
A recycling facility with long lines experiences delays because of their manual systems, which ultimatley cause the loss of repeat customers.
The Recycling Operations Manager (ROM) software is designed to be easy to use by scale house employees, so truck traffic keeps moving swiftly across the scale. "Before, weighing in customers was a long, multi-step process . . . our employee was writing out a slip and then walking a ticket into the office," says Brian Giordano of Giordano’s Vineland Scrap. "Now, the computer reads the scale and prints a ticket. It’s a lot smoother and faster for customers."
Skagit River Steel & Recycling in Burlington, Wash., has experienced similar results with ROM. "21st Century Programming products allow our business to have seamless scale weights, pricing sales orders and inventory accessibility," says the company’s Lois Young.
Additional features such as touchscreens, barcoding systems, ATMs and camera systems also address key operational problems that can cause delays.
Repeat customers are issued their own cards with their own unique barcodes, helping to speed up customer transactions. The idea is to keep each transaction simple for customers and employees alike, say the Kanes.
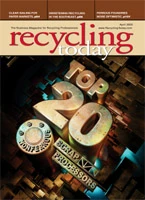
Explore the April 2005 Issue
Check out more from this issue and find your next story to read.
Latest from Recycling Today
- P+PB adds new board members
- BlueScope, BHP & Rio Tinto select site for electric smelting furnace pilot plant
- Magnomer joins Canada Plastics Pact
- Out of touch with reality
- Electra names new CFO
- WM of Pennsylvania awarded RNG vehicle funding
- Nucor receives West Virginia funding assist
- Ferrous market ends 2024 in familiar rut