Houston-based Waste Management Inc. (WMI) opened its Surprise, Ariz., single-stream material recovery facility (MRF), known as the Arizona Community Ecocenter, in February 2011.
By retooling its existing MRFs and constructing new facilities like the Arizona Community Ecocenter based on its experience at a MRF operator, WMI hopes to nearly triple the amount of recyclables it recovers from 8 million tons to more than 20 million tons by 2020.
During the official opening of the Surprise MRF, Duane Woods, WMI senior vice president, said, “WMI’s objective is to extract more value from the materials we manage. The Arizona Community Ecocenter will help us reach our goal by making the recycling process more efficient.”
ALL TOGETHER NOW
While maintaining some of the characteristics of WMI’s other MRFs, the company’s Surprise MRF stands apart because it features a “campus” that includes a landfill and space for a waste-to-energy facility, which the company says it may locate at the site. The MRF also includes a 1,200-square-foot education center that features videos, murals and interactive tools that show the public how WMI extracts value from the material it processes. While the company has not yet determined the location of the waste-to-energy plant, it is looking for ways to integrate the proposed project with the MRF and landfill.
Carrie Galvan, WMI director of recycling operations, says the MRF’s proximity to the landfill is ideal because it reduces the cost of transporting residue. “We also are able to mine more material from our transfer stations and pull out valuable commodities that normally would have gone to the landfill,” she says. “We also use some of our glass for alternative daily cover (ADC) at the landfill.”
WMI executives say the Arizona Community Ecocenter is the company’s most advanced facility, featuring what the company claims is the latest technology.
The 65,000-square-foot facility has the capacity to process more than 10,000 tons of material per month (or 25 to 30 tons per hour)—nearly 2.5 times the processing capacity of WMI’s previous facility in the area, which closed when the new MRF opened.
The Arizona Community Ecocenter costs more than $20 million to build and is expected to create from 30 to 40 permanent jobs.
Galvan says the MRF, which is still in the startup phase, has not reached its rated capacity of 10,000 tons per month. However, she says WMI expects to see incremental increases in the amount of material collected and processed as the general economy improves.
The facility’s rural location corresponds with the company’s “hub-and-spoke” approach to collecting and processing recyclables, Galvan says. The MRF takes in recyclables from WMI transfer stations in the surrounding area.
"We are constantly striving to optimize our efficiency by utilizing advances in recycling technology. This facility showcases the latest single-stream recycling equipment, which will ultimately allow us to offer more recycling programs to our customers."
– Pat DeReuda, president, Waste Management Recycle America
The Arizona Community Ecocenter accepts all grades of fiber, plastics No. 1 through No. 7, mixed rigid plastics, tin cans, scrap metal, glass and aluminum. “We have a drop-off collection for batteries, cell phones and aerosol cans,” Galvan says. The facility also holds community collection events for items such as computers, she adds.
According to WMI, the collected material is processed using some of the most sophisticated equipment available, including magnets, eddy currents, sorting screens and optical scanners, among other equipment, to maximize recovery and to increase automation.
EQUIPPED FOR THE JOB
During the Arizona Community Ecocenter’s grand opening, Pat DeRueda, president of Waste Management Recycle America, said, “We are constantly striving to optimize our efficiency by utilizing advances in recycling technology. This facility showcases the latest single-stream recycling equipment, which will ultimately allow us to offer more recycling programs to our customers.”
The MRF’s eddy current is one of the largest available today, Galvan says. Two balers—one from Harris, Tyrone, Ga., and a new MacPresse system from Sierra International Machinery, Bakersfield, Calif.—give the MRF the flexibility to process single-stream material as well as other recyclables.
Four Titech optical sorters from Van Dyk Baler Corp., Stamford, Conn., use sensors to determine the reflectivity of each object, calculating its speed and location on the conveyor belt, before dispersing a jet of air to separate the object from the rest of the material. The Titech sorters can be programmed to separate certain plastics, paper and other fibers from the material stream, Galvan notes.
Electromagnets extract tin-plated cans and other ferrous metals from the material on the conveyor belts and drop them directly into storage bunkers.
The MRF also incorporates rotating disks to separate OCC (old corrugated containers) from other materials, and a triple-deck screen is designed to further sort OCC from other fibrous materials.
The processing line also includes a vacuum system designed to help extract plastic film from the other recyclables.
GRAPPLING WITH QUALITY
One of the foremost challenges for recyclers, especially among those processors that have embraced single-stream processing, can be meeting consumers’ quality specifications.
To address this issue, Galvan says WMI has included an on-site education center at the Arizona Community Ecocenter to help educate residents on acceptable recyclables as well as the recycling process.
“Waste Management has really focused in on education as a proactive measure to reduce contamination,” she says. “At our new MRF in Surprise, we built an on-site education center. The center is open to the public and can entertain groups of all ages. We have live feeds of the MRF inside the education center along with several interactive displays. We have approximately 200-plus people from all over the valley who visit our education center every month.”
Galvan adds, “We participate in several community events to encourage recycling and sponsor several collection events annually.”
The MRF grades inbound loads for quality in an effort to reduce contamination, she says. “This process allows us to communicate back to our customers if there is heavy contamination in the recycling stream. We share photos of the contamination and partner with our customers to improve the quality of the inbound material.”
She adds that despite the facility’s efforts at education, concerns about contaminated loads remain.
The MRF’s high degree of automation, Galvan says, means the processing system’s conveyor line can be slowed down or sped up, depending on the quality of the material being processed. This capability, she says, allows the MRF to invest more time in cleaning up loads that don’t meet its specifications.
Galvan says staffing is WMI’s biggest challenge that contributes to the quality of the recyclable commodities the Arizona Community Ecocenter produces. “If you turn over the staff, it affects the quality of the material,” she says. Therefore, Gavin adds, “We are focused on employee engagement and retaining our employees.”
Get curated news on YOUR industry.
Enter your email to receive our newsletters.
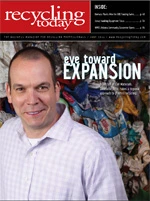
Explore the June 2011 Issue
Check out more from this issue and find your next story to read.
Latest from Recycling Today
- AF&PA report shows decrease in packaging paper shipments
- GreenMantra names new CEO
- Agilyx says Styrenyx technology reduces carbon footprint in styrene production
- SABIC’s Trucircle PE used for greenhouse roofing
- Hydro to add wire rod casthouse in Norway
- Hindalco to invest in copper, aluminum business in India
- Recycled steel price crosses $500 per ton threshold
- Smithers report looks at PCR plastic’s near-term prospects