Clayton County Recycling in the heart of Iowa has come a long way from its start as an auto salvage yard, says owner Fred Runde. With more than 75 employees today and a variety of modern processing equipment, the multi-site scrap recycling operation continues to be profitable by recovering the most metal possible from its 80/104 shredder with the help of a new compact FinesSort Jr. from Eriez, Erie, Pa.
Clayton County Recycling actually began in 1988 in Belmont, Wis., as a one-yard auto scrap salvage operation. Runde expanded the company in 1994 by purchasing 10 acres of cornfield adjacent to a railroad line in rural Monona, Iowa. Today, the company owns feeder yards in the Wisconsin cities of Madison, Holmen and Wonewoc along with the original yard in Belmont and its shredder yard in Monona.
The feeder yards, Runde says, play a vital role in supplying suitable scrap, consisting of old car bodies and parts, obsolete appliances and outdated agricultural equipment, to process through the auto shredder. The feeder yards are strategically located within 80 to 100 miles of the main shredder operation in Monona, which has now become the hub of Clayton County's business.
“Our shredder went online in 2006, allowing us to become more than a shearing, sorting and baling yard here in Monona,” Runde says. “At that time, we installed one eddy current separator that gave us the ability to recover nonferrous metals. That was great, but we still needed something else for fines 1-inch sized and smaller. We ran our fines over the same eddy current at the end of the day when regular production was finished but found after running them twice, they still were not getting all the metal out.
That’s when Runde contacted Eriez, an Erie, Pa.-based company known for designing individual units or complete systems for the recycling industry.
After some analysis and investigation into Clayton County Recycling’s operation, engineers developed a smaller scale metal recovery system to handle fines measuring 1 inch in size and smaller.
Dubbed the FinesSort Jr., it was installed at Clayton County Recycling in the fall of 2009, according to Runde. The company now processes up to 30 tons of fluff per hour, with the fines going direct to the FinesSort Jr., and the remainder of the fluff going to the original eddy-current separator.
"We ran our fines over the same eddy current at the end of the day when regular production was finished but found that even after running them twice, we still were not getting all the metal out.”
– Fred Runde, Clayton County Recycling
COMPLEMENTARY PARTNERS
Typically, scrap yard operators have been concerned with reclaiming nonferrous metals of larger sizes. The smaller metals that passed through the initial screening process usually have been discarded and sent to landfills.
This smaller material, referred to as fines, represents up to 40 percent of the original total flow. Within the fines, generally less than 5 percent is recyclable metal, depending on the mix of material being shredded. Although 5 percent of the fines or just 1 percent of the total stream might seem insignificant, reclaiming these valuable metals can be worth hundreds of thousands of dollars annually for shredder yard operators.
A number of larger recycling centers have installed Eriez’ FinesSort multi-stage metal recovery system, which contains a vibratory feeder, rare earth pulley, rare earth drum and permanent magnetic eddy-current separator.
Eriez engineered the FinesSort Jr. for recycling operators like Clayton County, which need a smaller scale system to recover fine metal particles profitability.
Essentially, the FinesSort Jr. is built with a 24-inch AIP (axial interpole per manent) pulley and a 60-inch Xtreme eddy current separator.
This design helped Clayton County to recover 1-inch and smaller fines in a single pass while using an eddy current separator to recover larger particles, Runde says of the company’s downstream system.
PROFITABLE PROCESSING
At Clayton County Recycling, scrap metal is first routed to the 2,500-horsepower 80/104 auto shredder built by American Pulverizer, St. Louis. The shredder is capable of handling 85 tons per hour, or the equivalent of 700 tons per day, according to Runde. The nonferrous material trapped in the fluff is then conveyed into a tumble-back conveyor, which helps to meter the pulverized material into a 20-foot-long by 6-foot-diameter trommel with screens.
As the material tumbles through the screens of the trommel, it is diverted to separate belt conveyors. Material 1 inch in size or larger heads to the original eddy-current separator, while smaller material heads into the FinesSort Jr.
The product extracted from the recovered fines is so clean that Runde says he is able to get a premium price for the metal. He also points out that his crew has rerun the rejected material and cannot find a significant volume of metal on the second pass.
That’s good for Clayton County, Runde points out, knowing it isn’t sending an appreciable amount of metal, or profit, to the landfill.
“The FinesSort Jr. was specifically installed to recover the 1-inch and smaller fines, aluminum, brass and copper,” Runde says. “The goal was better recovery of the metal content, especially since it contains a lot of dirt.
“This system got us a cleaner product and more metal than the original eddy ever could,” he continues. “We are very pleased with the FinesSort Jr. It does a great job.”
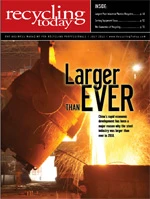
Explore the July 2011 Issue
Check out more from this issue and find your next story to read.
Latest from Recycling Today
- Fitch Ratings sees reasons for steel optimism in 2025
- P+PB adds new board members
- BlueScope, BHP & Rio Tinto select site for electric smelting furnace pilot plant
- Magnomer joins Canada Plastics Pact
- Out of touch with reality
- Electra names new CFO
- WM of Pennsylvania awarded RNG vehicle funding
- Nucor receives West Virginia funding assist