s “No. 5, PP” resin identification code and/or polyethylene with either the (ASTM D7611) “No. 2, HDPE” and/or “No. 4, LDPE” resin identification codes, generated from a positive sort of a curbside, drop-off, or other public or private recycling collection programs.”
Bedard adds that some MRFs also have begun segregating PP, but they must have sufficient volume of this material to justify doing so.
Regarding 1-7 bales, she says they were more prevalent five or seven years ago. “Building a MRF is a high-cost investment,” Bedard explains. “If you build a MRF, you want to mine the incoming material to the highest degree possible.”
Butler agrees, saying 3-7 bales made up nearly 70 percent of all mixed resin bales in 2016 compared with 4 percent for 1-7 bales.
The current market has some communities, particularly on the West Coast, reconsidering the plastic packaging they collect at the curb for recycling. Butler says, “Communities, particularly in Oregon, have considered or already dropped materials from the list of acceptable items collected curbside.”
She adds, “Stopping and starting collection is an educational nightmare for communities, but many MRFs simply can’t keep up with the amount and quality requirements for fiber so are forced to forgo their focus on capturing the smaller amounts of plastics beyond bottles.”
In addition to MRFs and communities reconsidering the types of plastic packaging they accept for recycling, one company that has operated facilities to sort mixed plastics recovered by MRFs has shuttered operations in recent years.
QRS Recycling of Georgia filed for Chapter 11 bankruptcy in the summer of 2016. QRS’ joint venture with Canusa Hershman Recycling Co., QRS of Maryland LLC, suspended operations at its Dundalk, Maryland, plastics recovery facility (PRF) in August 2017, saying it intended to optimize its equipment. That plant was opened in 2015 and featured more than $10 million in processing equipment to sort mixed plastics.
The QRS of Maryland facility remains idled as of press time, and QRS has backed out of the partnership, according to published reports, leaving Canusa Hershman Recycling, with corporate offices in Baltimore and Branford, Connecticut, as the sole owner. (QRS did not respond to interview requests.)Even before these closures, Bedard says the domestic processing landscape for this material was not particularly robust. “In the coming year, I expect that to change for the positive and that we’ll see more market options.”
“Based on PlasticsMarkets.org, a free buyer/supplier marketplace that More manages, there were 11 U.S. buyers for 3-7 bales,” Butler says. “Some of these buyers may still only be taking these materials at negative pricing.”
She continues, “These are buyers of mixed rigid plastics that were positively confirmed after the National Sword took effect in late 2017. Things are constantly changing, though.”
Stepping forward
Butler says the solution to the problems facing residential mixed plastics likely involves a combination of measures that include upgrades to key primary MRFs and added infrastructure “in the form of strategically located secondary processing facilities,” such as PRFs and secondary material recovery facilities (SMRFs).
She views it as a chicken and egg scenario, however. “There must be steady supply to warrant investment for adjustments needed to incorporate PCR (postconsumer resin), but MRFs need demand for their commodities to warrant investment in improved sorting capacity to supply the quality needed by reclaimers and end users,” Butler says.
Bedard says the APR started its Recycling Demand Champions program to create demand for residential mixed plastics. This program seeks to expand the market for postconsumer plastics, driving investment, increasing supply and producing more high-quality PCR.
The first phase of the campaign focused on work in process (WIP) durable goods, such as pallets and crates, but has expanded to include new PCR applications.
Butler says recycled content policies also could help to increase PCR demand.
“We need to address the economic challenges for recycling,” she says. “Collection is not all there is to recycling. Getting PCR into products is critical for a healthy recycling system.
“The flow of material offshore stunted our domestic investment in adequate sorting capacity,” Butler continues. “If we want to continue to see plastics beyond bottles recycled in significant volumes, we will need to optimize recycling from education, collection, sorting [and reclamation] to end use.”
Get curated news on YOUR industry.
Enter your email to receive our newsletters.
