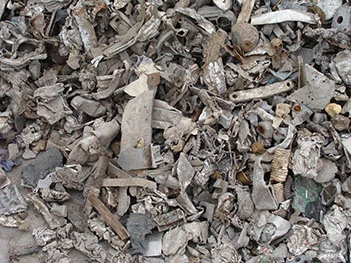
The global market for recovered mixed metals is worth millions of dollars; but, when it comes to some scrap metal grades such as zorba, many recyclers are missing out by employing outdated processing methods.
Suppliers to the industry such as the company I work for, Tomra Sorting Solutions, can help recyclers maximize the treatment of this valuable materials stream and take advantage of the considerable commercial opportunities that are available.
Rapid Developmets
Zorba is the collective term for shredded nonferrous metals, most usually originating from end-of-life vehicles (ELVs) or waste electronic and electrical equipment (WEEE). The Institute of Scrap Recycling Industries Inc. (ISRI) in the United States established the specifications for zorba.
ISRI defines zorba as “shredded mixed nonferrous metals consisting primarily of aluminium generated by eddy current separator or other segregation techniques.”
Other nonferrous metals found in zorba include copper, lead, brass, magnesium, stainless steel, nickel, tin and zinc in elemental or alloyed (solid) form.
Modern day markets for industrial production in all areas of life are creating an enormous demand for nonferrous metals, including copper, nickel and brass, commonly found in zorba. Material prices are constantly increasing, and manufacturers and production companies are demanding higher quality levels for recovered nonferrous fractions than ever before.
The products we use every day present us with opportunities to create zorba fractions when they are recycled. For instance, an average end-of-life vehicle weighing 1 short ton contains not only steel but also 79 kilograms of valuable nonferrous metals, such as copper, brass, aluminium and zinc. Nowadays, a large share of the overall resources used in car production is obtained from recycling these metal components, and this trend is growing.
Electronic products are now widespread in all areas of life and create an enormous demand for nonferrous metals. As an example, the global demand for copper for onboard electrical systems in cars alone amounts to 1.5 million tonnes per year, which corresponds to approximately 10% of worldwide copper mine production.
The recycling of aluminium scrap also is an extremely attractive proposition—up to 95% of the energy costs can be saved when compared with the laborious extraction of the more costly primary resource. At the same time, the demand for aluminium is steadily increasing in markets such as car manufacturing because of its lightweight properties.
To meet these demands, the recycling of nonferrous metals from shredded end-of-life equipment such as cars or domestic appliances is steadily increasing in importance, as many raw materials such as copper or aluminium can be recovered in this manner. However, for this to be possible, these fractions must be extracted to a high degree of purity. The sorting process adds value because the market value of refined individual nonferrous fractions is significantly higher than that of nonsorted ferrous mixtures.
Out with the Old
Recycling companies throughout the world have historically used and, in many cases, continue to use manual or sink-float treatments to sort mixed nonferrous metals. These traditional and outdated methods are limited in their success.
Manual sorting of auto shredder fractions is a cost-intensive process in industrial countries, with a natural lower limit in terms of material recovery. Metal parts and wires smaller than 20 millimetres cannot be sorted by hand easily. If they are hand-sorted, it requires time and effort.
Optically indistinguishable metals are difficult to sort and, therefore, might be lost. For example, it is not easy to manually separate and identify small pieces of cast from wrought aluminium or to spot zinc or steel attachments encapsulated in aluminium. There also is the problem that colour sorting is nearly impossible for identically coloured materials, such as the all-gray metals of aluminium alloys, zinc and lead.
Sink-float processes, also known as dense media plants, are used to separate metals with different densities, such as separating aluminium from other nonferrous metals.
This process can require large amounts of water and other expensive additives such as ferrosilicium (the processing and disposal of which can represent an additional burden to the environment). In terms of productivity, the sink-float method can only separate materials with different densities. The valuable heavy metal mix of copper, brass, stainless steel and zinc presents an unsolvable problem for this method.
As well as being inefficient, these methods are not cost-effective within industrial countries. Thus, zorba usually is sold to processing contractors in low-wage countries who employ manual sorters and resell the fractions at a high profit.
However, using sensor-based sorting technology, it is possible—and financially worthwhile—for recyclers to create pure fractions onsite from their metal mix and sell them into the market for higher profits than before without the involvement of third parties.
Sensible Sensors
Sensor sorting can be used for a variety of applications because different sensors can perform different sorting tasks. Low-maintenance sorting technology combines superior precision with high throughput to produce consistently top-quality end fractions.
