Versatility has become a hallmark of recyclers who serve residential and commercial accounts, as operators of material recovery facilities (MRFs) are increasingly being asked to recover a wider range of materials for recycling and to do so from commingled streams. The task creates challenges that MRF operators need to rise to in partnership with their equipment suppliers if they are going to succeed.
Toronto-based Canada Fibers Ltd. has embraced these challenges and the opportunities they represent. The privately held company was founded in 1990 as a brokerage service and soon expanded into paper converting, with a focus on slitting and rewinding newsprint and sheeting newsprint, says Jake Westerhof, vice president of operations. Canada Fibers soon expanded into scrap paper processing, adding a small plant in 1992, he says. That operation was expanded in 1998 when the company was awarded a contract with the city of Toronto to process curbside-collected paper.
“That was our first contract with a municipality for the processing of recyclables,” Westerhof says.
A Growing Processor
That initial contract with the city of Toronto acted as a springboard that propelled Canada Fibers into additional contracts to process recyclables for municipalities. Today, the company has contracts with several municipalities in addition to expanding its processing of material from the industrial, commercial and institutional (IC&I) sector and its brokerage services, Westerhof says.
The transition into processing residential and IC&I material has required considerable investment on the part of Canada Fibers. Currently, the company owns and operates six processing plants, four of which process residential recyclables from curbside programs.
Canada Fiber’s head office facility at 322 Horner Ave. in Toronto includes a waste paper division, a shredding division and its CMC Paper Converting division. The company also operates a MRF on Vanley Crescent in Toronto. The C$8.4 million (US$8.7 million) MRF began operation in 2005 after Canada Fibers was awarded a long-term contract to process curbside-collected recyclables for the city of Toronto. The single-stream plant can process up to 120,000 tons per year at a rate of 30 tons per hour, according to the company. Canada Fiber’s third Toronto facility is at 122 Arrow Rd. That 150,000-ton-per-year plant processes IC&I material as well as complicated material streams.
“We avoid the term ‘dirty MRF,’” Westerhof says of the Arrow Road facility. “It is a MRF that is trying to recover material from difficult-to-recycle streams,” he adds.
In April of 2006, Canada Fibers opened a MRF in Sudbury, Ontario, after obtaining a long-term contract with that city. The company describes its Sudbury MRF as “the first single-stream facility in northern Ontario complete with the latest single-stream technology, only on a smaller scale.” The Sudbury MRF features 40,000 square feet of processing area and a yearly capacity of 30,000 tons.
The company also operates a single-stream MRF with a capacity of 120,000 tons per year in Ontario’s Peel Region, which includes the municipalities of Brampton, Caledon and Mississauga. Finally, its dual-stream MRF in Hamilton has a yearly capacity of 65,000 tons.
Canada Fibers processes and brokers roughly 800,000 tons per year of material, Westerhof says, the majority of which it processed in house.
Of all the facilities Canada Fibers operates, it Arrow Road plant is perhaps the most unique.
On Target
The company’s Arrow Road facility processes IC&I material primarily and was designed to be versatile, says Plant Manager Stephen Miranda of Canada Fibers.
“At the Arrow plant, what we truly tried to do was to come up with a system capable of handling waste streams and material that weren’t traditionally captured,” Miranda adds.
Westerhof says Canada Fibers’ Arrow Road facility “chases recoverable materials that are not typically being chased,” such as highly contaminated streams collected in public spaces and even residuals from conventional MRFs, which it reprocesses.
“That is not an indictment of other MRFs,” Westerhof quickly adds. “There is always going to be a percentage of recyclable material that leaks off of any recovery system.”
Miranda adds that the plant is succeeding at its goal, recovering from 75 to 80 percent of incoming material.
“We designed the plant to recover smaller fiber and smaller plastics that would not get recovered at a conventional MRF,” Westerhof says.
Miranda adds that this is achieved in part by making minor modifications to widely available processing technology. This includes adjusting the angles of various screening equipment and the speed of the conveying equipment.
Canada Fibers also is in the midst of a significant update at this plant that includes the addition of a single-stream MRF, which the company expects to be operational by the end of April 2013. “It will have in the neighborhood of 350,000 tons per year of capacity,” Westerhof says of the new single-stream MRF.
