The Specialty Steel Industry of North America (SSINA), Washington, says its member companies largely sustained financial losses in 2002 because of unfair trade practices.
Echoing complaints made by carbon steelmakers that eventually resulted in the Section 201 protective tariffs, the SSINA says the North American industry needs help if it is to avoid mill shutdowns, job losses and a loss of market share.
"These latest statistics reflect that for the third consecutive year, specialty steel imports captured more than a quarter of the U.S. market with little variance in the percentages," says SSINA chairman Paul A. Kelly.
LOW-FLYING AEROSPACE |
Stuart Freilich of Universal Metals Corp., Worcester, Mass., sees "trying times" for vacuum quality aerospace nickel alloys and especially for the titanium markets. Freilich’s remarks were read by Barry Hunter of Hunter-BenMet Associates to attendees of the Bureau of International Recycling (BIR) Stainless Steel & Special Alloys Committee meeting in Oslo in late May. The titanium and aerospace alloy processor suggests that 2003 and most of 2004 would be a civil aviation market in which the world’s large high-cost airlines would have to restructure their business models in order to survive. Military spending could potentially be a factor in improving the specialty alloys market. But Freilich concluded: "The revert titanium industry, as we have known it, is history and some American and European titanium producers will not exist in the future as they will not be able to compete with Russian and Chinese producers, who continue to make inroads into these markets." |
A FAMILIAR WORD. Much like the aluminum and carbon steel industries before it, overcapacity is becoming a repeated word within analyses of the stainless steelmaking segment.
"Lackluster demand coupled with expanding worldwide capacity does not bode well for our industry in the short term," says Kelly. "Our goal this year is to ensure our long-term viability by working with our government representatives to take steps toward a rational global market though matching steel production with need and eliminating foreign government subsidies," adds Kelly.
The topic of eliminating government subsidies within the steel industry has been an ongoing source of conversation at meetings held by the Organization for Economic Cooperation and Development (OECD), whose delegates meet in Paris every few months.
Delegates from some 40 nations at the two most recent OECD meetings have agreed to trim some steelmaking capacity and to continue to hash out a draft proposal to eliminate government subsidies.
In the meantime, though, the SSINA says stainless steel imports continue to pour into North America. "Imports of total stainless steel sheet/strip, plate, bar, rod and wire increased 5 percent last year to 534,000 tons," notes SSINA, a figure that is up from the 508,000 tons in 2001. This increased what SSINA calls "import penetration" to 25 percent.
Stainless steelmakers have benefited from Section 201 imports to some extent, but stainless steel bar and rod tariff rates of 15 percent recently dropped to 12 percent while the stainless steel wire tariff dipped from 8 percent to 7 percent. "The principal objective of the program is to give our companies a chance to return to normalcy after years of attack from unfairly priced, high-volume imports that were counter to free market principles," says Kelly. "We have made some progress."
The ongoing difficulties, though, have also been noticeable on the scrap side. In comments accompanying its most recent quarterly report, Metal Management Inc., Chicago, singled out the stainless scrap business as a particularly difficult sector in its recently completed fiscal year. "Our nonferrous business continues to be negatively affected by the generally weak domestic manufacturing sector, particularly the commercial aerospace and stainless steel markets," said Metal Management CEO Albert Cozzi.
A GLOBAL VIEW. Scrap industry executives heard how the current stainless steel situation is affecting different parts of the globe at the Bureau of International Recycling (BIR) Spring Convention held in late May in Oslo.
While overcapacity may be on the minds of North Americans, stainless steel capacity "is still undergoing a phase of expansion" and production continues to increase at more than 7 percent annually, according to Sandro Giuliani of Italy’s Giuliani Metalli-Cronimet Group. Giuliani addressed attendees of the BIR Stainless Steel & Special Alloys Committee meeting in his role as chairman of that committee.
He added that Chinese demand remained the driving force for this production increase, with figures from the country’s Metallurgical Council indicating a 21 percent increase in imports of stainless steel products during the first quarter of this year.
But as of late May, Giuliani pointed to "a drop in orders and a decline in production compared to forecasts" over recent days, adding it was too early to say whether this signalled a shift in market trends or was a short-term reaction to SARS and its affect on Chinese workplaces.
Giuliani also noted that consumption in industrialized countries was "showing no sign of recovery" and that this situation was having an adverse impact on scrap collection, while export restrictions imposed in Russian and the Ukraine were continuing to make scrap harder to find in Western Europe. Since "scrap availability cannot fulfil the stainless steel production requirements," countries depending on scrap imports - such as those in Western Europe - would have to "lower their scrap ratio," he remarked.
Jussi Yli-Niemi, production manager at AvestaPolarit Stainless Oy’s steel melting facility in Finland, provided an update on one of the major new capacity projects in the works. His company’s 1 billion euros investment at Tornio, would result in he described as "the largest single stainless steel production unit in the world." By 2005, on-site melting shop and hot rolling capacity would both be around 1.65 million metric tons per year.
According to Yli-Niemi, the plant could potentially melt up to 600,000 metric tons of stainless steel scrap each year. New dock facilities would enable five or six vessels to be received simultaneously while a railroad connection to Russia would also be "very important," he remarked.
If new high-capacity mills are efficient as hoped, it could provide another tough competitive factor for North American steelmakers to consider. Barry Hunter of New York-based Hunter BenMet Associates told BIR attendees that operators of new and proposed melting facilities would look to secure "major" supply commitments to "assure even their minimum requirement of purchased scrap for a vastly increased production," thus giving North American scrap shippers a market no matter how domestic mills may fare.
Hunter added that processor needs and the availability of prime quality 18/8 scrap should effectively "offset any downward price pressure expressed in LME nickel."
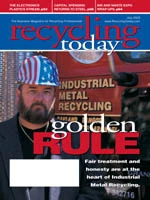
Explore the July 2003 Issue
Check out more from this issue and find your next story to read.
Latest from Recycling Today
- Recycled steel price crosses $500 per ton threshold
- Smithers report looks at PCR plastic’s near-term prospects
- Plastics association quantifies US-EU trade dispute impacts
- Nucor expects slimmer profits in early 2025
- CP Group announces new senior vice president
- APR publishes Design Guide in French
- AmSty recorded first sales of PolyRenew Styrene in 2024
- PRE says EU’s plastic recycling industry at a breaking point