Electronics recyclers see their industry as one that can harvest valuable materials while also avoiding hazardous disposal mistakes.
When Bill Gates and Steve Jobs were in the home stretch of the race between IBM and Apple computers to make the most powerful computer first, most likely neither was too concerned with how those machines would one day be disposed of or recycled.
The technology being created was so new and captivating that the thought of something faster and more powerful couldn’t be conceived—and the word “outdated” wasn’t part of their computer jargon. But now, as computers and electronics equipment constantly becomes more powerful—and thus, outdated more quickly—concerns have been raised about how to avoid filling landfills with both materials that could be reused or with products that may contain hazardous chemicals.
Researchers estimate that from 14 to 20 million computers are put out to pasture each year, with about 75% of those retiring to basement shelves or out-of-the-way closet shelves, a 1995 Tufts University thesis estimated.
While some people may think that obsolete electronic equipment is a gold mine waiting to be found, only about 30% of those units are resellable—the remaining 70% are usually thrown away if they are not recycled.
And while old computers and electronics equipment can be recycled, it is typically a not-for profit endeavor for the previous owner. In fact it may end up costing the consumer money to dispose of old products properly. This is one major stumbling block electronics recyclers have yet to overcome, says Peter Muscanelli, founder and president of the International Association of Electronics Recyclers, Albany, N.Y.
“We as a society need to look at the benefit of recycling not as a net positive,” Muscanelli says. “The key factor is that the $10 is well spent up front because once an item is in a landfill and broken apart you are never going to be able to recover any of the components for recycling.”
This line of reasoning holds that although it may be more expensive up front to recycle electronic equipment, it may be less expensive in the long run, he says.
“We want to help people to understand that if you spend a little money now it will come back a hundred times because it is not in a landfill,” Muscanelli says. “People are changing their mentality and tuning in to the fact that we have a specific amount of goods to use and they are renewable if we recycle.”
FINDING THE BEST METHODS
While both consumers and businesses may want to recycle machines no longer in use, the best way to accomplish that goal is an avenue that is still being explored. Since the industry is so new, no one method has been found to be the best when it comes to separating and recycling the components of electronics equipment.
Materials such as gold, silver and platinum can be recovered from computers and electronics equipment, but figuring out how to do so—and to do so profitably—is a puzzle the industry has not completely solved. A variety of options are available for recovering materials from the equipment—ranging from manual disassembly to crushing the products in a hammer mill and separating the end products.
The Goldsmith Group, Indianapolis, Ind., has found a way to recycle computer components and be profitable at it. The company specializes in the resale of computer and electronics equipment and sells refurbished products, as well as dismantling units and reselling the components. “We have found a niche in the knowledge of resale,” says Goldsmith Group vice president Eric Goldsmith. “That way we can service people’s equipment longer and furnish refurbished market.”
Goldsmith says knowing where the demand in the market is for specific pieces of computer equipment is the key to success in the recycling business. “It’s somewhat a glut in our industry, but there is still a niche in the resale and knowing what you’ve got and what people want,” he says. “If there is a scrap yard that doesn’t know about us, you can count on us reaching out to them.”
Goldsmith Group averages about two million pounds of product a year, including computers, monitors, mainframe computers and medical and telephone equipment, says Sam Goldsmith, vice president of Goldsmith Group.
DMC Electronics, Newfields, N.H., also specializes in the field of computer and electronics resale, but has a company policy of not landfilling any of the waste created in the refurbishing process, says Richard Campbell, corporate relations for DMC Recycling. “The basic premise of our whole operation is reutilization. We separate what we can sell, refurbish what we can and the next tier is demanufacturing.” Waste materials generated from the recycling process, such as plastics, paper and fluff, are sent to a local recycler who uses the materials as road aggregate.
“We recycle electronics, computers and telecommunication equipment, pretty much anything that will plug into a wall,” says Campbell. But, DMC is finding that about 20 percent of the materials from electronics equipment are reusable and the rest has to be demanufactured. DMC completes the recycling of electronics at their 87,000 square foot facility. About 350,000 pounds of materials are handled by DMC a week.
DMC Electronics is a certified ISO 14000 by the International Organization for Standardization, says Michael F. Magliaro, president of DMC Electronics. ISO 14000 is a set of environmental management standards developed to give companies structure for managing environmental impacts. To be ISO 14000 certified a company must show that they take steps to control elements that could be harmful to the Earth of left uncontrolled. DMC Electronics is one few U.S. companies with ISO 14000 certification, Magliaro says.
In addition to the Newfields location, DMC will be opening a Hagerstown, Md., facility in October and plans to have four or five more sites coming online in the next two years, he says.
