
1. Unmatched reliability
“In the 20-plus years that we have been running Bollegraaf balers, we have found them to be consistently dependable. I recently purchased my sixth one.” – Rod Nicolls, Vice President Operations, Urban Impact
“The engineering, construction and performance on the Bollegraaf is top of the line—the Cadillac of balers. Van Dyk’s parts and service team is always there when we need them.” – Frank Sánchez, Vice President, Town Recycling LLC
“The reliability on these machines really sets them apart. Also, it takes up less space than a two-ram baler, which was attractive considering our plant’s footprint.” – Anonymous MRF Manager
2. Pure speed
“The first time I saw a Bollegraaf operate, I was amazed by how fast the baling cycle was. Material loads on top of the flap while the previous load is being baled, and the feed conveyor only stops for a few seconds in between. With my old baler, I was used to waiting 45 seconds for the conveyor to restart while it went through its cycle.” – Nicolls
“It continuously bales fiber with very few maintenance stops.” – Anonymous MRF Manager
3. Low maintenance
“Our baler is now 23 years old, and it is operating at a level most balers do when they are only 10 years old. It keeps on working and requires much less maintenance than other balers we have owned. Other single-ram, multiuse balers in the marketplace did not seem to have the same reliability.” – Kevin Duncombe, President, Western Pacific Pulp & Paper
“Our HBC120S truly is automatic with next to no maintenance. The baler easily makes up to 250 bales per day, and we’ve seen it produce up to 400 bales per day with no operator. The baler is exceptional and an integral part of our high throughput and productivity.” – Mike Ferro, General Manager, City Carting/WTI MRF
4. Massive capacity
“We’re a one-baler facility with a smaller footprint. We can’t increase our footprint, but we can increase our speed and capacity. With the HBC140, we can run the same tonnage as a facility twice our size. Right off the bat, it added 25 percent to our capacity with no signs of slowing down. Most of the time, we can’t feed it fast enough.” – Scott Jenkins, President, EFI Recycling
“We have an HBC120 for containers and an HBC140 for fiber. Both exceed our expectations of throughput and uptime for our 50-tph system.” – Brian Dubis, MRF Operations Manager, RIRRC
5. Save on costs
“The biggest factor in our decision to purchase a Bollegraaf was the lower cost to operate it compared to a two-ram baler. It has delivered on reliability and costs.” – Duncombe
“After considering the production increase and potential energy savings, we decided to switch from a ‘ram-and-cram’ type baler to a Bollegraaf. The pre-press flap allowed us to bale without shearing, so maintenance costs improved, and downtime was significantly reduced.” – Joe DiNardi, President, Colgate Paper Stock
“The machine doesn’t require an operator, has a power pack that is one-third the size of comparable two-ram machines with much fewer moving parts, and the ram is on rollers, so the floor doesn’t wear out.” – Ferro
6. The unique pre-press flap makes even bales
“The single-ram setup uses a flap versus a shear and uses a fraction of the energy still producing bales that are heavier and easier to store and load.” – Ferro
“The 120S model packs a lot better than our previous baler with a lot less downtime.” – Dale Schmidt, Recycle Manager, Loraas Recycle
“It produces dense, symmetrical bales that stack well. This makes them perfect for export.” – Michael “Recycle” Benedetto, President, TFC Recycling
7. Unrivaled ROI
“Considering the high productivity and low marginal cost per ton, I knew we could save money and have a huge increase in our capacity. That gives us a competitive advantage.” – Nicolls
“The increase in capacity far outweighed the upfront costs. The technological advancements on the HBC140, particularly the hydraulic system, wire tie system and safety features, are just tremendous.” – Jenkins

8. Robust or bust
“It’s a very durable machine. We have only had to do routine maintenance and have had no serious breakdowns.” – Schmidt
“The five independent wire setup on the Bollegraaf allows you to keep working through any wire-tie issues, whereas other machines can easily shut you down if there is wire failure. If you are serious about throughput and quality, get a Bollegraaf.” – Ferro
9. Any part, anytime
“Despite us being in Canada, parts are always readily available. We generally receive parts by the next morning, so we don’t have to tie our cash up in a huge spare parts inventory.” – Nicolls
“Van Dyk by far has the best spare parts operation. We’ve called at night for them to send out parts and they have. They stock parts I might never need, but I know they’re there.” – Jenkins
10. Integrity of service
“Anything my maintenance team is struggling with can be helped by the support we get from Van Dyk. We were able to learn how to maintain and optimize our balers through interactions with the Van Dyk service department, both in person, but more frequently, via their free, 24-hour phone service.” – Nicolls
“There are many things that set Bollegraaf balers apart from the competition, but in my opinion, it is the organization as a whole. From sales to service and parts to ownership, Van Dyk stands behind their equipment and provides a level of support that is hard to find in the marketplace.” – Duncombe
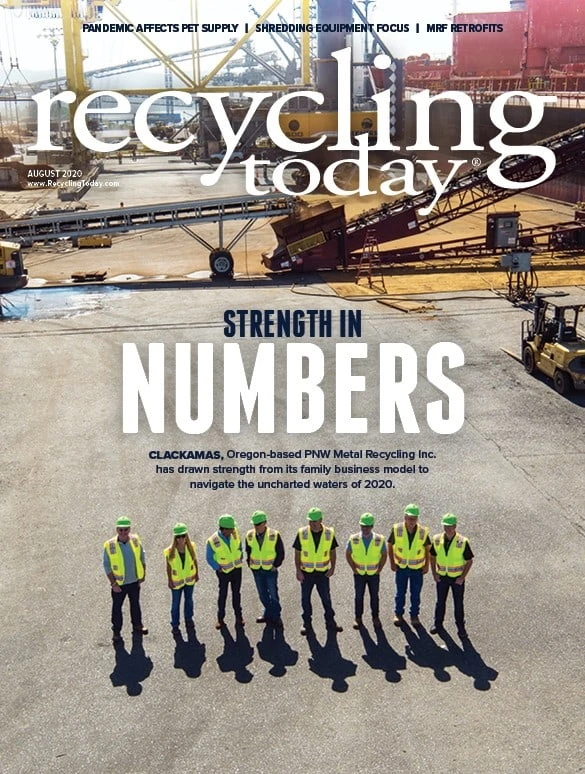
Explore the August 2020 Issue
Check out more from this issue and find your next story to read.
Latest from Recycling Today
- ReMA opposes European efforts seeking export restrictions for recyclables
- Fresh Perspective: Raj Bagaria
- Saica announces plans for second US site
- Update: Novelis produces first aluminum coil made fully from recycled end-of-life automotive scrap
- Aimplas doubles online course offerings
- Radius to be acquired by Toyota subsidiary
- Algoma EAF to start in April
- Erema sees strong demand for high-volume PET systems