RETHINKING WOOD FUEL HEAT
Editor’s note: The following "point of view" essay comes from Charlie Cary, a principal with Biomass Combustion Systems Inc., a maker of wood-burning boilers based in Princeton, Mass.
Wood that can produce heat for less than 50 percent of the cost of heat produced by oil and gas is available in many states. The technology to turn this material into environmentally friendly combined heat and power has long been utilized in the forest products industry, which regularly produces energy with its wood residue.
This technology and wood can make American industries more competitive, stabilize their energy costs, create jobs, reduce environmentally harmful emissions and increase the country’s security and energy independence. Any facility that uses heat 24 hours a day is a potential user of this technology.
So why isn’t more wood fuel being used for baseload steam production in industries outside the forest products industry?
After 18 years marketing biomass energy technology, we see a classic chicken-and-egg barrier of confidence in the market. Moderate-scale projects (requiring one to three semi-truck loads of wood a day) are uncommon outside the forest products industry and, as explained below, will remain an unrealized opportunity without a concerted and focused effort to develop demonstration projects.
On the private-sector developer side, the overhead costs associated with quoting biomass projects outside the forest products industry create a huge barrier to developing new markets. The moderate-scale biomass energy industry has never gained the strength to become horizontally integrated. Quoting projects requires coordination among many equipment suppliers and installation contractors. This task is made more difficult when a complete proposal must also include a dependable fuel supply that meets tight specifications at a firm price.
Currently, wood brokers are not marketing to industries with baseload steam requirements, and wood fuel is not being considered by industries. In this environment, finding niche opportunities is challenging and expensive. When there is little evidence that this investment in quote preparation will result in a project, the weak industrial wood energy industry cannot be expected to be a leader in developing this opportunity.
These overhead costs have moved the private sector toward finding economies of scale through large-scale development. Large centralized facilities have received most of the past investment in biomass energy, while projects that match available local wood supply with local baseload steam production have not attracted investment capital.
Every energy service company and engineering firm contacted during research for this proposal was not interested in projects of less than $5 million. This focus on large-scale plants increases the size of the required fuel sheds, which increases trucking and fuel costs. It also restricts the opportunity for wood energy systems by requiring so much fuel. Finally, these large plants create a larger impact on surrounding areas and generate more local opposition.
Increased confidence about the benefits of wood energy is also needed in the public sector. In general, the public sector responds to private-sector activity. Regulations and procedures are worked out over time in response to private-sector and environmental needs.
The chicken-and-egg dilemma has kept the biomass energy industry scattered in the woods and unable to create effective advocacy for these moderate-scale projects.
As a result, the public sector has not thought through the environmental and economic benefits of using available biomass for fuel. These benefits include job creation, less dollar exportation from energy importation, economic security for the region, more competitive local industries, less greenhouse gas emissions and potentially less sulfur, nitrogen and methane production.
But without a focused public sector discussion on these benefits, biomass regulations are often confused with other, less homogenous "wastes," and the political and regulatory climate remains tenuous.
Similarly, the chicken-and-egg barrier of confidence extends to industries that are not currently thinking about using locally available biomass for fuel. Industries contacted about the opportunity to burn wood expressed concerns about fuel dependability, potential regulatory nightmares and increased labor costs. So long as other plants in their industry are not using wood fuel, risk-adverse plant managers shy away from being an industry guinea pig.
On the risk side, issues of using material "from the waste stream" create potential or perceived risks that need to be worked through. The real beauty of wood fuel is that it limits the inputs so the emission outputs are limited. Yet public policy currently does not weigh the public and environmental benefits against the potential emissions and other risks. The issues are not black and white and therefore are difficult for the public sector to tackle.
This barrier of confidence is only going to be broken if the public sector begins to include wood energy in its "smart growth" strategy. This process starts with state governors or the U.S. EPA making a determination that the potential benefits of wood fuel outweigh the potential costs. Once this determination is made, the strategy must be to change current attitudes by educating both the public sector and industries on the benefits of using wood for fuel. The private-sector wood energy industry needs the public sector to show a willingness to work with it. The true test of this willingness would be in the number of projects developed in a limited time. These early demonstrations would do much to break the chicken-and-egg barrier of confidence that currently holds back the market.
ASPHALT GETS SECOND CHANCE
A highway project in eastern Pennsylvania will recycle asphalt roadway reclaimed from a section of interstate to pave two dirt roads.
Sections of pavement from I-80 will be recycled and re-blended to pave the two roads in Columbia County, Pa., about 90 miles west of Philadelphia. According to a report in the Bloomsburg, Pa., Press Enterprise, the recycling project "will save taxpayers hundreds of thousands of dollars."
Brian Toseki, manager of the Pennsylvania DOT (PennDOT) Columbia County office in Buckhorn, Pa., also tells the paper the new pavement will provide a smoother, less dusty surface for residents and visitors to nearby state game lands.
The fall project will transform 10,000 tons of asphalt removed from I-80 into nearly 3 miles of newly paved surface on the two dirt roads.
A contractor will soon convert the now stockpiled 10,000 tons of asphalt at an asphalt mixing plant. PennDOT timing calls for the project to get started in September and be completed within two or three weeks.
PennDOT’s Toseki tells the Press Enterprise, "We expect to get a fairly good life out of [the material]. Once you get that base, you can do a lot of things on it. Down the road, you can seal-coat it or oil and chip."
It is not the first such project in the region. Another dirt road was paved in a similar manner last year using asphalt reclaimed from a state highway-widening project. Using recycled asphalt saved taxpayers $130,000 on that job, Toseki told the local paper. Money is saved when maintenance costs for the dirt roads can be prevented.
PennDOT has been using reclaimed asphalt for roadways for at least five years and has also used it for other civil engineering applications, such as repairing roadway shoulders.
Much asphalt pavement recycling occurs in place, with existing roadway crushed on site for use under or within the new surface. The National Asphalt Pavement Association, Lanham, Md., estimates that at least 70 million tons of asphalt paving is recycled each year in the U.S., at a recycling rate of 86 percent, second only to lead acid batteries.
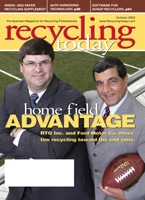
Explore the October 2003 Issue
Check out more from this issue and find your next story to read.
Latest from Recycling Today
- Nucor receives West Virginia funding assist
- Ferrous market ends 2024 in familiar rut
- Aqua Metals secures $1.5M loan, reports operational strides
- AF&PA urges veto of NY bill
- Aluminum Association includes recycling among 2025 policy priorities
- AISI applauds waterways spending bill
- Lux Research questions hydrogen’s transportation role
- Sonoco selling thermoformed, flexible packaging business to Toppan for $1.8B