
For many people, the phrase "scrap yard" conjures up the stereotypical image of acres of land piled high with scrap metal waiting to be processed. This image (often a misperception) has created problems for companies in their communities.
However, Green Metals Inc. (GMI), jointly owned by a combination of Toyota Tsusho America, ARK Inc., Toyota Tsusho Corp. and Nakadaya Corp., has taken a different approach to designing, building and operating a scrap metal handling facility, which is part of its overall strategy to create a profitable processing facility that also operates in an efficient and environmentally sound way.
While this may be the goal of many scrap recycling companies, for Green Metals it is ingrained into the business culture. In fact, its corporate policy—"Green Metals is dedicated to the preservation and protection of our environment through the use of state-of-the-art recycling technology and the conservation of natural resources"—is printed on the back of the business cards of many of the company’s staff.
A BETTER MOUSETRAP.
The most apparent difference between GMI and many other scrap recycling companies is the facility itself. While most ferrous scrap facilities conduct the majority of their business outside, Green Metals operates in a totally enclosed facility. The company’s Georgetown, Ky., headquarters plant is a 37,000-square-foot facility where it processes industrial ferrous scrap. A smaller building, adjacent to the ferrous plant and roughly half the size, handles a growing volume of nonferrous metal.Despite the relative smallness of the building, its design features provide advantages. For instance, walls within the building are configured to allow the company to segregate metals by type, including busheling, No. 1 bundles, turnings, cast iron borings and shearable scrap. At the nonferrous site, GMI takes in bare and insulated copper, brass, stainless steel and aluminum.
An elevated walkway allows staff to move throughout the building without running the risk of being injured by any of the equipment.
The 12-inch-deep concrete floor of the company’s enclosed "yard" has a plastic liner to prevent fluids from seeping into the groundwater. Any liquid that results from processing is extracted, stored and then shipped to another company where the material is recycled. Further, the liner also works to prevent soil and storm water contamination, further reducing product liability coverage for its customers. The liner is attached to each of the perimeter beams and then sealed. "This is done to minimize the penetration," GMI’s Rob Paulson says. "We also have dug out well areas and we have monitoring ports that we can inspect."
Paulson adds, "We pump out and recycle all the liquids generated at the plant. The company we use decants the water and recycles the oils and residuals." Additionally, GMI internally recycles some of the coolants extracted from the catch basins at the plant’s base.
This design is not limited solely to the Georgetown facility. GMI takes a similar approach at all its plants.
The enclosed facility also is highly automated, with cameras at various locations in the plant. This gives employees in the adjacent office a real-time view of the operations and enables them to check for problems and to ensure efficient processing.
While building such a facility costs more upfront than a traditional scrap yard, GMI Vice President Steve Cecil says the increased automation and lower labor costs gives GMI a cost-effective advantage on an ongoing basis.
"We feel our totally enclosed operations are a huge benefit to our customers," Cecil says. "With certain legislative rulings indicating the generator of scrap materials being the responsible party, our facilities minimize the risk for our customers who are the generators." He adds that because GMI is so young, there is less inherent Superfund risk associated with doing business with the company than there might be with some older scrap processors.
The design of Green Metals’ plants are reflective of not only Toyota Tshuso’s business philosophy, but also of a large percentage of Japan’s scrap recycling business. While GMI’s Georgetown plant is in an industrial park with plenty of room for outside storage, the operation is designed similarly to many Japanese scrap yards, which are in residential neighborhoods and need to blend with their surroundings.
A TAILORED APPROACH. While many scrap recyclers may highlight their long pedigrees in the scrap recycling industry, GMI is a relative newcomer to the United States. The company opened its first U.S. location, the Georgetown plant, in March of 2000.In addition to the Kentucky plant, GMI operates similar facilities in Princeton and Columbus, Ind.; Eleanor, W. Va.; Huntsville, Ala.; and Jackson, Tenn. The company is also in the process of constructing a scrap facility in San Antonio.
GMI also has operations in Japan, China, the Czech Republic, South Africa and France. Further, the company expects to continue its growth, adding scrap processing facilities close to its manufacturing operations.
