When City Carton Recycling upgraded the sorting equipment at its Cedar Rapids, Iowa, facility in 2006, one of the considerations included optical sorting equipment. But at that time, making an investment of $300,000 to $500,000 in this kind of equipment was not something Northern Division Manager Chris Ockenfels was ready to entertain. Chris recalls that, at that time, he did not view optical sorting as a proven technology for separating fiber from plastic. The company used employees to hand sort material instead.
Then, Chris began crunching the numbers. A few years later, when the company renewed its single-stream contract, it contacted its equipment supplier, Machinex, of Plessisville, Quebec, Canada. Chris was ready to get on board with the idea of optical sorting.
DECISION TIME
“We looked at the cost and wages and, after investigating it further, we found a three-to-four-year payback on wages saved alone,” Chris recalls. “We renewed our contract for single-stream recycling and were able to justify spending the money to use the optical system as a quality control check behind our screening technology to ensure a cleaner end product,” he adds.
Alan Schumacher, facility manager at the Cedar Rapids facility, says he was always in favor of installing optical sorting equipment. “Putting our collective minds together, we realized the obvious: We would be better served to go with the optical sorter to enhance our variable labor expense and to provide a much more efficient way to separate the incoming dual stream that we work on.”
Still, based on the volume that City Carton Recycling was taking in, it wasn’t an easy decision.
City Carton Recycling President Andy Ockenfels determined the Cedar Rapids location services less than 150,000 people and, thus, the material intake would be limited.
The limited incoming material volume meant it would take longer to see a return on investment than in a larger metropolitan area. “For bigger cities, it should be a no brainer,” Andy says.
The decision to invest in the technology in a smaller market has paid off over time. While it would take three to four years for the investment to pay off, Andy says he wants to be in business for many years to come, so he is fine with that.
“We have been happy with the optical sort system we used in our machine to improve the efficiencies and quality of material,” says Andy.
INCREASED EFFICIENCIES
The optical sorting equipment increased efficiency for City Carton Recycling by eliminating the need for four manual sorting positions as well as by increasing the speed at which material is sorted. Schumacher says he noticed a difference right away. “There was a very significant increase in speed,” he says.
According to Schumacher, the Cedar Rapids facility processes an average of 13 tons of material per machine hour and employs 11 people to operate the whole system. Quality control (hand-sorting) staff was reduced from six employees to two employees when the new optical sorting system was in place.
Chris Hawn, the U.S. sales manager for Canada-based Machinex, says optical sorting equipment allows recyclers to focus on their targeted commodity. “You can do a great job on a recovery rate target that you might be missing with manual labor,” he says.
In City Carton’s case, optical sorting is used to separate fibers from containers. The material first goes through three star-wheel screens before it gets to the optical sorter. This step minimizes the amount of fiber that is left.
Schumacher describes the optical sorter as the last line of defense to separate plastic containers from the fiber.
A final manual sort completes the process.
City Carton accepts all grades of fiber, plastic bottles Nos. 1 through 7 and aluminum and steel cans. “Our goal was to separate, after our third star sort, the remaining fibers from the plastic,” says Schumacher. “That way we would have a diversion for all non-fiber materials that would enhance our opportunity to provide a quality hand sort of ferrous and nonferrous metals out of the remaining No. 1 to No. 7 plastic stream.”
CAREFUL CONSIDERATION |
Alan Schumacher, facility manager at the Cedar Rapids, Iowa, City Carton Recycling material recovery facility, offers the following recommendations for companies considering optical sorting equipment: 1. Make sure not only of your current volumes but of your projected volumes. By doing this, you will know how big of a system you need, not only now but in the future. 2. Do not go with the first vendor that comes through the door. Take the time to research, visit and observe before you pull the trigger on a big capital investment. You want to make sure you choose an equipment vendor who will be there with you for the long-run. 3. Have a strong preventive maintenance program to maintain this large capital investment. |
QUALITY IMPROVEMENTS
According to Schumacher, that design has enabled City Carton to create end products that exceed industry standards. “When we sell our material we receive minimal if any quality complaints,” he says.
Further separation means higher grade material and more profits that can be gained from processed material.
“Our corporate officers are really good visionaries in that they recognized we needed to develop a good quality recycling stream of plastics because of the value add that [material] provides for our P&L (profit and loss),” Schumacher says.
FURTHER INVESTMENT
City Carton has been so pleased with the results of the optical sorter that it has purchased a second optical sort system for its Iowa City, Iowa location.
“It will be used for source separating plastic vs. the first system, which was for efficiency and quality,” Andy says of the Iowa City optical sorting installation.
“City Carton is a great operation,” Hawn observes. “It has obviously proven itself to the extent that it is investing more at the current time to move forward with current optics.”
Schumacher and City Carton recognize the importance of investing in new technologies in order to remain successful in the recycling industry. “The opportunity to invest in new technologies to promote efficiencies within our organization is tantamount to our success,” he says.
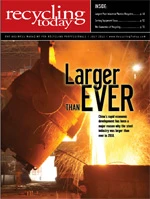
Explore the July 2011 Issue
Check out more from this issue and find your next story to read.
Latest from Recycling Today
- P+PB adds new board members
- BlueScope, BHP & Rio Tinto select site for electric smelting furnace pilot plant
- Magnomer joins Canada Plastics Pact
- Out of touch with reality
- Electra names new CFO
- WM of Pennsylvania awarded RNG vehicle funding
- Nucor receives West Virginia funding assist
- Ferrous market ends 2024 in familiar rut