Automotive dismantlers harvest parts from cars for their resale value. However, they encounter certain items during the disassembly process, such as aluminum wheels and catalytic converters. While they may not have value as resalable parts, these components are valuable as scrap metals and provide a source of supplemental income to yards.
Gary T. Wiesner of PRO Auto Recyclers, Williamstown, N.J., says his company has turned to mining cars for nonferrous metals to make up for the lighter weight of late model vehicles. "We wind up with a lot less steel, so we have to find other means," Wiesner says of the dismantled hulks PRO brokers for shredding. "Anything that we can sell as a recyclable, rebuildable or a core product, we’re definitely reaching for."
PROFIT PROSPECTING. "From where we stand, more auto recyclers will be looking to potential profits from sorted scrap recycling than they have in the past as their other expenses continue to escalate," Bob Hoffmann of Quality Replacement Parts (QRP), Schofield, Wis., says. QRP is a network of professional auto recyclers throughout the Great Lakes region.
Auto dismantlers are increasingly mining aluminum wheels and catalytic converters from vehicles and brokering them to scrap processors. This is nothing new. Actually, as more cars equipped with aluminum wheels head to dismantling facilities, the recovery volume for this item has increased.
"Ten or 15 years ago, there was a smaller percentage of vehicles that had aluminum wheels," Bill Morrison of Morrison’s Auto Parts in Edgerton, Wis., says.
AT THE SHREDDER |
As auto dismantlers continue to remove aluminum wheels and catalytic converters from scrapped autos, shredder operators’ profitability is affected to varying degrees. "Aluminum wheels and transmissions, as well as engine blocks, are all high value parts that many auto dismantlers remove before we get the cars," Steve Shinn of Hugo Neu Schnitzer East, Jersey City, N.J., says. "This is not new." However, shredder yards can adjust for the removal of these items at the scale, offering a price consistent with the nonferrous items still on the vehicle. "We would definitely pay more for a vehicle with a motor and aluminum wheels than we would pay for a car that’s been completely stripped, because there’s more nonferrous metals in there to profit on," Randy Katz of City Scrap Metal, Akron, says. "The nonferrous in the metals is a hidden treasure that you try to capitalize on as much as you can." Shinn adds, "Although quality feedstock is important to shredder operators, the removal of antifreeze, engine oil, fuel, CFCs, batteries and mercury switches by the auto dismantler is really the most critical component of ensuring that the shredder operator receives only autos ready for the shredder." Long-term profitability hinges on environmental compliance. Shinn says the transaction between the dismantler and shredder operator is about striking a balance. "If they take some high-value nonferrous and that’s the cost I have to pay in order to get a hulk that is going to make sure that I can remain environmentally compliant, so be it. It’s a price that the shredder operator at Hugo Neu Schnitzer is willing to pay," he adds. |
"The wheels all have to come off anyway, so it isn’t like you you’re digging in there after them, but they are definitely a product that you’re after at $11 or $12 a piece," he says.
The increase in volume has made the removal of aluminum wheels more attractive to dismantlers, as has their accessibility. The platinum in catalytic converters makes them a valuable item that dismantlers target for recovery.
"The converters are one of the first things to come off a car in the dismantling process," Morrison says. The removal of the catalytic converter enables the dismantler to access the motor and transmission of most vehicles.
David Gold of A. Gold Standard Auto Wreckers, Scarborough, Ontario, Canada, says auto recyclers, regardless of size, most likely recover aluminum wheels and catalytic converters for recycling as standard operating procedure. "Some yards go into detail, most do not," he says.
SIZABLE ADVANTAGES. Larger facilities are often more focused on the scrap value of certain components than smaller yards, Gold says, taking additional steps during dismantling to capture these items.
However, the larger dismantling facilities have an advantage when it comes to recovering items for their scrap value, as they produce more desirable volumes of material and are often located in metropolitan areas, close to scrap processors.
Hoffmann says, "The balance of the auto recycling industry tends to be scattered in rural areas, handles anywhere from 250 to 400 cars a year and doesn’t produce a lot of any one type of scrap."
In addition, he says, smaller yards often focus on removing regulated items, such as mercury switches and fluids, as opposed to the "desirable" items.
Smaller dismantling yards also need cost-efficient methods for transporting their modest volumes of scrap from their rural locations to the scrap processors in metropolitan areas, Hoffmann says.
MOBILE MINES. Larger dismantling facilities have a bit more leverage with scrap processors. "They have a larger bargaining chip in the fact that they can produce so much product," Wiesner says.
PRO dismantles between 220 and 250 cars on average per month. "Normally our buyers are in and our loads go out weekly," he says of his scrap material. "It’s more or less a fifty-fifty proposition. Some we deliver, some they pick up."
To facilitate the dismantling process, Wiesner says, PRO has created charts and follows the same system for almost every car, looking for resalable parts, scrap items and rebuildable parts. "Even if it’s an item that on that particular vehicle wouldn’t have a great value, we would still remove it just to keep with the general flow, the general practice."
