|
Mike Schwebke of Joseph Behr & Sons Inc., Rockford, Ill., suggests determining a yard’s material handling needs prior to selecting the attachments to outfit a scrap handler. If he were going into business today, Schwebke says, he would employ hydraulic cranes outfitted with combination magnet/grapple attachments, which he likes because of their versatility. Behr currently operates four or five cranes outfitted with magnet/grapple combinations.
"You can sort as well as grab nonferrous material and sort unshreddables out of white goods," he says of the magnet/grapple combinations. "There are trade-offs, but for the most part, it works pretty well."
Schwebke says adding a magnet to a grapple causes the grapple to lose from half a yard to three quarters of a yard in capacity. Additionally, a magnet/grapple combination is incapable of 360-degree rotation because of interference from the wiring for the magnet, he says.
"The magnet has its place 25 percent of the time in this business," Schwebke says, "but the grapple has definitely taken over the business."
GETTING A LIFT.
Behr uses its magnets for cleaning up behind the grapple and for feeding one of its shears unprepared plate material.However, at Midland-Davis in Moline, Ill., the magnets are the workhorses of the yard. "We don’t have any grapples," the company’s Mitchell Davis says. "We have lattice boom cranes. We don’t have a crane with a shear on the end or hydraulic knuckle booms with grapples. We don’t do autos."
Davis says that 90 percent of the company’s incoming material arrives in roll-off containers and is dumped in the yard. "We use it for moving material, loading, sorting, picking and cleaning up the roadways," he says.
Jed Morris of Morris Recycling Inc. (MRI), New Albany, Miss., says that magnets are best suited for handling "small, dense scrap that lays close together."
Moving Material |
The following is a list of attachments and their uses.
Crusher: Pulverizing concrete and rock
Lifting Magnet: Ferrous scrap; well suited for sweeping the yard and removing ferrous scrap from the bottom of rail cars
Lifting Magnet/Grapple Combination: Ferrous and other metals/nonmetallic scrap
Log-Type Grapple: Large metal scrap, including auto hulks
Mobile Shear: Cutting scrap metal and moving long pieces of metal scrap
Narrow-Tine Grapple: Softer scrap, such as cardboard, plastics and tires
Orange Peel Grapple: Metallic/nonmetallic scrap
Tulip/Full-Leaf Grapple: Metallic/nonmetallic scrap that includes small pieces |
Depending on the yard, MRI may switch between grapples and magnets. "In operations where we only have one crane, we tend to swap," Morris says. "In operations where we have multiple cranes, we typically have at least one unit that is interchangeable. On a scrap handler, a magnet just does not move enough scrap except in very specific applications where it is a necessity," he says.
While lifting magnets are not capable of the versatility that grapples provide, they require little maintenance and can often provide decades of service.
"Magnets, if you take care of them and don’t use them as battering rams or to break cast or anything like that—which, unfortunately, some people do—about the only thing you’ll have to do is periodically fix the electrical connectors," Davis says.
Morris also stresses the need for training staff on the proper operation of lifting magnets. "The biggest thing maintenance can do is help inform operators on the proper operational care," he says. "Magnets are insulated coils that when run at too high of a duty cycle can become hot, deteriorating the insulation and causing a short. Making sure the operator only turns the magnet on after it is in the pile or otherwise touching the scrap will extend the life of the magnet and improve the efficiency of the unit," Morris says. "Otherwise, a magnet is not a battering ram and does not need to be used to break or beat against anything." He adds, "In some instances over a lot of tons, you may have to build up or replace wear surfaces."
Schwebke says that the magnets’ chains and pins will occasionally need to be replaced. "We may go through a set of chains and pins in eight months." He says that Behr has had magnets in service for 25 years and has only had about three repaired for dead shorts.
While grapples require more maintenance than lifting magnets, they are the preferred scrap-handling tools at Behr’s yards.
NIMBLE FINGERS.
"I’d say 75 percent of out work in our yard is done with grapples," Schwebke says. "We actually handle all of our inbound, unprepared material, which is the bulky material, like combines and farm equipment and that kind of thing. Feeding our other shear with this kind of material with a magnet/grapple combination works out pretty well."He continues, "We get a lot of machines in that weigh probably 20 tons. Years ago, we used to rig all of that with chains and manpower. Now we have a big enough grapple that we get a hold of these things and unload them within minutes."
Schwebke says grapples are "faster and more efficient by far" when compared to magnets.
While Randy Katz of City Scrap Co., Akron, says the yard uses magnets to load outbound trucks, grapples are used to feed the yard’s shredders. "You could never pick up an auto with a magnet," he says. "A grapple picks up material beautifully."
Morris says the type of scrap a grapple is capable of handling varies according to the style of grapple used. "There are some fully enclosed grapples, which are better suited for smaller, dense, free-flowing scrap," he says. "The straight-tine grapples are better suited for large, bulky scrap, whether light or dense. Size is also a factor, again depending on the application and duty cycle."
MRI employs four- and five-tine orange-peel grapples. "The five-tine grapples work best for multi-task type uses and help keep us standardized so we can rotate our grapples through maintenance," Morris says. "We use four-tine grapple in the larger sizes, as they fit inside a trailer better."
Grapples require more maintenance then lifting magnets. Schwebke says, "It’s tough to keep scrap out of the grapple." When that happens, the cylinders and hoses may have to be repaired or replaced. The tips of the grapple’s tines have to be rebuilt or replaced as well. "The tips need to be replaced every four to six months, sometimes sooner," he says.
Behr is currently experimenting with replaceable tips from one manufacturer, which are attached to the tines of the grapple with a pin and a clip. Compared to the weld-on tips, Schwebke says the replaceable tips could save eight or 10 hours, if not more, in maintenance.
"We’ll convert if that really works out well," he says.
Additionally, Schwebke is looking at new grapples that are designed to avoid excessive wear on the tines by preventing the cylinders from over-extending once the tips have worn. He says older grapples do not have "stoppers" on their cylinders to prevent them from extending beyond the center point. "New grapples are addressing that issue."
Schwebke says these kinds of innovations represent money and time savings for scrap recyclers because they help operations to avoid equipment-related downtime. "I’m always looking for new ideas to avoid this issue," he says.
Morris suggests doing your homework prior to purchasing a grapple. "A grapple really takes a beating, and you better get one that can stand up to your operation," he says. "They require maintenance. We spend more money on repairing grapples then we do on repairing the crane itself."
The author is associate editor of Recycling Today and can be contacted via e-mail at dtoto@RecyclingToday.com.
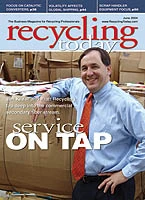
Explore the June 2004 Issue
Check out more from this issue and find your next story to read.
Latest from Recycling Today
- Reconomy brands receive platinum ratings from EcoVadis
- Sortera Technologies ‘owning and operating’ aluminum sorting solutions
- IDTechEx sees electric-powered construction equipment growth
- Global steel output recedes in November
- Fitch Ratings sees reasons for steel optimism in 2025
- P+PB adds new board members
- BlueScope, BHP & Rio Tinto select site for electric smelting furnace pilot plant
- Magnomer joins Canada Plastics Pact