With four recycling yards and a transportation fleet to operate for the Southeast region of Fort Wayne, Ind.-based OmniSource Corp., making sound equipment decisions is a big part of the job for Regional Manager Mike Winkler. Luckily, when the scrap handler at the company’s shredding facility in Spartanburg, S.C., was due for an upgrade, Winkler had no trouble getting advice he could trust.
Just a phone call away, he found Scott Gibble, the northern Indiana division manager for OmniSource’s Midwest region. In 2010, Gibble took delivery of a new 840 M material handler, a new model that Stanley, N.C.-based Sennebogen had developed specifically to suit his requirements. Since then, Sennebogen has delivered several 840 M scrap handlers to OmniSource sites in the Midwest.
Gibble recommended the 840 M to his colleague, and the material handler also had the endorsement of OmniSource’s Vice President of Ferrous Operations Bob Brewer. Brewer worked closely with Sennebogen factory representatives and his distributor as the specifications for the 840 M were developed.
But Winkler’s choice was not an automatic one.
“We do like to standardize when we can,” he says. “Scott told me this was a reliable, efficient machine. Our own purchase decision for Spartanburg, though, was simply based on the operating cost that the machine demonstrated at the Midwest plants.”
SUPPORTING ROLE
Winkler conducted his own due diligence before placing an order with ASC Construction Equipment, the Sennebogen dealer based in Charlotte, N.C. He was already familiar with the staff at ASC, who also supply the Volvo loaders used at OmniSource sites in the Southeast. Winkler says he was impressed by the low fuel and maintenance costs reported by OmniSource’s Midwest facilities. Then he paid a visit to the head office of Sennebogen LLC, which recently relocated to a new facility the company built just outside of Charlotte.
“We have our own mechanics to service the equipment,” Winkler says, “but parts availability was big time for us. And this parts facility just blew us away.” The visit also gave Winkler a chance to get personal with the 123,000-pound machine. “We all got a chance to get in it and run it while we were there,” he says. “It was very impressive.”
Opened in October 2009, the 54,000-square-foot Sennebogen facility combines sales and administrative offices, warehousing for a comprehensive parts inventory and a dedicated training section with multimedia-equipped classrooms and a large indoor bay that allows visitors to view the equipment from above and below.
EVALUATION IN PROGRESS
“It’s in a stationary application while it feeds the shredder, but I’m rotating operators through it to get different opinions on how it handles. The feedback so far has been all positive. After a couple of weeks, we will try it out loading trucks.”
– Mike Winkler, OmniSource
The rubber-tired 840 M provides excellent mobility on the paved Spartanburg yard. The material handler’s hydraulic elevating cab and the visibility it allows has earned accolades from its operators, Winkler says. The loading height of the shredder’s conveyor is about 14 feet. The cab of the 840 M can raise the operator to a seated eye level of 19 feet, providing a clear view of the target and the surrounding area.
In addition, he says he suspects the material handler will be easier to drive around the yard. “We expect this machine will be a lot easier to move around than others we have had,” Winkler says. “The rubber tires will run faster on the concrete and cause less damage.”
The shredder facility receives material from feeder sites OmniSource operates in the region. To keep the shredder operating at capacity, the 840 M is fitted with a 2-yard scrap grapple. Winkler anticipates that he will add a smaller grapple for loading trucks in addition to a cleanup magnet to sweep the yard.
GOING THE DISTANCE
Gibble says the 840 M evolved through specific requirements for the processing equipment used at its various facilities OmniSource set down for Sennebogen to match. “What initially attracted us to Sennebogen was that we had a special need for a rubber-tired material handler of a particular size,” he says. “When we were [specifying] machines, the 840 M series wasn’t even in the Sennebogen product line yet. We tried the 835 M, and it was too small for our needs; we tried the 850 M, and it was too big.”
“What initially attracted us to Sennebogen was that we had a special need for a rubber-tired material handler of a particular size.”
– Scott Gibble, OmniSource
OmniSource also had clear ideas on the kind of performance the business required: a machine that would be a little quicker and more mobile than existing units and that could handle attachments in a specified size range. That’s when Tim Kreider of Brandeis Machinery & Supply, based in Louisville, Ky., became involved. Brandeis Machinery & Supply is the Sennebogen dealer serving Indiana and Kentucky.
“The dialogue between our company and Sennebogen was largely driven by Tim,” Gibble says. “Brandeis deserves a lot of credit for listening to what we needed for our application and then bringing the manufacturer and product to us.”
Constantino Lannes, president of Sennebogen LLC, became personally involved with OmniSource at that point. “The new machine was specially created to serve the increased demands of high-performance operations like
OmniSource,” Lannes says. “Our engineers took the best features of the 835 M and 850 M models and created the new 840 M—its specifications and performance is a direct response to customer requirements,” he adds.
CUSTOM CRAFTED
“It has proven to be a very good performer,” says OmniSource’s Brewer. “It’s a fast machine with ample reach and great cycle times that can drive the attachments in our application. It’s a very stable machine with a low center of gravity and a wide stance—the perfect fit for our special needs.”
OmniSource facilities in Indiana, Michigan and Ohio are already standardizing to the Sennebogen 840 M, and now Winkler is transitioning the Southeast region to the machines custom-built to the company’s applications.
With its Sennebogen fleet expanding, Brewer stresses that the after-purchase service support always figures prominently in OmniSource management’s equipment decisions. “It doesn’t help our uptime or bottom line if we have to wait for someone to drive three or four hours to service our equipment. Good distributor support in the states where the machines are going is a major factor in going with the Sennebogen product line. Since we acquired our 840 M units, our distributors—Brandeis in Indiana, Gibson Machinery in Ohio [and] ASC in South Carolina—have done a great job supporting us in a timely manner.”
Get curated news on YOUR industry.
Enter your email to receive our newsletters.
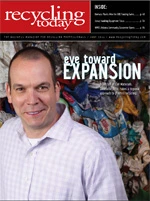
Explore the June 2011 Issue
Check out more from this issue and find your next story to read.
Latest from Recycling Today
- AF&PA report shows decrease in packaging paper shipments
- GreenMantra names new CEO
- Agilyx says Styrenyx technology reduces carbon footprint in styrene production
- SABIC’s Trucircle PE used for greenhouse roofing
- Hydro to add wire rod casthouse in Norway
- Hindalco to invest in copper, aluminum business in India
- Recycled steel price crosses $500 per ton threshold
- Smithers report looks at PCR plastic’s near-term prospects