CBI READY TO OFFER ANNIHILATOR
Continental Biomass Industries (CBI), Newton, N.H., has announced that its Annihilator shredder (formerly dubbed the MOAS—Mother of All Shredders) has now completed its testing phase and is ready for demonstration.
The 20,000-pound machine was unveiled in June at WasteExpo in New Orleans. The unit is designed as a primary shredder for all types of C&D debris and additional municipal solid waste streams.
According to CBI, the unit features a forged, high-strength steel rotor that is 10 feet, 4 inches long, 6 inches thick, and 42 inches in diameter. The cutting gap on the 8,000-pound anvil adjusts instantaneously to accommodate varying feedstock and to meet desired end product size requirements.
The Annihilator comes in both stationary and mobile configurations with a choice of 600 and 1,000 hp electric or diesel engines. Those seeking more information or wishing to arrange a demo can contact CBI at (603) 382-0556.
PETERSON OFFERS HORIZONTAL RECYCLER
Peterson Pacific Corp., Eugene, Ore., has introduced the new HC 4700 horizontal recycler designed for high-volume producers with demanding end product specifications.
The HC 4700 horizontal recycler with a 630 hp motor is a new mid-range model in the Peterson recycler lineup. It utilizes the Peterson three-stage grinding process with an up-turning rotor that helps to produce materials to exact specifications, according to the company.
BULLDOG UNLEASHED ON DEMO MARKET |
Victor Equipment Co., St. Louis, is now marketing its Bulldog HC 1100C Series Torches for the demolition and scrap recycling markets. According to the company, the Bulldog features a lightweight, maneuverable design, yet is also a durable, fast-cutting LP propane/natural gas torch. The Bulldog features heavy-duty brass tube supports that provide rigidity despite the sleek, low-profile head design. The torch can cut through material up to 14-inches thick. Four models of the Bulldog are available, with 36-inch and 48-inch torches that can be selected with either 75-degree or 90-degree heads. Victor Equipment’s product designers say the Bulldog’s sleek profile allows it to "move effortlessly in, out and around tight places, eliminating operator fatigue." |
The first fragmentation step occurs at the up-cutting rotor. The rotor draws material into the grinding chamber in an way that minimizes wear on the bit, according to a Peterson Pacific news release. The anvil is positioned for optimum sizing and production to provide the second stage in the sizing process. The final sizing stage takes place at the large grate area.
The horizontal recycler’s quick-change multiple-grate system allows users to easily customize grate configurations to produce a wide array of finished materials, according to the company, with minimal regrinding.
Peterson Pacific’s patented Impact Release System minimizes damage from contaminants in the grinding chamber resulting in more uptime, according to the company. "Peterson’s Smart Control Panel helps maximize throughput for more production each day," the company news release states.
All finished materials are discharged on a continuous conveyor, which reduces material spillage, meaning less clean up.
LIPPMANN INTROS "PRIME MOVER"
Lippmann-Milwaukee Inc., Cudahy, Wis., has introduced the 4818 Prime Mover crushing and screening plant.
The company bills the new model as, "an economical, high-volume portable impact crushing and screening plant that offers [recycled and primary] aggregate producers multi-product capabilities and precise material sizing in a self-contained, easily transportable unit designed for quick set-up."
The Prime Mover includes Lippmann’s 4248 horizontal shaft impact crusher, which can process concrete with rebar, asphalt, brick, block and other C&D debris.
The Lippmann impactor is equipped with a heavy three-bar, solid-steel rotor that offers high capacity and a high reduction ratio and features a new locking device. A hydraulic hood provides easy access to wear parts for quick, easy change-outs, according to the company.
The plant also features a Lippmann 45-inches by 18-feet heavy-duty feeder with a quick removal feed hopper module. Also included are a 48-inches by 45-foot plant conveyor that folds for easy transport; a 16-feet by 6-feet double-deck inclined vibrating screen with two 24-inch cross conveyors; a 48-inch under-screen fines conveyor; and a 24-inch return conveyor.