He adds, “The city of Toronto is asking for performance specs that have not been met in any single-stream facility in North America. It has challenged us to raise the bar. We’ve taken it upon ourselves to comprehensively improve our system design in terms of material throughput, recovery requirements and material quality.”
In turn, Canada Fibers has challenged its equipment vendor to raise recovery capabilities and focus on material quality, Westerhof says.
“The plant will be faster and better,” he says of the new Arrow Road single-stream MRF.
The company has selected Van Dyk Recycling Systems, Stamford, Conn., a system integrator that supplies equipment from Bollegraaf, Lubo and TiTech.
Westerhof says Canada Fibers has worked with no less than four of the major systems suppliers. “That gives us a very unique perspective,” he says. “We have come to understand the strengths and weaknesses of each of those major manufacturers, which helped in our selection process.”
Westerhof adds that Canada Fibers’ agnostic approach to equipment selection offers numerous advantages. “It improves our operating abilities to have experience with different equipment. It challenges us to be the best possible operators we can be,” he says.
A Challenging Environment
Another challenge the company faces is the changing nature of the recycling industry and consumer packaging, Miranda says. “The recycling industry is changing all the time,” he says. “New products keep getting added to the stream. We have to remain flexible in what we do to be on top of those changes and to recover anything required to be recovered.”
Miranda adds, “The goal of the company is to divert everything we can from landfill.”
Westerhof says several organizations are looking closely at designing packaging to improve its recyclability in response to extended producer responsibility (EPR) programs being introduced in Canada. “An interesting dialog is taking place, and we are participating as a company to share our view on managing new packaging design going forward.”
Among Canada’s provinces, Ontario lags behind British Columbia and Quebec in implementing EPR programs. In Ontario, “municipalities with at least 5,000 inhabitants are required to operate Blue Box programs to collect newspapers, polyethylene terephthalate (PET) bottles, aluminum and steel cans, glass containers, as well as a minimum of two supplementary printed paper or consumer packaging items made from metal, plastic or glass,” according to Environment Canada. The Waste Diversion Act of 2002 introduced requirements for industry stewards to pay for 50 percent of net municipal Blue Box costs through Stewardship Ontario.
“We support EPR,” Westerhof says, “because we feel it will drive more material to recycling and away from the disposal stream.” However, he says, “There is still a lot of work yet to do in terms of transitioning to that system.”
Westerhof adds that initiatives are proposed in British Columbia, Quebec and Ontario to move to full EPR systems for consumer packaging and printed materials in which manufacturers will provide 100 percent of the program funding rather than partial funding.
While the recent recession was felt less acutely in Canada than in the United States and other parts of the world, Canada Fibers was not immune to the side effects experienced by the global recycling industry. “2008 and early 2009 were a difficult time everywhere,” Westerhof says.
The lesson that Canada Fibers learned as a result of the recession: “We need to be nimble and flexible in our operations to be able to respond to all manner of changing conditions—economic or otherwise,” Westerhof says. “Being responsive is key.”
He adds, “We are not producing widgets, and what comes in the door every hour is constantly changing, especially at Arrow Road.”
The company’s objective is “to get the most out of our recovery programs for our customers, thereby conserving resources and saving valuable landfill capacity.” Therefore, Canada Fibers’ focus on responding to the changing nature of the materials stream by adapting its operations should serve the company, and its customers, well in the future.
The author is managing editor of Recycling Today and can be contacted at dtoto@gie.net.
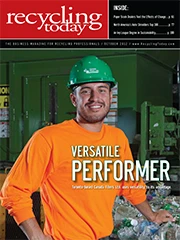
Explore the October 2012 Issue
Check out more from this issue and find your next story to read.
Latest from Recycling Today
- LumiCup offers single-use plastic alternative
- European project yields recycled-content ABS
- ICM to host colocated events in Shanghai
- Astera runs into NIMBY concerns in Colorado
- ReMA opposes European efforts seeking export restrictions for recyclables
- Fresh Perspective: Raj Bagaria
- Saica announces plans for second US site
- Update: Novelis produces first aluminum coil made fully from recycled end-of-life automotive scrap