Global in nature, the success of Green Metals ultimately resides in its onsite day-to-day management. VP Cecil has about 25 years of experience in the scrap metal business. Paulson, with around 17 years of experience, is responsible for ensuring that GMI exceeds its already aggressive environmental standards.
Despite not having the decadese of history that many other scrap metal recyclers have, Green Metals offers quite a few benefits to its customers. Masami Iwase, who is the coordinator for GMI and its parent company, says customer service is a major selling point.
"Most dealers operate only during daytime. But scrap generators operate not only during the day, but also at night," Iwase says. "To operate during the second shift, normally scrap dealers will have trailers and trucks to store scrap at night, but it doesn’t look good for customers. Also, scrap companies need to have space to store the material." Because GMI operates around the clock, its customers don’t need to prepare storage space, Iwase adds.
On the consuming side, GMI has attempted to build a stronger rapport with its customers is by tailoring its shipments to a particular operation. Cecil explains: "Many times we will put together special blends for our customers. We may put together packages for them that have a certain percentage bundled, a certain percentage loose. What that allows the mill to do is take it right to their furnace. Therefore, we can receive more money because we are eliminating one of the steps in the company’s process." He adds, "Everything we try to do with our customers or consumers is a partnership. We are interested in long-term partnerships."
While running a profitable scrap recycling facility is always challenging, even in the best of times, Green Metals, as well as its sister company ARK Inc., operates under a standard that provides total waste management based on Toyota Motor Manufacturing’s zero-landfill philosophies and on ISO 14001 standards, which specify a process for controlling and improving a company’s environmental performance. The ISO 14001 process consists of general requirements, environmental policy, planning, implementation and operation, checking and corrective action and management review.
The importance of achieving exemplary environmental quality standards throughout the company is toward the top of the list in GMI’s mission statement. To accomplish this GMI continually looks to expand its business to provide maximum environmental protection for its customers by using a totally enclosed facility, providing competitive revenues, using its continuous improvement philosophy and providing enhanced logistical services.
One point that Cecil is most proud of is the fact that everything that comes into the plant is recycled, whether it is metal, fibrous material, plastic or even liquid. Everything that comes in the door ends up being processed on site or contracted out to another vendor.
FOCUSING ON MOVEMENT.
Visitors to GMI’s plant also will notice relatively few employees. While many scrap yards have dozens of employees, Cecil estimates that the Georgetown plant operates with roughly 20 people. Considering that the plant operates 24 hours a day, 365 days a year, the economics make sense.Iwase notes that the initial investment at the Georgetown plant continues to pay dividends when adjusting and tweaking later plants. "As far as efficiencies go," he says, "we might at first use 10 people, but then one year later at an existing or new plant, we may be successful in operating with fewer people, maybe seven, maybe six, maybe five."
The day-to-day operations also speak to the efficiency of the Green Metals approach. All the scrap metal that comes into the plant moves via truck. Outbound shipments are sent via truck and rail. The plant can accept as many as eight rail cars at once and includes two rail spurs to keep the flow of material steady.
Because the Georgetown plant has no space available to store excess material, keeping the material moving is of paramount importance. The operation is designed so that all the material that is shipped into the plant by truck is then processed and shipped out, either by truck or rail, on a daily interval. The key to the company’s success is the continuous movement of the material, regardless of market conditions.
Also, because of the rapid flow of material and the lack of storage space, GMI does not get involved in hedging or speculating. "Our philosophy is simple. We don’t speculate on scrap. We are a manufacturer. The material is processed, loaded and shipped," Cecil says. Iwase adds that speculating on prices goes against GMI’s basic business philosophy.
While Georgetown may not seem to be in the heart of a traditional scrap corridor, a significant number of auto plants are in the general area, and around 100 Japanese businesses in Indiana and Kentucky support Toyota.
GMI’s Georgetown facility sits in a large industrial manufacturing park, adjacent to a number of other large Toyota facilities, including steel slitting operations and a Toyota Automotive plant. The proximity of these facilities facilitates continuous operation. Although the company takes in quite a large amount of material from other Toyota manufacturing operations in the area, Green Metals is not totally beholden to the company. GMI also takes in and processes scrap from a number of other auto and general manufacturers in the area.