The unit is powered by a Cummins 460- hp diesel engine with a 350-kw generator and built on a heabvy-duty chassis, according to a Lippmann-Milwaukee release.
GK RECEIVES ISO CERTIFICATION
General Kinematics, Barrington, Ill., a leading producer of vibratory process equipment, has received quality certification for both QS 9000TE and ISO 9001 from NSF International Strategic Registrations Ltd.
According to the company, certification of these international quality standards establishes that General Kinematics Quality Management System has been assessed and registered as meeting the requirements of an extensive quality audit conducted by NSF ISR.
"Receiving QS 9000TE and ISO 9001 certification demonstrates General Kinematics’ commitment to providing quality products and service to our customers and has established us as the largest vibratory process equipment manufacturer to receive this certification," says Paul Musschoot, president of General Kinematics.
The company’s total quality program and continuous improvement philosophy are designed to meet customer quality requirements worldwide.
GENESIS CREATES SHEAR BLADE DIVISION |
Genesis Equipment & Manufacturing Inc., Superior, Wis., has created a subsidiary that will offer replacement mobile shear blades. The subsidiary, known as Blades by Genesis, is initially taking order for blades that are compatible with shears made by Stanley LaBounty, fitting MSD 40, 50, 70 and 100 Series B and Series III mobile shears made by that company. Rob Schlichting, general manager of Blades by Genesis, says the blades are made of a special alloy material designed for maximum wear-resistance. The blades have been field-tested for more than a year. "We’ve had them at work in several applications that we identified as the most severe for blade wear," says Schlichting. Those applications included the "processing of rail cars—a punishing application for blade life," he adds. The Genesis subsidiary is offering same-day shipping on blades and free freight to anywhere in North America. In addition to providing blades, the company will also offer a full wear parts kit that includes primary and secondary blades, shim kits, fasteners, piercing tip and wear plates. "We see this as an opportunity to provide an excellent product and, at the same time, extend Genesis’ availability and service to a broader customer base," says Schlichting. |
The QS-9000/TE Supplement is a quality standard developed for Tier 1 companies that produce tooling and equipment for the Big Three automakers. This standard is more rigorous than the ISO 9001standard, as it requires extensive product and process analysis and a structured planning and problem solving approach. The use of these tools and disciplines ensures the highest levels of equipment reliability and maintainability.
General Kinematics has been serving the recycling, mining, foundry, chemical, food and other industries for more than four decades. To date, more than 35,000 units have been installed in virtually all of the world’s industrialized countries.
HAMMEL KOMPBIO DESIGNED FOR BIOMASS
Germany’s Hammel Recyclingtechnik GmbH is now offering the Kompbio, a shredder for the production of biomass and compostable material, through its Hammel North America distributorship, based in Fort Wayne, Ind. The machine was introduced at the "Bavarian Composting Day" in Munich, Germany.
Hammel is billing the Kompbio as a mobile system that consists of a primary shredder, screening machine and secondary shredder for the separation and processing of roots, mixed tree trunks and green waste into compostable material and marketable biomass fuel.
The Kompbio has been designed to produce a consistent exact final grain size, according to the company.
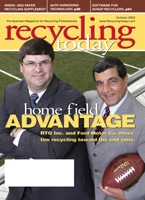
Explore the October 2003 Issue
Check out more from this issue and find your next story to read.
Latest from Recycling Today
- APR launches Recycling Leadership Awards
- Private equity firm announces majority investment in Sprout
- Author predicts spike in silver’s value
- SWANA webinar focuses on Phoenix recycling collaboration
- Domestic aluminum demand up through Q3 2024
- IntelliShift honored at IoT Breakthrough Awards
- Ace Green Recycling finalizes plans for battery recycling site in India
- Ambercycle, Benma partner to scale circular polyester