Another computer recycler to come online recently is also finding a demand in the market for the services offered. The Oak Ridge National Recycle Center (TORNRC) began operation in mid-July and Rodney Dean, vice president of TORNRC, estimates the facility has processed about 500,000 pounds of computer equipment so far. The company refurbishes equipment for resale and pieces that can’t be refurbished are dismantled for resale or recycling.
Located at the East Tennessee Technology Park (ETTP) in Oak Ridge, Tenn., the former site of the Manhattan Project, the center was created from a grant from the Community Reuse Organization of East Tennessee (CROET) and is a joint venture between Diversified Environmental Services Inc. (DES) and 5R Processors Ltd. TORNRC is receiving materials from the Department of Energy and companies such as United Parcel Service.
The company has had a very good response from computer manufacturers and is operating ahead of schedule, says Dale Jessop, vice president of Diversified Environmental Services Inc. “Our ultimate goal is a national electronics recycling center,” he says.
In addition to the resale of computer and electronic equipment, items can be processed using a shredder, such as the ERS6000 (Electronics Scrap Recycling System) by Shred-Tech. The fully automated system processes electronic scrap ranging from PCs to mainframe computers, says Rob Glass, sales and marketing vice president of Shred-Tech, Cambridge, Ontario, Canada. The system can handle a wide range of materials. Materials are put into the system and separated into streams of copper, aluminum, steel, brass and plastics and then collected for recycling. Precious metals such as silver, gold, platinum and palladium are also collected. The system can process about three tons of materials an hour, he says.
Some shredder owners can choose to perform preliminary dismantling if there are parts that could be resold and reused, but the ERS6000 can process materials without any dismantling, which can be a labor intensive and very expensive process, Glass says. The automation of the ERS makes it the first system to handle all types of materials and to separate them effectively, and it can handle all types of materials, according to Shred-Tech.
Efficient separation is the key to successful processing, Glass says. “There are various ways to do it, but the key is to automate it.” An ERS6000 system was installed at the Hewlett-Packard/ Micro Metallics recycling facility in Sacramento, Calif. about two years ago and Shred-Tech has had a positive response to the system, Glass says.
A PATH TO PROFITABILITY
As more and more techniques for electronic recycling become available, recyclers have begun to figure out how to recycle for profit. Muscanelli says he thinks that companies that have found a way to become profitable in the field of electronics recycling manage their resources extremely well and are very frugal and efficient. “You have to be very sharp in managing everything in order to stay in business,” he says.
United Recycling, West Chicago, Ill., offers a variety of recycling services ranging from the resale of equipment to the dismantling of units and the sale of the individual parts. The company processes about two and a half million pounds of materials a month, says Bob Glavin, president of United Recycling. “It’s a monster and you have to keep feeding it,” he says of the demand to recycle.
To handle the increasing amount of materials coming into the facility, the company moved from their 30,000-square foot building to an 85,000-square foot facility in January. In April another 100,000 square feet were added for the demanufacturing portion of the business.
The company accepts electronics, medical and test equipment and understands that “the customer wants to maximize the value of the products coming out,” Glavin says. “First we try to resell it as a working unit, and if that doesn’t work we try to sell the components out of it.”
United Recycling completes as many recycling processes in house as possible, Glavin says, and to ensure that materials are recycled overseas, United is looking to open a facility in Hong Kong. Glavin says many materials end up in landfills when materials are sent overseas to be recycled. “The only assurance you have is to do it yourself.”
DANGERS IN RECOVERING MATERIALS
Determining what process to use to recover materials from equipment is just part of the challenge. The handling and disposal of hazardous materials in computer and electronic equipment can offer more hurdles to overcome.
“The industry is very much in its infancy,” says Lauren Roman, president of Industrial Services, Flanders, N.J. “Most people know that there are hazardous components, but you can’t look in a manual.”
But, Muscanelli says, if those materials are recovered from products before they make it to the landfill, everyone can save time and money in the long run. “Electronics have components that would be deemed hazardous once they are broken down in landfills and leach out,” he says. “When they are reclaimed they may be hazardous components, but you are lessening those components in the environment.”
Hazardous materials commonly found in electronics equipment include mineral oil capacitors (PCBs included), batteries (lead acid, nickel/cadmium, lithium and alkaline), printed circuit boards (lead), mercury relays (mercury), cathode ray tubes (lead and cadmium), photoreceptor drums (selenium/ arsenic) and gas springs (oil).
