Many factors affect the productivity of scrap handlers, but a systematic approach to choosing, configuring, operating, maintaining and replacing each machine helps ensure success.
|
Choosing the correct size and configuration of a scrap handler to match job requirements should be the first step, and is the most important factor in attaining high productivity.
Machine Sizing.
The size of the machine must match job requirements. Too large of a machine will result in higher acquisition and maintenance costs as well as in greater fuel consumption, which is increasing in importance as fuel prices continue to rise. However, too small of a machine will not keep up with the incoming or outgoing material movement. Additionally, undersized machines will not keep processing equipment, such as shears, balers and shredders, operating at their maximum efficiency.To determine the size of the material handler required, the machine should be matched to the ton-per-hour requirements of the particular job. But many different factors affect productivity, including:
Mobility.
Will the machine be required to travel within the yard, or be used at a stationary job, such as feeding a piece of processing equipment?Estimated cycle time.
Is the site laid out so the machine can achieve its fastest possible cycle time? Each job should be set up so that the machine will swing the minimum degrees and so that it can reach its lift and release targets with a minimum of boom and stick movement, swing movement and little or no travel.Material and work availability.
Is there enough material or work continuously available in the yard for the machine to achieve its rated production capacity?Material size, type and density.
The more consistent the type and density of material, the simpler it becomes to calculate production and work tool type and size requirements. Much better efficiency can be achieved if the material is consistent. In cases where the material varies significantly in type and density, consider having multiple sizes and types of work tools. Switching the work tool to best match the material being handled can help boost productivity.To calculate the productivity of a machine in a given application, several numbers are needed. They include the percent of time the machine will be traveling; the minutes per hour the machine will operate (typically 50 minutes); the amount of swing required, which affects cycle time for loading; grapple or magnet capacity in tons; the fill factor of the grapple (this could be 100 percent, but may be less in some materials); machine availability (percent of time the machine is able to run); and planned downtime for maintenance and refueling.
Different machine configurations and machine management practices allow optimizing productivity for a specific application.
PLATFORMS AND BOOMS.
If the scrap handler must move frequently to different sites in the yard, a scrap handler mounted on a wheeled undercarriage should be considered instead of a scrap handler mounted on a track undercarriage. A wheeled scrap handler can travel more than twice as fast as a tracked scrap handler.Another reason for selecting wheeled scrap handlers is to protect the concrete or asphalt surfaces that many yards use to meet environmental requirements or improve the quality of scrap.
If wheeled scrap handlers are used, the yard must plan to periodically clear scrap and other debris from the machine’s travel routes to minimize the potential risk of tire damage.
Many manufacturers offer several different front linkages with varying maximum reaches for each scrap handler model. A longer maximum reach should make the machine more versatile, such as being able to reach the front end of a trailer when loading material from the rear.
But the longer the front linkage, the smaller the work tool must be and the lower the potential productivity will be. Thus, longer reach is not better unless the yard has a true need for it.
Such needs could include the ability to reach the entire truck body length without repositioning the machine; the ability to feed scrap processing equipment from a larger stockpile; and the ability to stack scrap material higher when needed in light of the yard’s space limitations.
THE RIGHT TOOL FOR THE JOB.
Choosing the correct type and size of work tool is critical in maximizing scrap handler productivity. Most commonly, either an orange peel grapple or a magnet is used as the work tool.To correctly size the work tool, the range of material density the machine is expected to handle needs to be considered. Scrap can vary from 500 to 3,500 pounds per cubic yard.
As a general rule, heavier and denser ferrous materials are more efficiently handled with a magnet, and lighter, less dense materials (and certainly nonferrous metals) are more efficiently handled by an orange peel grapple.
The weight of the work tool also must be considered. By adding the net attachment weight to the capacity of the work tool multiplied by the density, you can arrive at the total weight (work tool plus payload) that the machine will be required to lift. This number can then be compared to the lift/range chart of the machine.
To achieve the maximum efficiency, the total gross weight should fall as closely as possible to, while not exceeding, the capacity number shown on the lift/range chart within the maximum reach and range that the job will require. If the machine is not expected to lift at maximum reach, or the density varies widely, consider those factors when sizing the work tool.
In addition to these sizing criteria, the flows and pressures of the grapple (exerted during open-close operations and when rotating) must be matched to the scrap handler hydraulic circuit.
Similarly, the power requirements of the magnet should not exceed the generator system capacity.
UP AND RUNNING.
A scrap handler is only making money when it is running, which is a strong argument for maximizing availability.For scrap handlers in critical parts of the operation, such as feeding scrap processing equipment, consistent availability is a must, and thus keeping unscheduled dowtime to a minimum is critical.
Machine replacement cycles should be planned so newer machines with higher availability will be put into the most critical, high-productivity areas.
It may be more economical to replace machines on a more frequent basis than to suffer from the low availability and high repair cost of older machines. Or, older machines can be put into non-critical areas of the yard where availability is less important.
Preventative maintenance will help ensure maximum uptime. Using scheduled oil sampling to determine component wear rates and doing planned rebuilds during slow periods can maximize availability and minimize repair costs by catching failures before they become catastrophic.
Consider having the equipment dealer maintain the equipment. Choose a dealer who has the trained service personnel and support from the manufacturer for prompt parts availability.
If the dealer does all maintenance on the machine, yard personnel can concentrate on what they do best—processing scrap in the yard.
At Caterpillar Inc., we take a systems and solutions approach that considers all of the yard’s key needs. It starts with the proper machine purchase—selecting the right machine for the yard and matching the proper work tool to it.
Additionally, we continue with applying the proper maintenance program, training operators and maintenance personnel and planning replacement cycles to maximize machine availability. A systematic approach pays off through increased productivity and profitability.
The author is a senior sales engineer with Caterpillar Inc., working from the company’s Aurora, Ill., plant and office.
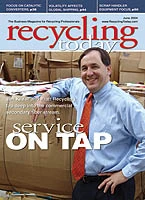
Explore the June 2004 Issue
Check out more from this issue and find your next story to read.
Latest from Recycling Today
- Reconomy brands receive platinum ratings from EcoVadis
- Sortera Technologies ‘owning and operating’ aluminum sorting solutions
- IDTechEx sees electric-powered construction equipment growth
- Global steel output recedes in November
- Fitch Ratings sees reasons for steel optimism in 2025
- P+PB adds new board members
- BlueScope, BHP & Rio Tinto select site for electric smelting furnace pilot plant
- Magnomer joins Canada Plastics Pact