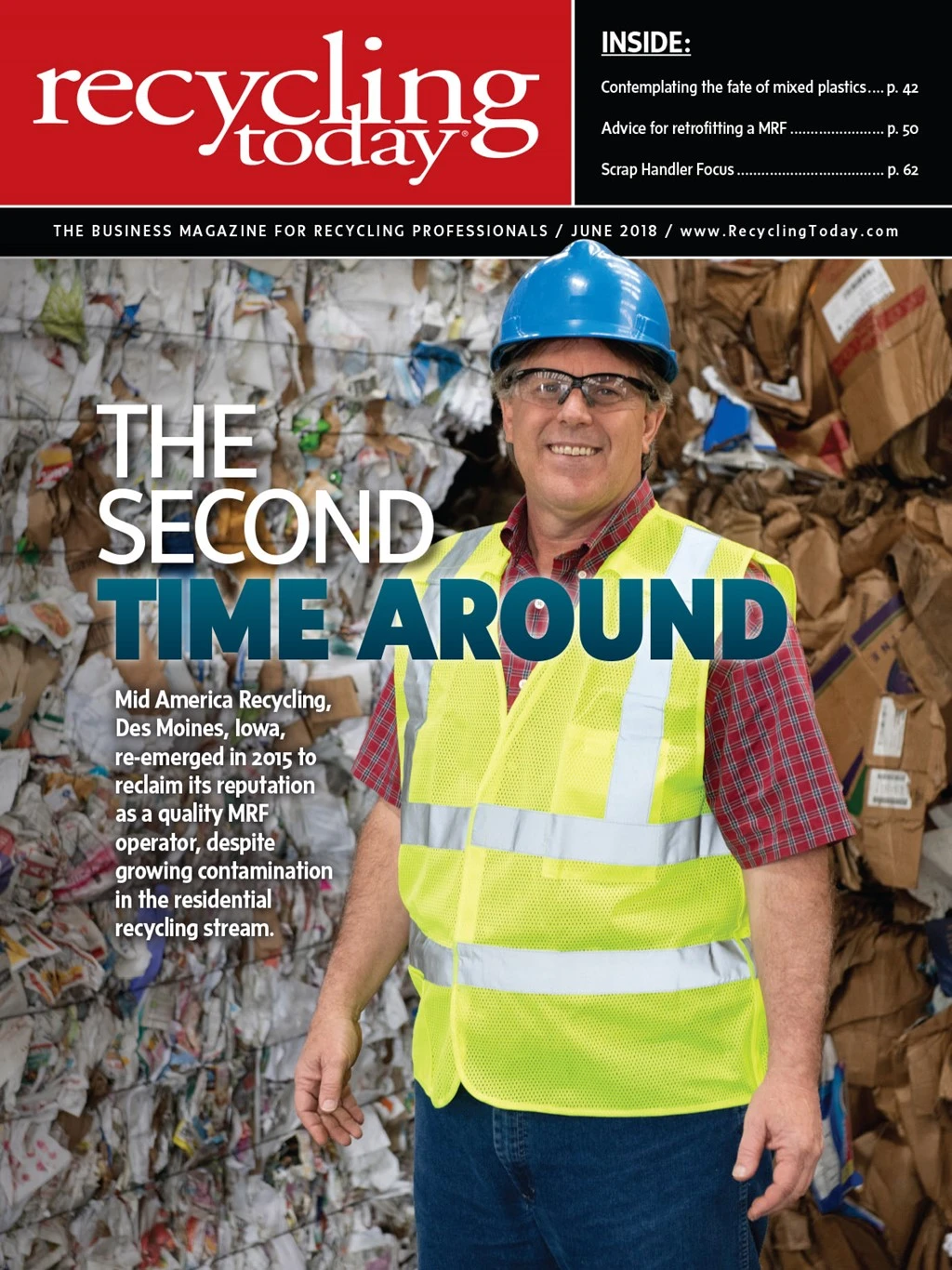
Explore the June 2018 Issue
Check out more from this issue and find your next story to read.
Latest from Recycling Today
- Recycled steel price crosses $500 per ton threshold
- Smithers report looks at PCR plastic’s near-term prospects
- Plastics association quantifies US-EU trade dispute impacts
- Nucor expects slimmer profits in early 2025
- CP Group announces new senior vice president
- APR publishes Design Guide in French
- AmSty recorded first sales of PolyRenew Styrene in 2024
- PRE says EU’s plastic recycling industry at a breaking point