Many paper and paperboard mills are extending the types of recovered fiber they can take in, and as they do so, quality issues can crop up. One of the most difficult materials to handle is wax-coated or wax- impregnated corrugated containers.

While there are some end markets for the material, it is almost universally unwelcome for re-pulping. Many paper companies are using the material as a source for boiler fuel or, in some cases, using the waxed corrugated as a compostable material.
The problem stems from wax’s unsuitability as a material in the making of new paperboard products. Wax, because of its nature as a separator, does not intermingle with the water used to make pulp.
Several companies have taken steps in an attempt to address this issue. The results of experiments, though, have not yet been determined.
THE NUMBERS. Wax-coated corrugated containers are not the most dominant part of the recycling stream. However, because they often can be easily commingled with non-coated streams of old corrugated containers (OCC), the problems with finding and keeping the material out of the pulping stream are significant.
According to several industry sources, about 5 percent of the corrugated produced in the country ends up with some type of wax or other coating. The waxed boxes often end up going into the produce industry, especially grocery stores. However, even at a 5 percent level, this volume is significant.
Kadant Black Clawson, Fulton, N.Y., is one company that has spent a significant amount of time and effort to develop a process to make waxed corrugated a viable material in the paper recycling stream. The company has introduced a system that uses a combination of washers to extract a significant amount of wax from the corrugated. Users of this system have so far been limited.
According to Doug Crow, the technical services application manager for Kadant Black Clawson, "The basic problem with wax impregnated board is that it is slippery, it can get on the machine and can effect the slide angles. You have to find a way to get rid of the wax.
"Black Clawson has come up with a product that aims to do that. With this washing system, a company runs between two and three washers in a series, forming a counter current washing system," Crow explains.
While the system greatly reduces the amount of wax on the cardboard, one of the biggest drivers for a company considering whether or not to pay the additional cost of using this system is the price spread between wax corrugated and conventional old corrugated. "You need a bigger price break to make this system viable," Crow adds.
While mills and recyclers deal with what to do with the waxed corrugated that is prevalent in the waste stream, the ultimate decision is made by the box buyers. Grocery stores, a major end market for waxed corrugated boxes, may be forced to throw away as much as 15 percent of their OCC because of wax contamination. But a number of grocery stores say their use of waxed corrugated is in response to consumer demands.
To replace these boxes, some companies are offering other, more effective ways to coat the boxes. However, these coatings may cost more, something that grocery stores find difficult to pass on to customers.
As things stand now, recyclers typically take in wax corrugated for free (as part of the overall shipment) or a charge is imposed on it.
UPGRADING. While many people look at the waxed boxes as a contaminant, or a less valuable fiber material, Crow notes that the goal of new systems is to have the waxed OCC be considered a better quality material than conventional OCC.
AN ALTERNATIVE TO WAXED CORRUGATED |
While the paper industry seeks to develop a method for handling waxed corrugated boxes, there are several companies that are in various stages of developing a replacement for the paraffin-based coatings. One company that has worked on developing a more recyclable corrugated box has been EvCo Research LLC, Atlanta. A company executive spoke at the recently held National Recycling Coalition’s Annual Congress. Scott Seydel, with EvCo Research, says that the company uses a mix of recycled PET plastics with oils to coat corrugated containers. Because of the composition of the coating, the box is highly recyclable. This, Seydel notes, is a desirable alternative to wax-coated old corrugated containers (OCC), which are typically either landfilled or used for lower-value products such as compost. Despite the possibilities that this new coating holds, Seydel says that marketing the product has been a difficult go. For one, the paper industry is a tradition-bound industry, and many companies are leery of being the first to make the initial foray into the new material. The conclusion, Seydel says, is that "less expensive technology isn’t always welcome. It disrupts long accommodated market shares in mature markets, it devalues production machinery assets no longer needed, and requires subtle but frequent adjustments to customers’ equipment." While there have been successes, the company has shifted greater attention to working with the end consumers, in this case the grocery stores, to show them the opportunities to sharply reduce their landfill costs, while boosting their recycling levels. Over the past several years the company has put together several programs with a number of large grocery chains, including Albertson’s, Publix, and Winn Dixie. Additionally, while some paper companies have been slow to embrace these opportunities, EvCo has developed some products with a number of large paperboard producers, including International Paper, Willamette Industries and The Newark Group. |
The waxed coating, after all, protects the core fiber from contaminants that cheapen the value of the OCC. In this way, some consider the waxed OCC similar to aseptic containers: Expensive to strip away the coating, but holding high quality fiber.
