Suppliers of material handling equipment must be ready to outfit their hydraulic machines with either a grapple or a magnet when the machine is sold into the
ferrous scrap market.
LBX Co., Lexington, Ky., is among the manufacturers who must design their machines to be well-suited to work with either attachment—or to work for recyclers who will switch between any number of types of attachments, including grapples, magnets or mobile shears.
The company sells several models of hydraulic handlers under the Link-Belt brand name, with its LX and Quantum models designed specifically for scrap recyclers.
GRAPPLING WITH STEADY SHIPMENTS. Super Salvage, a scrap company in Washington, D.C., took delivery of its 370 LX Material Handler in early 2003 to replace an older Link-Belt Quantum machine.
Set on a small one-acre lot just a few miles from the nation’s capitol, Super Salvage keeps its material handler busy all day long, off-loading trucks and feeding the materials to a shear. According to Dee Armstrong, Super Salvage’s mechanical supervisor, "It bears the brunt of the work load of this whole yard."
Super Salvage accepts ferrous and nonferrous metals and processes them to specification for various mills. In addition to the new Link-Belt 370 LX, the company runs two Link-Belt C2 material handlers, five forklifts and a skid steer loader that feeds an 800-ton Harris guillotine shear and four baler presses.
The 370 at Super Salvage is equipped with a one-yard, four-tine grapple and a Young three-piece boom. Armstrong also ordered the machine with a dealer installed auto-lube system that he says has made his job a lot easier. He praises the machine’s performance on the job.
While the 370 LX has only been at work for a few months, it has already had to endure the tough conditions of the job site. Armstrong said the 370 LX actually has to withstand more stress and extreme conditions than any of the other machines on the lot.
"Nothing stays clean in this yard. And the 370 gets insulation, metals and other projectiles thrown at it all the time," says Armstrong. "Still, it keeps going strong. It’s very powerful, fast and efficient. And it’s so quiet that you can barely hear it running unless you’re right up close," says Armstrong.
Armstrong credits an on-board diagnostic system that allows service personnel to quickly analyze up to 148 items in four categories: machine status, troubleshooting, history and systems configuration. Other features, such as low idle up and an idle start-up function, prevent unnecessary wear on the machine, he adds.
CANADIAN MAGNETISM. Also taking delivery of an LBX 370 model in early 2003 was Don Mills Steel and Metal in Gormley, Ontario.
The 370 LX at Don Mills Steel is fitted with a magnet/grapple attachment with a 20 kW generator package. According to Tony Andrad, who operates the machine at the location in suburban Toronto, "The 370 is very stable. The mag/grapple can handle 3,000 pounds per load, and this machine handles it with ease. It’s got a longer reach than my old machine."
The machine Andrad formerly operated was an LBX 4300 Quantum Link-Belt. "We had good results with that machine with only the usual routine maintenance calls," remarks Nick Gallo, one of the owners of Don Mills Steel and Metal. "We put more than 12,000 hours on it."
"The machine is very smooth and reacts precisely to the controls," says Andrad of the 370 model.
Don Mills Steel and Metal sits on a 50-acre property in Gormley and processes industrial scrap and light materials, as well as obsolete scrap, such as automobile bodies.
In addition to the its 370 LX, the company runs three more Link-Belts—one with a shear and two with magnets—that feed an Al-Jon car crusher and a scrap metals baler.
The applications are typical of those asked of a scrap handler at a versatile scrap recycling facility. After several months on the job, Gallo reports that the machine continues to perform its multiple tasks well with a minimum of downtime.
BUILT TO LAST. LBX Co. has made several modifications and upgrades to its LX Series of material handlers, according to the company. The machines are powered by Isuzu engines with an electronic engine control, which matches the level of fuel injection to the load. This feature is designed to lower overall fuel consumption, reduce engine noise and vibration and produce cleaner emissions.
Each machine in the series is built on a "next-size larger" undercarriage and fitted with a heavy-duty swing motor, giving the machines powerful swing torque. The high-wide undercarriage incorporates heavy-duty components and improves stability, says the company. A chrome-plated boom foot pin mounted in a grease-impregnated brass bushing is designed to provide a durable and long-lasting connection at the highest stress point on the attachment.
"The customer feedback from the initial shipments indicates this machine will be the performance leader in its size class," says Loren Heaney, senior product manager for LBX Co.
Another new feature is the Inte-LX computer control system that monitors hydraulic output and pressures and regulates engine performance for the maximum balance between speed, power and fuel efficiency. The new Auto Power-Up function automatically provides additional power in heavy lifting situations, allowing the operator to focus on the job at hand.
The LX Series also features the Nephron Filtration System, designed to eliminate contaminants down to the size of one micron from the hydraulic system.
This means the hydraulic fluid needs to be changed less often—only every 5,000 hours compared to the 2,000-hour recommendation for some other scrap handling machines. This system reduces maintenance costs while extending the life of the hydraulic system, the company claims.
The operator’s control station has also been modified. The cab has been re-designed to give the operator more room and comfort with easy to use controls. The seat slides independently of the control consoles and the joystick can be tilted to three positions allowing the operator to work in the most comfortable position.
"This new line is substantially smoother and more responsive than our previous series," says Heaney. "The idea was to build a machine that is more comfortable and easier to operate while retaining all the performance characteristics of the previous model."
This story was supplied by LBX Co., Lexington, Ky., www.lbxco.com.
Get curated news on YOUR industry.
Enter your email to receive our newsletters.
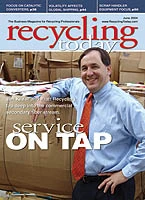
Explore the June 2004 Issue
Check out more from this issue and find your next story to read.
Latest from Recycling Today
- Green Cubes unveils forklift battery line
- Rebar association points to trade turmoil
- LumiCup offers single-use plastic alternative
- European project yields recycled-content ABS
- ICM to host colocated events in Shanghai
- Astera runs into NIMBY concerns in Colorado
- ReMA opposes European efforts seeking export restrictions for recyclables
- Fresh Perspective: Raj Bagaria