Hydraulic cranes and scrap handlers have distinct differences. So, by definition, scrap and material handlers are not exactly cranes. But for safety reasons, if it walks like a crane and quacks like a crane, it might be best to consider it a crane.
Scrap and material handlers have been a great innovation for the scrap metal recycling industry. Excavators have been re-designed and modified to perform repetitive movement of scrap faster and more efficiently than was previously accomplished with cranes.
|
Sleek, compact and powerful, these machines have steadily replaced many lattice boom cranes whose design hearkens back to the Civil War era. That’s the good news. Yet, for safety purposes, it is also often bad news.
CHANGING OF THE GUARD. For decades, cranes in the scrap industry hoisted and moved material that weighed far less than the crane’s lifting capacity. Yet, they did so numerous times over the course of an hour, something they were not ideally designed to accomplish.
In these situations, great strain was placed on the boom, hoist and other parts from this continuous duty cycle. Yet the use of these cranes also meant they were carefully and meticulously inspected and maintained. OSHA delineated specific daily, weekly and periodic inspections that were necessary.
Only the most experienced workers operated the crane. And, most importantly, workers learned to respect these tall and powerful machines. They steered a wide path around them and would cross its path only when they had the operator’s attention and the long swing of its magnet or grapple was brought to a stop.
Enter the scrap handler, known affectionately by many as the hydraulic crane—a distant cousin of the ancient workhorse. It sits lower to the ground, is easier to operate and can move more scrap per hour. It is easier to move and to reposition than its lattice boom crane cousins and it comes without OSHA requirements. The scrap handler has also brought with it, though, new forms of accidents.
SUDDEN MOVEMENTS. The tall, cumbersome crane seldom moved from its spot. But the new material handler can be easily and frequently moved or repositioned throughout the yard.
Pick This Up |
In addition to its voluntary standard for scrap and material handlers, the American Society of Mechanical Engineers (ASME) has also developed standards for below-the-hook lifting devices.
B30.20 - 2003 Below-the-Hook Lifting Devices, a 56-page book from ASME, includes "provisions that apply to the marking, construction, installation, inspection, testing, maintenance, and operation of below-the-hook lifting devices, other than slings, used for attaching loads to hoist," according to the society’s Web site.
The book includes chapters on structural and mechanical lifting devices, vacuum lifting devices, proximally operated lifting magnets, remotely operated lifting magnets and scrap and material handling grapples.
For more information or to order the book, visit www.asme.org. |
With its magnet or grapple held high, it travels a path never followed by taller machinery—a path that can potentially be crossed by high voltage wires. In these cases, the handler’s boom will rip through the wires sending a shower of sparks down around the operator’s cab.
Operators who would never have tried to jump from a crane’s high cab have attempted to leap the short distance to the ground from a scrap handler. Unknown to them, they were safe in the cab, yet could suffer severe or even fatal injuries when they touched the now electrically-charged outer structure.
The potential for movement has caused other problems. Operators have looked at the compact size of the new machines and have mistaken them for having all-terrain capabilities. This has lead to handlers toppling over and pinning operators in the cab or crushing workers nearby.
One tragic event involved a material handler in a fast-moving thunder storm. Several workers found shelter next to a scrap handler as the operator slowly maneuvered toward permanent shelter. A bolt of lightening struck the handler’s boom. The driver was not harmed, but the workers walking next to the handler got the brunt of the charge. One worker died while another was severely burned.
The now shorter distance from ground to cab has also presented new safety issues. Operators climbing down from the high cab of a crane would take great care in navigating the ladder. Yet many operators now working in a much lower cab will commonly climb down a few rungs of the ladder and then jump to the ground rather than continue their climb. This has lead to serious knee and back injuries.
Inspection and maintenance standards may also go by the wayside with scrap handlers. OSHA does not have regulations governing scrap handlers. There are no mandatory requirements for daily or periodic inspections. Yet parts can still wear, and hydraulic hoses can spring tiny leaks. Indeed, units, if neglected, can experience failures that can cause the boom to come crashing down.
So if it walks like a crane and quacks like a crane—even if it is a scrap handler—this duck certainly deserves the respect and meticulous attention that was lavished on its predecessor.
STAYING CURRENT. Yard managers and operators who want to make sure they are putting safety first may wish to dust off the concepts and procedures that used to keep that "turn-of-the-century" lattice boom crane running smoothly and safely. In most cases, these procedures can be updated for hydraulic scrap handlers. Following are some suggestions.
The American Society of Mechanical Engineers (ASME) has developed a voluntary standard for scrap and material handlers. This standard, ASME B30.25-2003, provides recommendations for frequent and periodic inspections of this equipment.
The standard recommends that hydraulic components, safety devices and controls be inspected daily. The ASME standard further lists numerous items that should be included in more complete inspections conducted by a qualified person. It also includes recommendations for an effective preventive maintenance program.
Additionally, the ASME standard includes hand signals for use by employees on the ground to communicate with the scrap handler operator. Most of the signals had formerly been used when communicating with a lattice boom crane operator.
Certainly, today most operators can stay in communication with ground crews via radio. Yet radios can malfunction or be left in the break room, so knowing the signals can still come in handy.
Scrap handlers should not be operated near or under electrical power lines—ever. It is very difficult to judge whether a boom will clear a power line. Taking this chance is foolish and should not be done at all.
Driving a loader beneath power lines can also be tricky. The only really safe way to do this is to travel with the tip of the boom below the operator’s line of direct site. That way, if the driver sees that the cab will easily clear, then there is no doubt that the rest of the equipment will also make it through safely.
This operation might require removing the arm or jib from the boom or fully dropping the boom so that the magnet or grapple attachment rests on a slow moving flat bed trailer leading the way. All necessary actions should be taken to keep any part of the handler far away from the power lines.
Operators climbing up or down from the cab should always maintain three-point contact with the ladder. This means that one hand and both feet or both hands and one foot are always in contact with the rungs of the ladder. This continues until the operator is safely in the cab or has touched one foot on the ground. It is one small step for man, because one giant leap could hurt.
More information on these standards, which I helped develop as part of an ASME subcommittee, can be found on the online store at the ASME Web site at www.asme.org.
The author is the founder of Maryland-based Recycling Risk Management LLC, which specializes in safety, loss prevention and compliance consulting for the recycling industry. Previously, he was director of risk management for the Institute of Scrap Recycling Industries Inc. He can be contacted via e-mail at mikemattia@recyclingrisk.org.
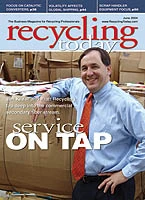
Explore the June 2004 Issue
Check out more from this issue and find your next story to read.
Latest from Recycling Today
- ReMA board to consider changes to residential dual-, single-stream MRF specifications
- Trump’s ‘liberation day’ results in retaliatory tariffs
- Commentary: Waste, CPG industries must lean into data to make sustainable packaging a reality
- DPI acquires Concept Plastics Co.
- Stadler develops second Republic Services Polymer Center
- Japanese scrap can feed its EAF sector, study finds
- IRG cancels plans for Pennsylvania PRF
- WIH Resource Group celebrates 20th anniversary