One paper company that has been testing the use of waxed corrugated in its pulping systems has been Domtar’s Cornwall, Ontario, Canada paper mill. The company has been using OCC to make some of its fine papers. According to John Mullinder, the company has been blending a small amount of wax corrugated in with its regular OCC.
While the markets for wax-impregnated OCC have been limited so far, there have been some steps taken to address the situation. The Corrugated Packaging Alliance (CPA), Rolling Meadows, Ill., commissioned a study on the issue of waxed boxes. Hal Tanner, the consultant on the project, said the study looked at four different issues with wax boxes:
1. The quantity of the wax treated boxes;
2. What percentage of the wax boxes were claimed to be re-pulpable;
3. Developing a database of replacements;
4. A list of coated roll producers.
The results of the study are not yet available, although Tanner says that the CPA hopes to have the report completed this month.
Although wax coated cardboard boxes only make up between 3 to 5 percent of the total OCC stream, Mullinder says that as much as 20 percent of the OCC generated in the produce industry is made up of wax-coated boxes.
The level could result in potential contamination of other corrugated boxes.
Recognizing the present difficulties with wax, the CPA, a jointly-sponsored group developed by the American Forest & Paper Association (AFPA) and the Fibre Box Association, has put together some proposed alternatives to waxed boxes. These include the following:
• Using wax only in situations where it offers the only realistic solution;
• Extracting wax from OCC;
• Using additives to alter coatings;
• Developing new re-pulpable coating materials;
• Improving package design;
• Cooling without ice;
• Using modified atmosphere packaging alternatives; and
• Developing better re-pulping technology.
The CPA has found that recent commercialized alternative coatings have yielded promising initial results for shipping products that do not require heavy moisture-barrier case protection. In 2002, the corrugated industry shipped 128,000 tons of these boxes using wax alternative coatings. This reduced the volume of wax treated containers that were unavailable for recycling by 9.1 percent.
At present, box manufacturers are evaluating alternative treatments advanced by nine chemical and coating suppliers, as well as wax alternative-treated con-tainerboard rolls from 10 different suppliers. Further reductions in non-recyclable wax cases may be realized in the near future as more of these alternatives are selectively commercialized. (See sidebar on page S37.)
CURRENT ALTERNATIVES. Supermarkets interested in reducing their current disposal costs for wax treated corrugated are encouraged to investigate recovery facilities that use waxed corrugated for such purposes as composting and making fire logs and fuel pellets. The AFPA, Washington, has published an online directory of waxed corrugated recovery facilities on its Web site (www.afandpa.org, follow the link to Environment & Recycling, Wax Corrugated Recovery Directory).
Ralph Simon, with SP Newsprint, Atlanta, is in a position to see both sides of the story. His company is both a collector of recovered fiber as well as a consumer of the material.
In addition to being the moderator at a panel on the waxed corrugated topic at the 2003 Paper Recycling Conference & Trade Show, he will also be discussing wax issues (among other potential contaminants) at the Paper Stock Industries (PSI) chapter meeting this fall, taking place Oct. 22-25 near San Diego.
Simon remarks that wax is used as leverage between suppliers and consumers, depending on market conditions. "It is an arbitrary deduction by mills when markets are soft. However, when markets are tight, mills will accept the material."
This situation cuts to a best practices and mutual definitions effort that the ISRI (Institute of Scrap Recycling Industries Inc.) PSI chapter and the AFPA are trying to work out.
One way to do this is through the ISRI Scrap Specifications Circular, which defines the grades mills handle as well as contaminants and other definitions.
Simon calls this an important way for both sides to ensure that the other side is cognizant of the expectations between the two parties. While this isn’t a perfect way to reduce or improve the situation, it is an opportune way to reduce the likelihood of a misunderstanding between buyer and seller before material, including wax corrugated, is shipped.
The author is senior editor and Internet editor with the Recycling Today Media Group. He can be contacted via e-mail at dsandoval@RecyclingToday.com.
Get curated news on YOUR industry.
Enter your email to receive our newsletters.
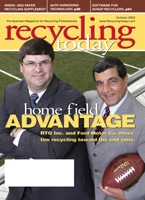
Explore the October 2003 Issue
Check out more from this issue and find your next story to read.
Latest from Recycling Today
- ReMA board to consider changes to residential dual-, single-stream MRF specifications
- Trump’s ‘liberation day’ results in retaliatory tariffs
- Commentary: Waste, CPG industries must lean into data to make sustainable packaging a reality
- DPI acquires Concept Plastics Co.
- Stadler develops second Republic Services Polymer Center
- Japanese scrap can feed its EAF sector, study finds
- IRG cancels plans for Pennsylvania PRF
- WIH Resource Group celebrates 20th anniversary