
Each July, experts from ESAB NA, Denton, Texas, attend the Annual Ironworker Instructor Training Program at Washtenaw Community College, Ann Arbor, Michigan. Ironworkers from the U.S. and Canada attend this “train the trainer” event.
One of the classes ESAB conducts focuses on oxy-fuel training, which covers essential safety rules, proper equipment setup, cutting advice and correct shutdown procedures.
I have compiled 13 tips that cover highlights from the oxy-fuel training class:
1. Stand aside – When slowly opening the cylinder valve, always stand to the side of the regulator. In the (highly unlikely) event that the regulator fails, it would be most prone to fail in a manner that directs the force of the gas in the direction of the regulator bonnet and pressure adjustment (PA) knob. Then, open the oxygen cylinder valve all the way, but only open the acetylene valves one-half to one full turn. Open alternate fuel cylinder valves all the way.
2. Leak test – Use a wrench to tighten all metal-to-metal connections, including those between the gas hoses and the torch. Next, leak test these connections by saturating (not wetting, but saturating) them with leak test fluid and watching for growing bubbles. Use approved leak test solution.
3. Right size tip – For the best cut quality, use the right tip size for the metal thickness at hand and adjust gas pressure according to the tip charts for your specific brand of

4. Pressure drop – When using narrow diameter and/or long lengths of hose, consider that the gas pressure will drop by the time it reaches the torch. You can find pressure drop charts in the Victor gas equipment catalog, either on page 12 of the print version or on page 16 of the PDF found at www.esabna.com/shared/documents/litdownloads/65-1501.pdf. (Victor is an ESAB brand of cutting and welding equipment.) Compensate for the pressure drop by increasing the regulator delivery pounds per square inch gauge (PSIG) to ensure back-of-the-torch pressure meets cutting tip requirements.
5. Gauges on the handle – If you consistently cut at long distances from your cylinders, verify the exact pressure drop for your rig. Attach pressure test gauges and note the difference between
6. Brace yourself – In whatever way possible, support your cutting hand with your free hand. A scrap yard worker could accomplish this by bracing his or her free hand on a piece of scrap.
7. Ready to pierce – Before you can pierce steel with the cutting flame, you must ensure the steel has reached its kindling point. While a reddish-yellow color is a good indicator, you can confirm the temperature by slightly depressing the cutting oxygen lever. If the steel forms slag immediately, you can fully depress the lever. If not, release the cutting oxygen lever and maintain the preheat flame a little longer.
8. Spiral out – When piercing, start in the center and work outward toward your cutting path.
9. Torch height – Generally, hold the torch so the inner cones of the acetylene flame are just off the cutting surface. That said,
10. Roll in, roll out – When cutting thicker metal, “roll” the torch into the edge of the metal and then bring it perpendicular. At the end of the cut, roll the torch outward to help ensure a clean sever.
11. Lighting alternate fuels – If you have trouble lighting the torch, hold it against the plate at a 45-degree angle

12. Secured cylinders – It’s all too easy to forget to secure cylinders when moving them around a job site. If you don’t have a cylinder cart handy, try using a reinforcing column instead.
13. Oxygen first, fuel last – Victor recommends shutting off the torch oxygen valve, then closing the torch fuel valve. This technique leak checks both valves every time the torch is shut down. A snap or a pop indicates a leaking oxygen valve, while a small flame at the end of the tip indicates a fuel gas leak.
Those who like to learn via video can check out the winner of the I-beam plasma cutting contest at www.youtube.com/watch?v=21u2TxC6E1U.
For companies that want to host a training class, ESAB’s Victor brand offers an instructional DVD, which includes 36 minutes of visual instruction, an instructor
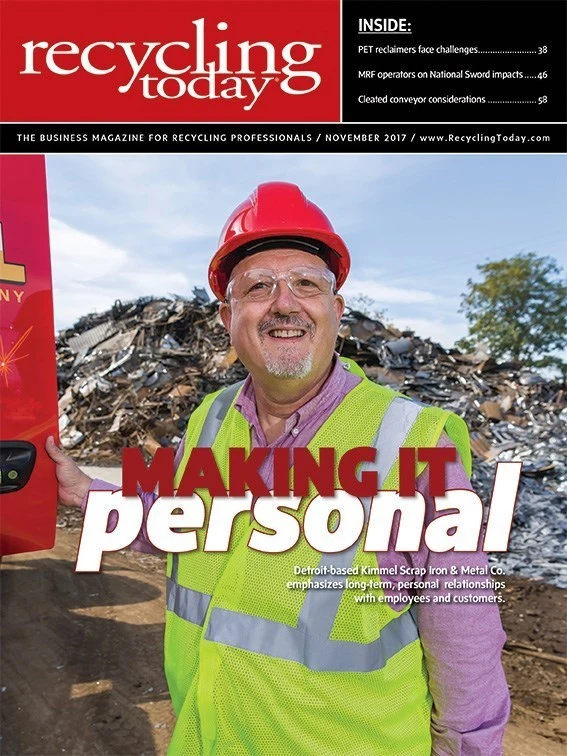
Explore the November 2017 Issue
Check out more from this issue and find your next story to read.
Latest from Recycling Today
- AF&PA report shows decrease in packaging paper shipments
- GreenMantra names new CEO
- Agilyx says Styrenyx technology reduces carbon footprint in styrene production
- SABIC’s Trucircle PE used for greenhouse roofing
- Hydro to add wire rod casthouse in Norway
- Hindalco to invest in copper, aluminum business in India
- Recycled steel price crosses $500 per ton threshold
- Smithers report looks at PCR plastic’s near-term prospects