The components cause a problem for recyclers because they are considered hazardous waste and can be expensive to dispose of. “If they aren’t resellable second hand, people aren’t really interested in them and the majority of them find their way to a blast furnace,” says John Hanson, executive director of the Recycling Council of Ontario, Toronto.
In Canada, electronics equipment is not categorized as hazardous waste and therefore is not being treated as such, Hanson says. “But, there are a number of commercial recycling centers opening up that are independent or have some sort of affiliation with computer manufacturers.”
MAKING A DIFFERENCE
To help promote electronic recycling, the National Recycling Coalition (NRC) is preparing to launch a new portion of their current website. An online forum will give people in the electronics recycling industry an opportunity to discuss issues faced by processors and to talk with experts in the field, says Edgar Miller, director of policy and programs for the NRC, Alexandria, Va.
The forum, scheduled to begin in October, is “an online information exchange for discussing issues related to computer and electronics recycling,” Miller says. “We have established a work group of national experts on identifying topics and discussion issues.”
Some issues the forum will address include recovery of materials, proper usage of materials, the needed infrastructure to collect materials and collection options, he says. The forum is intended to help people create a knowledge base about computer and electronics recycling as people begin to change and upgrade their computer systems.
Other organizations involved with the recycling of electronics and computer equipment include the American Plastics Council, Washington. Since the Plastics Recycling Conference ‘97, sponsored by the Society of Plastics Engineers, Brookfield, Conn., the APC has addressed plastics recycling issues through workshops at the annual conference, says Michael Fisher, director of technology for the American Plastics Council. “The conference is directed at bringing the results of APC research to manufactures and recyclers,” he remarks.
WHERE THINGS ARE HEADED
Several developments on the drawing board could affect the manufacturers of electronics equipment, both in the United States and overseas.
The development in Europe of the Waste Electronics and Electrical Equipment directive could impact both European and American companies, Hanson says. The proposed directive would address the recycling of electronics equipment and design issues that would facilitate recycling more easily. Lead, mercury and cadmium would also be phased out materials by 2004 as well. The directive would apply to all electronics equipment sold in Europe, even if made by an American company and sold overseas.
“A lot of American companies could be impacted,” he says. “It places the burden of end of life management to the maker. We definitely recommend those measures we see as feasible and desirable from an environmental point of view.”
While there are currently no bans on the landfilling of computer and electrical equipment in Canada, Hanson says the Recycling Council of Ontario would be very supportive of a ban. In addition to the possibility of new regulations, Ontario hopes to form a waste diversion organization in the coming months.
While the recycling of electronics equipment by businesses and industry seems to be advancing, the next challenge may lie with convincing the public that the materials should be recycled and how to capture those goods. “Most of the materials are in the hands of the consumer,” says Magliaro. “I think that collection is the biggest challenge for consumer goods.”
The author is the assistant editor of Recycling Today.
Sidebar
DESIGNING FOR RECYCLING
One of the hurdles to the recycling of electronics equipment is not only capturing the materials, but also being able to recycle them profitably. For operations that demanufacture units, design issues can make that process more tedious. Units that have many different types of plastics or both Phillips and flat head screws can slow down the disassembly process, making the recycling process harder to complete and less profitable for those involved.
Reggie Caudill, director of multi-life engineering at the New Jersey Institute of Technology, Newark, N.J., says there are a number of design elements that can be changed to make demanufacturing easier. “You want to minimize the number of different types of materials especially if they are fairly similar in material characteristics,” he says. “There are several fairly standard kinds of things you look for, such as using the same plastic or ones that are compatible.”
Identifying design elements that may be of value to both the manufacturer and the demanufacturer could help make electronics recycling easier and save manufacturing costs as well, says Glenn Kuntz, principal technical manager for Concurrent Technologies Corp., Largo, Fla.
“It has to be something easier to do and that makes money for the company,” he says. “If it makes it easier for them to assemble and more profitable for the company, then manufacturers will go right along with something that saves them money. If you can show an environmental benefit and that it is also has a financial benefit, then companies are happy to comply. ”
Get curated news on YOUR industry.
Enter your email to receive our newsletters.
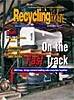
Explore the September 1999 Issue
Check out more from this issue and find your next story to read.
Latest from Recycling Today
- Circular by Shapiro releases "5 for Five" sustainability series
- Graphic Packaging set to close Ohio CRB facility
- Ameripen voices support for Maryland EPR bill
- Matalco to close Canton, Ohio, plant
- Maryland county expands curbside recycling to include electronics
- California EPS ban will be enforced
- YKK AP America introduces BetterBillet
- Fresh Perspective: Cameron Keefe