Tomra Sorting is seeing an increase in demand for sensor-based sorting technology for the treatment of zorba. By combining two automated solutions, it is possible to remove heavy metals from aluminium scrap to produce melt-ready aluminium. The remaining heavy metals then can be sorted by colour to recover clean copper, brass and mixed heavy gray metals fractions.
Sensor systems that employ X-ray sensors, when in X-ray transmission (XRT) mode, measure the atomic density of the materials to be sorted. XRT technology uses an X-ray source to create broadband radiation which penetrates the material. When attenuated, it hits an X-ray camera equipped with a sensor. This technique uses two independent sensor lines, each with a different spectral sensitivity. The data are then analysed using high-speed X-ray processing.
When used for sorting nonferrous metals, XRT technology removes not only heavies (copper, brass, zinc, iron) that are visible to the human eye but also removes contaminants that are difficult to spot, such as alloyed aluminium (serial 2000 copper rich and serial 7000 zinc rich), zamac and aluminium with encapsulated ferrous screws.
When the aluminium has been separated from the heavy metals, a combination sensor can be used to sort and separate the remaining heavy metals found in zorba. The system combines a colour camera and metal sensor technology and uses the signals from these sensors to determine the target material to high levels of accuracy.
By using these sensors in an off-line set up, the mixed heavy metals can be sorted in multiple runs to produce high-value, high-purity fractions of copper, brass and gray metals.
The technology also presents opportunities for processing fractions such as fines. Because of the growing demand of commodities in general and the downsizing of electronic components, it is now worthwhile to focus more on the treatment and processing grain sizes smaller than 10 millimetres (0.4 inches).
For example, copper granulate, recovered by recycling copper-containing wires, already is a high-value resource. However, not all impurities currently can be removed by common technologies, such as screening or densimetric air or water tables, with noncopper materials like brass, lead or stainless steel remaining in the product. With newer technology, it is now possible to detect and efficiently sort material smaller than 1 millimetre (0.04 inches) and remove these fines automatically, upgrading copper granulate to a purity of up to 99.9%—consequently increasing its value.
In addition to high throughputs and purity, the beauty of sensor-based sorting technology is that its flexible nature allows it to operate in conjunction with existing processing methods. Some metal recyclers are taking a modular approach to investing by purchasing equipment in stages. This helps to keep costs down and represents a major advantage over traditional plant methods, where the whole system must be purchased upfront.
Zorba's Bright Future
Why should recycling companies be interested in sorting zorba? Although the process can be a little more complex than processing other fractions, there is no doubt that the sorting of nonferrous metals from zorba presents real commercial opportunities. By sorting zorba, it is possible to produce high-quality end fractions of aluminium, copper and brass, which can then be sold on to smelters (both within their regions and overseas) at a much higher market value.
In addition, the markets for zorba are thriving, both for the initial untreated material and for the final treated fractions. The growing sale and ultimate disposal of consumables such as cars and electronic devices show no sign of slowing down. This provides a steady stream of both input material and valuable opportunities to produce quality end fractions.
A key benefit of sensor-based sorting for treating zorba is that it can add value to each of the target metals and help deliver high-quality end fractions consistently. The systems do not necessarily represent a massive investment: Tomra estimates the operational cost to be 80% less than the cost of running a dense media plant. The typical payback period for a sensor, by Tomra’s calculations, is between six and 36 months. The systems are designed to work in conjunction with existing processing methods.
With continued growth in worldwide demand for high-quality nonferrous metal fractions, it may be time to consider this approach to processing the valuable and in-demand zorba stream. With sensor-based sorting techniques, recycling companies may find a genuine opportunity to enhance their operations for a modest outlay and also add to the bottom line relatively quickly.
Judit Jansana Borrajo is head of technical sales, Iberia and Latin America, for Tomra Sorting Solutions, www.tomrasorting.com/recycling. The company is a global supplier to the recycling, mining and food processing industries.

Explore the December 2013 Issue
Check out more from this issue and find your next story to read.
Latest from Recycling Today
- Harsco brands slag-content asphalt as SteelPhalt
- ArcelorMittal puts French EAF conversions on hold
- Associations ask for effective EPR to drive textile circularity in Europe
- GESA report claims 72 countries recycled EPS in 2023
- Report: Saica exploring recycled paper mill project in Dayton, Ohio
- Hydro’s Alumetal to meet 15 percent of its energy demands through solar
- CSA Group publishes standard defining plastics recycling in Canada
- Second Cyclyx Circularity Center to be located near Fort Worth, Texas