To provide full service to its industrial and commercial accounts, Green Metals also accepts non-metallic materials such as shrink-wrap plastics and even some paper, which it then ships to other vendors. GMI’s sister company ARK typically handles these materials and is also within the Toyota Tsusho complex.
THE KAIZEN WAY. In discussing the company’s overarching business philosophy, Iwase stresses the importance of kaizen. Roughly translated, this Japanese word means "continuous improvement of operations."
Iwase says, "This is a highly important philosophy that Toyota Tshuso has incorporated into its overall structure." By finding ways that continuous improvements can be filtered through the company, a more efficient, environmentally safe operation can be achieved.
For kaizen to work, Cecil says, "Everyone has to buy into it. This means from the top executive in the company to the lowest level employee, every person must look for ways to make Green Metals a more efficient operation."
GMI emphasizes many of the Toyota Production System (TPS) guidelines, Cecil adds. "These are basically continuous improvement; training and development of associates; candid and open relationships with customers; and providing safe work environments where associates are treated with respect."
These quality standards and environmental policies are not only enforced at GMI’s North America plants, but at its facilities worldwide. In fact, Cecil says that a Green Metals operation in Tianjin, China, must operate in as environmentally friendly a way as the plants in the United States, regardless of the mandated standards in that country. This environmental policy is incorporated through GMI’s total structure, making it a key supplier in the Toyota chain, but also subject to fewer environmental problems that may crop up for scrap metal recyclers.
By establishing and maintaining close relationships among its plants, GMI can ensure overall success.
MORE THAN JUST WORDS.
Many companies with multiple locations or operations in different parts of the country may talk about how they operate under the same policies. Occasional meetings and conference calls may occur, but individual yards may actually operate in isolation and as their own separate entity.However, GMI recently brought top representatives from all of its locations to a meeting at a college campus close to Green Metals’ Georgetown facility so they could discuss issues that may be common to all.
Cecil says that while exchanging e-mails and talking on the phone is helpful, getting the diverse group of representatives together allowed GMI to discuss more important issues. While there are nuances among GMI’s locations, many issues carry through the different locations, making the conference an effective way to strengthen the company’s overall structure.
The meeting gave representatives from GMI’s different worldwide locations the opportunity to promote training techniques, discuss equipment and maintenance issues and work through standards and processes.
Green Metal’s locations also are designed to maximize their proximity to Toyota plants. In addition to the Georgetown plant, which is nestled in with other Toyota-based operations, the company’s other plants also are located next to or very close to other Toyota facilities, reducing the time and cost for transporting the scrap material to the plants.
The company’s kaizen model has enabled it to shrink the size of some of its facilities, squeezing out excess to include only the space actually needed for processing operations.
Also, while Green Metal’s Georgetown plant currently operates two overhead cranes, the company is looking at the viability of using only one crane if it can improve overall efficiency.
Along with the cranes, the plant also employs Metso balers, a Sierra shear and a Mayfran aluminum turnings centrifuge at its nonferrous plant.
As for the future of Green Metals, both Iwase and Cecil see a big upside. With the kaizen approach, the company will continually look for ways that future and existing plants can adjust their operations to become more efficient. Whether that means reconfiguring an existing facility to design a pit to eliminate steps, switching from an overhead crane to hydraulic crane or reducing the number of cranes a plant uses, Green Metals uses the experiences from each of its plants to improve its operations overall.
While the company has only been in business for five years, Green Metals already has had success in establishing its presence in many locations. As Toyota continues to grow as an international company, Green Metals aims to grow in concert.
The author is Internet and senior editor of Recycling Today and can be reached at dsandoval@gie.net.
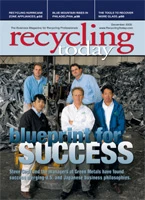
Explore the December 2005 Issue
Check out more from this issue and find your next story to read.
Latest from Recycling Today
- IntelliShift honored at IoT Breakthrough Awards
- Ace Green Recycling finalizes plans for battery recycling site in India
- Ambercycle, Benma partner to scale circular polyester
- NIST database aimed at increasing textile recycling
- ILA, USMX announce tentative agreement
- Innventure subsidiary acquires rights to advanced plastics recycling technology
- Radius experiences sixth consecutive quarterly loss
- US ferrous market exhibits upward pricing pressure: Davis Index