Anode—
A 99 percent pure form of copper that is typically sent through an electro-refining process for further purification, ultimately emerging as copper cathode.Automobile Shredder—
A hammermill-style shredder large enough to shred whole cars into fist-sized chunks in less than a minute.Automotive Shredder Residue (ASR)—
The material left over after an automobile has been shredded and the ferrous metal and other marketable materials have been separated. Also known as fluff.Balers—
Machines that compress scrap for shipment as condensed, sheared, and tied cubes.Basic Oxygen Furnace (BOF)—
The updated replacement of the traditional open-hearth furnace, the BOF refines molten iron mixed with steel scrap in a process that can take place in less than one hour. Unlike electric arc furnaces, which can melt up to 100 percent ferrous scrap, melts taking place in BOFs can usually contain no more than about 25 percent scrap.Blister—
The form of copper as it leaves the Bessemer process, so named because escpaing elements leave "blisters" on the surface. Copper in blister form can be 99% pure but is then further refined.Capacity—
Steel mills are often ranked by two capacity types. Engineered capacity is the volume of steel a mill could produce if optimal conditions are met year-round. True capacity is usually a lower figure that takes into account standard maintenance procedures and seasonal factors that affect operating conditions.Cathode—
A form of copper produced through an electrowinning or electrolytic process. It can be produced in purity levels of 99.9 percent.Charge—
The material contained in a given steel furnace melt, such as a mixture of scrap metal and pig iron in an electric arc furnace. The act of loading and heating the material in the furnace is also known as charging.Consolidation—
The act of forming a publicly traded company with the purpose of acquiring existing firms engaged in identical or related businesses to create national or global corporation with significant market share.Deox—
Aluminum in the form of various shapes, such as shot, cones, stars or pyramids that when added to molten steel reacts to form stable oxides and reduce the amount of dissolved oxygen, producing a stronger finished product.Direct Reduced Iron (DRI)—
A scrap substitute created by a process that uses natural gas to produce a substance that contains as much as 97 percent pure iron. The resulting material is desirable for its low tramp element content, but requires an affordable supply of natural gas to be produced economically.Electric Arc Furnace (EAF)—
A steel-making furnace in which ferrous scrap can make up to 100 percent of the material melted. The heat in the furnace is created by electricity that travels (or arcs) from graphite electrodes to the material to be melted. The term "mini-mill" is used synonymously with steel mills that have EAFs.Feedstock—
Any material used at the front end of an industrial process. For a scrap processor operating a ferrous shredder, automobile hulks might be considered feedstock. At a mini-mill, ferrous scrap or scrap substitutes would be the feedstock material, while nonferrous scrap is a feedstock at secondary smelters.Hammermill—
A high-speed rotor equipped with large hammers for pulverizing material and metallic objects into smaller sizes.Home Scrap—
Excess steel that is generated at a mill and often routed back to the furnace.Hot Briquetted Iron (HBI)—
A form of direct-reduced iron (DRI) formed into bricks, chunks or ingots.Ingots—
Molds in which metal is cast or a mass of metal cast into a convenient shape for storage or transportation to be later processed.Iron Carbide—
A scrap substitute that uses natural gas in its manufacturing process to create a material that is roughly 90 percent iron and 6 percent carbon.Least Cost Suitable Charge (LCSC)—
An electric arc furnace formula to determine what to use in any given melt based on current prices and suitable chemical composition. The goal is to obtain a quality melt while not overpaying.Magnetic Separation—
A system to remove ferrous metals from other materials using magnets to attract the ferrous items.Melting Yield—
The amount of steel produced as a percentage of feedstock entering the furnace at a steel mill.Mini-mills—
A sub-category of steel mills often defined by the presence of electric arc furnaces. Many financial analysts also categorize mini-mills as using non-union labor and being operated by smaller, newer companies, relative to integrated or BOF operators.No. 1 Heavy Melt—
Ferrous scrap grade consisting of iron and steel items ¼-inch or more in thickness measuring no more than 60 inches by 18 inches, to fit in a standard charging box.No. 2 Scrap—
Ferrous scrap grade consisting of iron and steel items less than ¼-inch thick but more than 1/8-inch thick, and measuring no more than 60 inches by 18 inches, to fit in a standard charging box.Pig Iron—
A cast iron material produced in a blast furnace.Prompt Industrial Scrap—
Excess metal or other material generated at manufacturing facilities. It is often auctioned to scrap buyers or contracted for processing by the generator.Remelt Secondary Ingot (RSI)—
Aluminum scrap that is recycled into an intermediate product without a specific chemical composition. Independent fabricators and companies that melt scrap or dross to produce RSI or molten metal that is used in their plants for direct processing or sold in the market commonly use this technique.Scrap Substitutes—
High-iron content materials used as replacements for ferrous scrap in electric arc furnaces. Much of the scrap substitute made is manufactured by steel mini-mill companies seeking to ensure a supply for their furnaces. (Also see "Direct Reduced Iron," "Iron Carbide," and "Pig Iron.").Shear—
A machine that cuts metal scrap (after it has been condensed) to produce uniform shapes ready to be tied, shipped and melted.Shredded Scrap—
The pieces of ferrous scrap produced by shredders, often from shredded vehicles and appliances. The fist-sized chunks are transportable and saleable as a commodity.Smelter—
A facility that melts or fuses (as ore), often producing an accompanying chemical change usually to separate out the metal.Spectrometer—
An instrument that measures wavelengths of light spectra to determine the chemical composition of an item. They are often used to check for tramp elements or to determine alloys.Toll Processing—
One company performing a value-added service to improve material belonging to another company. Within the scrap industry, this can be the processing of prompt scrap from a nearby industrial facility. Within the steel industry, this can be the slitting, rolling or coating of steel produced at a nearby mill.Tonnage Types—
Measures commonly used when weighing or shipping scrap and other commodities:•
Gross Ton—Weighing 2,240 pounds, this tonnage measurement isoften used to measure ferrous scrap and raw commodities such as iron ore.
•
Metric Ton—At 2,205 pounds (or 1,000 kilograms), this unit of measure is standard in most of the world outside of the U.S.
•
Short Ton—2,000 pounds, the most standard ton measurement used within the U.S.Tramp Elements—
Elements considered undesirable in most steel furnace melts, but often found mixed with ferrous scrap, such as copper, nickel, chromium, tin and molybdenum.Turnings—
Small bits of scrap created as a result of lathing or other machining operations at industrial facilities.White Goods—
A term for large household appliances such as refrigerators, washers and dryers that are part of the ferrous scrap stream.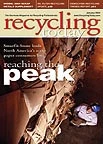
Explore the January 2004 Issue
Check out more from this issue and find your next story to read.
Latest from Recycling Today
- Nucor receives West Virginia funding assist
- Ferrous market ends 2024 in familiar rut
- Aqua Metals secures $1.5M loan, reports operational strides
- AF&PA urges veto of NY bill
- Aluminum Association includes recycling among 2025 policy priorities
- AISI applauds waterways spending bill
- Lux Research questions hydrogen’s transportation role
- Sonoco selling thermoformed, flexible packaging business to Toppan for $1.8B