In addition to aluminum wheels and catalytic converters, Standard mines the batteries, radiators and condensers from vehicles. Gold says the Scarborough facility averages 350 cars per week.
"Late model cars are dismantled in a different way with an elaborate process. Older scrap cars, which really don’t have much parts value, go through a simpler process," Gold says. "We’re just taking off some of these core products and then crushing it."
Standard sends crushed autos out daily, while wheels, radiators and condensers go out monthly. "We’re trying to get it as consistent as possible, just to get the stuff out of here," Gold says. "The price goes up and down all the time, but most people need the space. Some require the cash flow as well."
PRO, however, will occasionally hold onto items if the price dips. "If in one particular month, catalytic converters seem to be lower, we’ll try to hold them for a couple of months and ride the wave. Hopefully, it will increase," Wiesner says.
WHEELING AND DEALING. "We didn’t really do a lot of shopping on the price part of it," Morrison says of his company’s earlier approach to brokering wheels. "But now, before we sell our aluminum wheels—and we probably generate two semi loads of aluminum wheels every three to four months—I actually just put them out for bids," he says. "I get four bids from four different processors, and the high bid wins."
Morrison says this approach eliminates some of the guesswork on his part and assures him that he is receiving fair market value for the material.
Standard generally phones a couple of processors for prices prior to selling its scrap components. Gold says the company doesn’t always take the highest price, as the availability of transportation and Standard’s knowledge of the processor influence the decision. "Everything plays a factor here," he says.
Wiesner says PRO has three or four processors that it prefers to deal with, having done so for years. "We basically stick with the consistency of our buyers," he says. "We’re still from the old school. We have personal relationships that we like to keep."
DON'T SWEAT IT |
A few of the larger auto dismantlers have installed aluminum sweat furnaces on site to assist in reclaiming aluminum from scrap that also contains large quantities of iron. However, some dismantlers have found the regulations associated with sweat furnaces outweigh the benefits. "We actually had a small aluminum sweat furnace on order," Gary T. Wiesner of PRO Auto Recyclers, Williamstown, N.J., says. That was until Wiesner contacted the EPA Region 2 representative with a few questions. "By the time they gave us the regulations and what type of stacks we’d have to put onto it, it was just ludicrous," he says. Wiesner and his partner decided that the company would be better off continuing with its usual operations, leaving metal processing to those who were already equipped to deal with the associated environmental regulations. |
Although scrap components represent an additional source of revenue for auto dismantlers, it’s an area that they manage closely in light of market fluctuations and the escalating price of labor.
COST ACCOUNTING. The extent to which dismantlers recover less accessible automobile components, such as radiators, condensers and evaporators, for their scrap value is kept in check by rising labor costs.
"The return of managing scrap must be greater, obviously, than the cost to handle it," Gold says. "Sometimes it’s easy to place a value or to place a calculation on certain parts, and those parts are aluminum wheels and catalytic converters."
Gold says the return from wheels is easy to calculate, as they must be removed in the dismantling process and are a valuable scrap component. "Catalytic converters, there’s a little more of a process involved, but the value is so significant that you find time to do it."
Wiesner says he and his partner often weigh the question of whether managing scrap components is worth the time and effort PRO puts into the process. "When the market’s good, it merits it. When the market is bad, it doesn’t. But, like I said, we’ve got to stick with the consistency of keeping that mechanism in tact everyday," he says.
Morrison says the returns of managing scrap vs. the time and effort involved depend on the degree of recovery. "We manage our cost for dismantling vehicles very closely," he says.
While Morrison’s removed aluminum radiators and condensers from vehicles five years ago, labor costs no longer allow that. Today, these components remain with the vehicle.
"What we recover are byproducts that have to be recovered as we’re dismantling the car," Morrison says.
Some dismantlers remove radiators and condensers encountered while retrieving high-value parts for resale. However, Gold stresses that scrap recovery is a byproduct of the dismantler’s core business of parts recovery and resale.
However, in today’s business climate, dismantlers who are interested in maximizing profitability will continue to remove items with scrap value encountered during the dismantling process. Easily accessible and marketable items such as aluminum wheels and catalytic converters continue to provide dismantlers with additional revenue opportunities, particularly those handling significant volumes of vehicles.
The author is assistant editor of Recycling Today and can be contacted via e-mail at dtoto@RecyclingToday.com.
Get curated news on YOUR industry.
Enter your email to receive our newsletters.
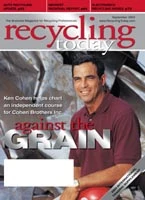
Explore the September 2003 Issue
Check out more from this issue and find your next story to read.
Latest from Recycling Today
- SABIC’s Trucircle PE used for greenhouse roofing
- Hydro to add wire rod casthouse in Norway
- Hindalco to invest in copper, aluminum business in India
- Recycled steel price crosses $500 per ton threshold
- Smithers report looks at PCR plastic’s near-term prospects
- Plastics association quantifies US-EU trade dispute impacts
- Nucor expects slimmer profits in early 2025
- CP Group announces new senior vice president