Every day in the United States more than 10,000 workers are injured on the job, with 14 of those injuries resulting in death.
While the sheer number of those injuries is staggering, the financial impact to employers is crippling. An annual study conducted by the Liberty Mutual Research Institute for Safety in 2010 revealed the direct cost to employers from injuries in 2008 was $53.42 billion. Indirect costs were between $80 billion to $200 billion annually.
A key component to protecting both the safety of your employees and the profitability of your company can be the creation of a personal protection equipment (PPE) maintenance program.
A PPE maintenance program provides a method to periodically check safety protection equipment to ensure its functionality.
SELECTING A PPE MANAGER
The first step in creating a plan is identifying how you would like to manage your PPE maintenance program.
Three models for management are:
1. Employees monitoring their own equipment;
2. A central person maintaining all of the equipment; or
3. A combination of the two.
To determine which of these management plans will be most effective for your company you must consider how PPE is currently treated in your company.
If your employees are assigned a set of PPE and that equipment stays in their possession, it is best to have the employee monitor his or her equipment. If all of your PPE is turned into a central location at the end of the work day, then it is best to have one person in charge of PPE maintenance. If your company features a combination of these policies, then I would suggest the implementation of a policy that combines the two management processes.
For this article, we will assume the workplace involves a joint maintenance program. (If your workplace wants to institute only one aspect of the program, simply strip out the portion that does not apply to your management style.)
TRAINING ON MAINTAINING
Once you have chosen a PPE maintenance management style, it is necessary to craft a training program for the upkeep of equipment. To create this program, you must first know the maintenance that is required for each type of PPE. (For a listing of the typical maintenance required for the common PPE used in recycling, please see the online sidebar, “Maintenance Checklist,” that accompanies this feature.)
Once you have determined the basic details of maintaining your company’s PPE, it is time to create your training program.
To begin, create a list of the PPE equipment that is specific to your organization and show your employees how to perform each required maintenance task in a group training meeting. After the meetings, have your employees sign off on a training log, indicating that they attended and understand the training provided. (If you want a form, please e-mail me at mrich@safetyservicescompany.com, and I will gladly provide it for free.)
In addition to this large group training, I recommend including a training refresher on a specific topic each month or two. This information can be provided with your employees’ paychecks. Each of these refresher training documents should include a place for the employee’s signature, so they can be returned and documented.
CREATING A TRACKING POLICY
Now that we have crafted a training plan to accompany our PPE maintenance program, we must create a method to track proper PPE maintenance.
Maintenance Checklist |
Typical maintenance requirements for the common PPE used in recycling is available at www.RecyclingToday.com/July-2011-PPE-Maintenance.aspx. |
Since I have decided to use the two-pronged approach in this article, two separate log books are required. The first log book will be for employees, with a vertical row featuring each employee’s name and a horizontal row featuring the date. For ease of use, I recommend keeping this book near employee lockers or the time clock.
When an employee starts each day, he or she will be responsible for checking the condition of his or her PPE, performing any required routine maintenance and signing off in the appropriate box.
The second log book is for equipment that employees share or that is not used often. The easiest way to complete this book is to number each piece of PPE with a permanent marker and place the corresponding number in the vertical rows of an Excel file or log book. The horizontal rows will represent dates.
After creating the log, the person in charge of maintenance will sign off on the maintenance of the equipment each day.
You can purchase log books at most office supply stores or you can print off blank Excel sheets, punch them with a three-hole punch and place the sheets a three-ring binder. If you want to take the green route, you can create an electronic log book using Excel or a similar spreadsheet program.
Log books allow you to record the maintenance of your equipment, have a record showing your company was not at fault in case of equipment failure and constantly remind your employees to properly use their PPE.
By implementing this simple policy you can prevent PPE failure and extend the life of your PPE.
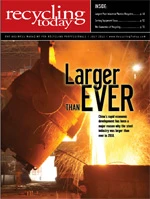
Explore the July 2011 Issue
Check out more from this issue and find your next story to read.
Latest from Recycling Today
- Magnomer joins Canada Plastics Pact
- Electra names new CFO
- WM of Pennsylvania awarded RNG vehicle funding
- Nucor receives West Virginia funding assist
- Ferrous market ends 2024 in familiar rut
- Aqua Metals secures $1.5M loan, reports operational strides
- AF&PA urges veto of NY bill
- Aluminum Association includes recycling among 2025 policy priorities